F4E’s collaboration for 3D printing develops technology and stimulates industry
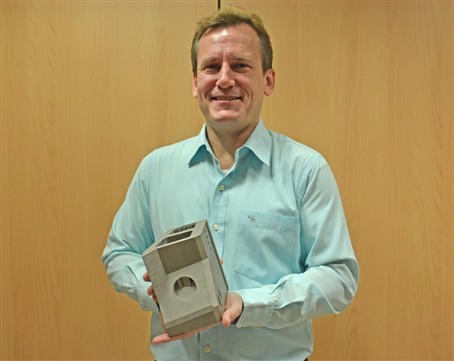

ITER will be made of thousands of highly complex state of the art components which need to fit together like an intricate puzzle. F4E’s fusion engineering design process has long relied on mock-ups and prototypes based on 3D drawings know as CAD, computer-aided designs, to use as a basis for conventional manufacturing. However, F4E has increasingly started to set its sights on a new method known as additive manufacturing (AM) which uses 3D printing, to design and directly manufacture components more efficiently and affordably. Once a CAD sketch is produced, the AM equipment reads data from the CAD file and, depending on method, lays downs or adds successive layers of liquid, melted powder, or sheet material, in a layer-upon-layer fashion to fabricate a 3D object.
“For a complex project such as ITER we have to be versatile and proactive to find options that can save time and cost. This method offers a more efficient and cost-effective way to manufacture complex components. 3D printing lends itself especially well for manufacturing components that are a non-conventional shape or which have complicated internal geometry,” explains Stefan Wikman, F4E Technical Officer responsible for dealing with qualification of additive manufacturing. For this reason, F4E has been working together with a Swedish consortium consisting of Chalmers University, Mid-Sweden University, Swerea KIMAB and Stockholm University, studying the feasibility of manufacturing ITER’s First Wall Beam, the part of the blanket on which the panels will be attached and which has a complex internal geometry for cooling water, thus making it an ideal component to try to find a simple way to manufacture using 3D printing. With three grants with F4E contribution of 50 000 EUR, 245 000 and 250 000 EUR respectively (F4E finances 50% of the costs), the consortium have been carrying out mock 3D printing of the First Wall Beam using a metal powder form of the 316L (N) ITER grade stainless steel (procured by Carpenter Powder Products, Sweden) which the First Wall Beam, like other ITER components, needs to be made up of. The component is gradually built up by successively placing a layer of powder to make up the shape and then melting this layer into place. The advantage of using metal powder form is that loose, surplus powder can be reused to build the next component. The feasibility studies have investigated two different methods of 3D printing: Electron Beam Melting (EBM) and Selective Laser Melting (SLM). EBM can melt thicker layers quickly, but it needs more energy and it must operate in vacuum. In comparison, the laser beam used in SLM, requires less energy, but melts thinner layers.


Image below: After lose powder removal to the right (photos courtesy of Mid-Sweden University).
“We have been checking how well the 3D printing technique works as well as how well the resulting component fulfils the criteria that ITER IO has set for this component in terms of physical properties and mechanical stress tolerances. Components which have been manufactured measure approximately 20 cm in length, 20 cm in width and 30 cm in height”, says Stefan Wikman. The results have proven to be very positive: the density of the 316L (N) components have proven to have a density of 99.9% (SLM method) and 99.8% (EBM method) which means that that material is comparable to conventional material as forgings. In addition, the stress tolerances, especially when using the SLM method, have proven to be very high due to a microstructure of smaller grains within larger grains of the steel that strengthen the steel significantly.


Image below: Magnification of sub-grains inside these larger grains to the right comprising a grain in grain structure (photos courtesy of Stockholm University).
The encouraging results from the feasibility studies have led to F4E further developing relationships with industrial liaison partners that could potentially could upgrade AM facilities to accommodate 3D printing of larger stainless steel components in this fast growing market (perhaps even up to metre scale). As a result of the presented work F4E’s leading position in Europe with regards to qualifying 3D printing techniques of larger stainless steel components has the potential of a spin-off effect to other fields other than the energy sector.
The results generated through F4E’s partnership with the Swedish consortium and the feasibility studies have generated several scientific papers and received international recognition. “Additive manufacturing and 3D printing offers a paradigm shift in terms of manufacturing technologically complex components and is changing the way designers dealing with complex machines such as ITER are thinking. We are no longer bound to using conventional shapes, we can disregard manufacturing complexity and explore new solutions which were previously not possible to fabricate by conventional machining”, says Stefan Wikman “The technique in itself has numerous spin-off opportunities. For example, today 3D printing can replicate intricate human body parts for surgical implants and in a near future, it could be used to fabricate advanced bigger structures suitable for power plants and car engines”, he concludes.