Winding completed for ITER Poloidal Field coil prototype
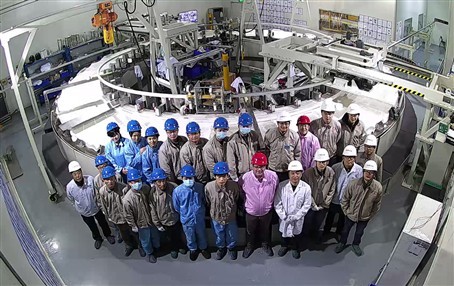

To confine ITER’s superhot plasma, expected to reach 150 million ˚C, powerful superconducting magnets will be needed. The first layer will consist of Toroidal Field (TF) coils, which will entrap the hot gas, to keep it away from the walls of the vacuum vessel. The second layer will consist of Poloidal Field (PF) coils, which will embrace the TF coils from top to bottom, to maintain the plasma’s shape and stability. Europe is responsible for five of the six PF coils: four of them will be manufactured in a facility located on the ITER site and another one in China, following an Agreement signed with Europe. Russia is also responsible for the fabrication of one PF coil.
Before “real” manufacturing activities kick off, trials have to be conducted in order to qualify tooling and fabrication processes. Technical experts document every step of the way and draw lessons. This is the learning curve which will teach us how to develop a sound method of production. The team behind the PF coil manufactured in China at ASIPP (China’s Institute for Plasma Physics), on behalf of Europe, has celebrated a milestone: a full-scale prototype of a double pancake has passed the final winding qualification test. What is a double pancake? Two layers of conductors wound like a massive pancake. And why is it important? Because real manufacturing can start soon!
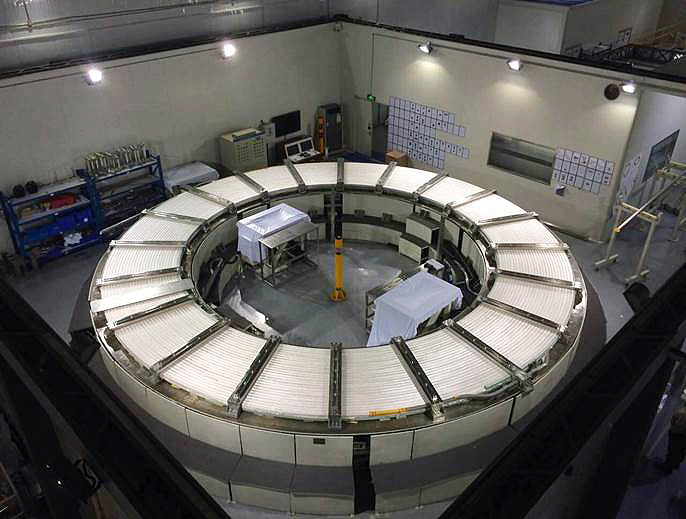
How did we get here? Trials started early in autumn last year and reached a peak towards November. The new year started with the completion of the trials in ASIPP when the component was moved from the winding facility to the termination and joint preparation areas. Winding the coil took roughly two months, including the manufacturing of the Helium inlets, the entry points of cold Helium inside the massive magnets. A team of 20 workers, engineers, inspectors and F4E staff have been working on extended shifts to meet this objective. The insulated prototype, resembling a massive white ring, has an inner diameter of 7.1 m and an outer diameter of 10.3 m. A sequence of steps has led to this final result. First, the conductor had to be despooled, straightened, cleaned and sandblasted. After rinsing and drying, the conductor was bent, wrapped and insulated using fiberglass and kapton tape. The Helium inlets have also been manufactured at the middle point of the winding.
What is coming next? The team will have to complete the terminations and perform the vacuum pressure impregnation of the prototype. In the meantime, winding of the first “real” double pancake can start early in March, after all the relevant manufacturing, qualification activities and reporting have been completed and approved.
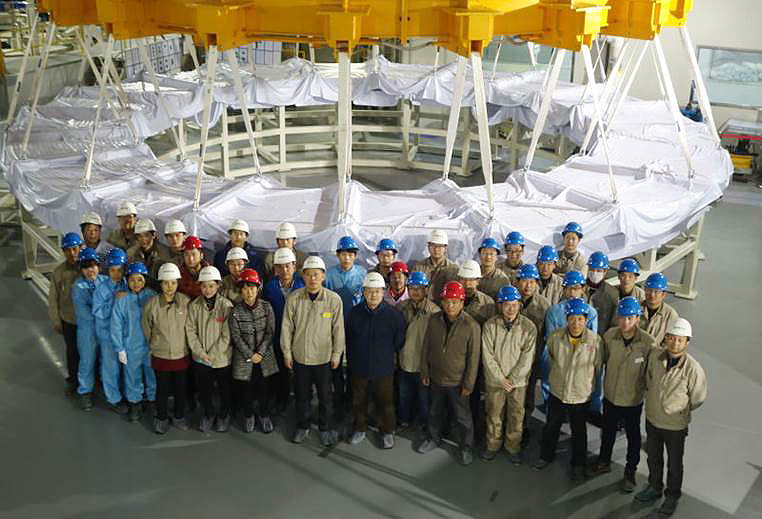