Manufacturing of the Blanket First Wall semi-prototype completed
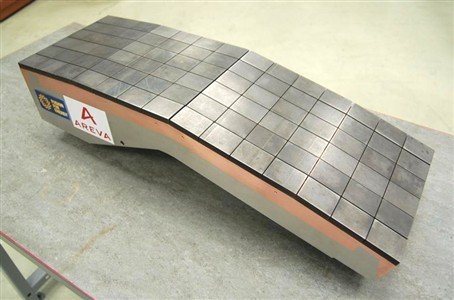

A so-called semi-prototype of the Blanket First Wall (about 1/6 of the dimensions of a full-scale First Wall Panel) has recently been manufactured. This activity, based on specialised know-how and skills owned by only a handful of European companies, has been completed in roughly two years by French company AREVA.
The first wall panels are 1m x 1.5m detachable elements which together with the shield block (a block of stainless steel on which the first wall panels are fixed) form the Blanket modules. The Blanket is the part of the ITER machine that acts as a first barrier and protects the vacuum vessel, which is the heart of the ITER machine, from the neutrons and other energetic particles that are produced by the hot plasma. The First Wall consists of 440 panels, of which F4E will provide about half. Depending on the location of the modules in the Blanket, different design parameters are necessary. F4E is providing the Normal Heat Flux panels (the Enhanced Heat Flux panels will be provided by the Chinese and Russian Domestic Agencies). Normal Heat Flux panels are designed to withstand heat fluxes of up to 2 MW per m², whereas Enhanced Heat Flux panels can withstand heat fluxes up to 4.6 MW per m². The panels are made up of beryllium tiles which are bonded with a copper alloy and 316L (N) stainless steel using Hot Isostatic Pressing (HIP), a method that involves pressure generated by gas in order to compress the metals together homogenously from every direction. During operation, the ITER First Wall panels will be cooled by pressurised water.
The completion of the semi-prototype moves F4E a step closer to obtaining qualification by ITER IO for the manufacturing of the actual Blanket First Wall. Qualification is necessary for all components in the ITER machine and involves building and testing prototypes in order to gain and consequently demonstrate knowledge and practical skills for the manufacturing of the actual component.
With the manufacturing of the semi-prototype now completed, the next step will be its high heat flux testing. This involves subjecting the surface of the semi-prototype to an electron beam capable of applying the same heat flux the First Wall panels will endure in the ITER machine, resulting in the panels having a beryllium surface temperature of around 400°C during testing. F4E has awarded the grant for the high heat flux testing to German research centre Forschungszentrum Jülich and the testing is scheduled to be completed by the summer of 2014.
The associated Procurement Arrangement for the procurement for the actual First Wall Panels to be used in the ITER machine is scheduled to be signed in early 2015.