Diagnostic sensor prototypes successfully manufactured
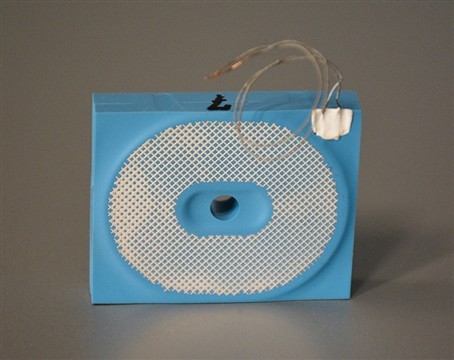

Work is progressing in the field of ITER Diagnostics under F4E’s collaboration with German company Via Electronic, which is manufacturing prototypes of sensors to be installed inside the heart of the ITER machine, the vacuum vessel. More than 200 such sensors will measure the local magnetic field in ITER during operation, contributing vital information for control of the plasma.
Each prototype consists of 34 layers of ceramic, 30 of which contain a screen-printed spiral coil circuit made out of pure silver (the remaining layers of ceramic provide external protection and electrical screening in the form of a printed grid on the external faces of the device). The individual spirals, which have a width of 400 µm and a height of 12 µm, are connected together with inter-layer ‘vias’ so that the whole assembly forms a single pick-up coil. The manufacturing technology is termed “Low-Temperature Co-fired Ceramic” (LTCC) and offers a very robust product because the sensor is fully encapsulated in ceramic. “It’s important for these sensors to be particularly robust as they will be located in a very harsh environment, close to the plasma, with extremely limited access once ITER operation begins”, explains Shakeib Arshad, F4E’s Technical Officer for this development. “Although this type of technology has been used extensively in other applications, for example in medical equipment, it is unconventional in fusion because simpler technology was adequate in the smaller tokamaks built up until now.”
The collaboration between F4E and Via Electronic covers the production of 40 prototypes. This follows the manufacture of a first batch of prototypes by Via Electronic in 2014 which led to several refinements to the original design. In the quest to further optimise the design, eight variants are being produced with different wiring schemes and electrical screen thicknesses.

F4E is also preparing two additional contracts for manufacture of similar prototypes by other suppliers. “As the next step, these prototypes will be irradiation tested in a fission reactor, in order to establish their performance in an ITER-like environment”, says Sandra Julià Torres, the F4E officer responsible for the prototyping contracts. “Irradiation testing is costly and the results can depend on subtle manufacturing details. Prototypes from several manufacturers are desirable for this reason.” The irradiation testing will be carried out by the Nuclear Research and Consultancy Group (NRG) in the Netherlands and the Centrum výzkumu Řež s.r.o. (CVŘ) in the Czech Republic. Additionally, a computer model is being developed by the Belgian Nuclear Research Centre (SCK-CEN) in order to help with interpretation of the irradiation tests.