Panoplies of steel for Europe’s Toroidal Field coils
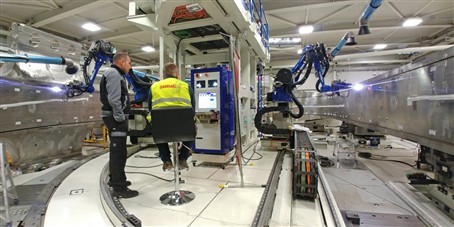
Technical staff following the welding of the ITER Toroidal Field (TF) coil cases. The work is performed by automated robots at the SIMIC factory, Porto Marghera, Venice, Italy. Ten of the 18 TF coils will be delivered by F4E and its suppliers.
The Toroidal Field (TF) coils can also be described as the magnets of all magnets that will operate in ITER. They are the ones that will confine the super-hot plasma within their powerful magnetic field. When powered with 68 000 A they will generate 11.8 Tesla—about 1 million times stronger the magnetic field of the Earth. A total of 18 magnets of such kind will operate in ITER with Europe responsible for manufacturing ten of them and Japan for eight plus one spare.
The fabrication of Europe’s TF coils started in La Spezia, Italy, at the ASG Superconductors factory, where technicians rolled out the entire fabrication process starting with the spooling of the conductor till the production of the inner-structure of the magnet, known as winding pack, measuring 14 m high and 9 m wide.
But to become a fully-fledged ITER magnet, the massive component needs to go through as series of cryogenic and electrical tests and to be inserted into its coil case, which is welded, gap-filled with resin, and machined to make sure its steel panoply is tight and well fitted. These final fundamental steps are taken at the factory of SIMIC, Venice, Italy, where the pace of activity has accelerated. The staff of SIMIC and F4E work round the clock to make sure that the final result is in compliance with strict specifications required for the ITER device. The massive superconductive coils occupy different tooling stations. And in a seamless sequential manner they move from one machine to another until they reach their final stage and are packed to be delivered to the ITER site.

So what is the latest in terms of their fabrication? So far, four winding packs –
the inner-core structures of the magnets – have successfully gone through the cryogenic tests. Out of them, two have been inserted into their coil cases. Welding has been completed for one and in the case of the second, the process is almost completed. “We are talking of six months of work because we have long welds running roughly 5 km. The job is performed both manually and with the help automated robots. Due to the risk of distortions resulting from welding, technicians need to be extremely meticulous when they perform this task,” Boris Bellesia, F4E’s Project Manager for this contract from the area of Magnets, explains. And then comes the tricky part of gap filling, where resin needs to be injected inside the massive vacuumed structure to create continuity between the winding pack and the coil cases, ensuring that there is no gap. “On the assembly rig, the station where also insertion and welding are performed, this delicate step also unfolds. SIMIC has developed a station with 90 variants of different angles to tilt the TF with a degree of uncertainty of less than 0.1 mm,” he continues.

Gap filling for the first TF coil has been successfully completed, a process closely followed by Piergiorgio Aprili, F4E Technical Support Officer for Magnets, who takes the time to explain what is entailed. “The coil is tilted with an angle of 5 degrees in order to inject approximately 1 500 l of resin from the lowest point. During this process the gap between the winding pack and the coil case is in vacuum. Then, the TF coil is covered with thermal mats, containing heaters to raise the temperature of the coil case, and in parallel, current is circulating in the winding pack to control its temperature. Afterwards, we inject resin initially at 40 °C. Once the filling is completed the temperature of the coil reaches 65 °C so as to achieve a jellying effect. As the temperature rises, the resin hardens. The jellying cycle lasts 24 hours, followed by a curing cycle at 75 °C for another 24 hours,” he explains.

Behind these technical achievements there is project management, careful planning and management of resources. Paolo Barbero, SIMIC Project Manager, explains in in more detail the technical achievement and the contribution of the workforces. “We are very satisfied with the results obtained during the welding operation. Over 100 m of complex welding were completed, and achieved very high quality levels by working three shifts. The gap filling of the first TF coil with resin was a delicate operation, which took us two weeks including weekends without stopping. The second TF coil is almost welded. We were able to build on the expertise from the first TF and replicate the good results.”
Alessandro Bonito-Oliva, F4E Magnets Programme Manager has been following the evolution of the works from the start. Together with his team, he has invested time in identifying the best possible options to reconcile schedule and the complex specifications. “The results we have obtained so far are not just the outcome of good technical solutions. In essence, they represent ten years of hard work and careful planning. Our strategic thinking helped us to analyse upfront, and to define the proper implementation strategy. This, together with our capability to react, adapt and to manage in a timely manner adverse situations during the implementation of the contracts, have been essential to the results obtained so far,” he explains