A step closer to completing the MITICA cryopump
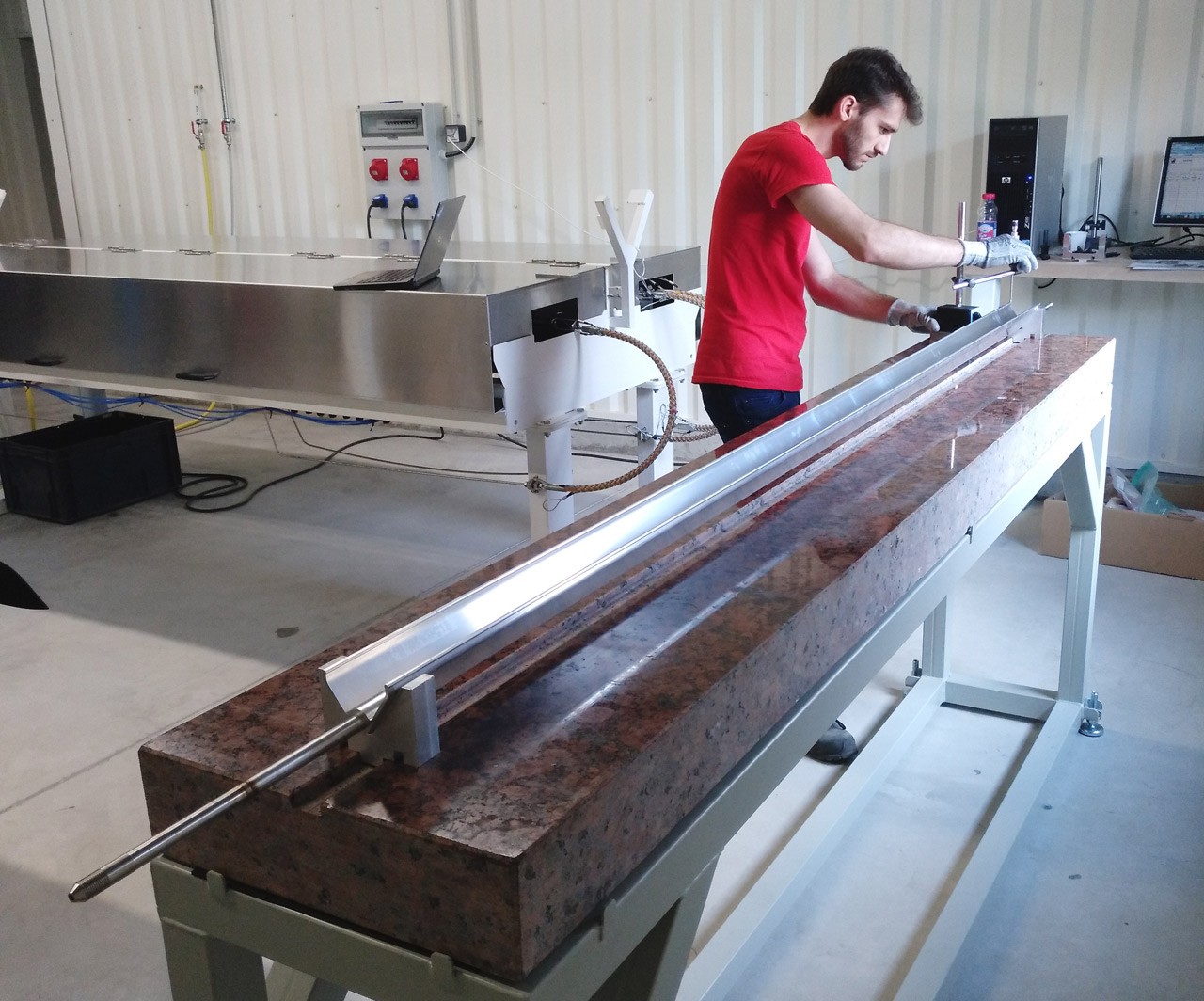
A technician performing a metrological survey on a V-shaped thermal radiation shield, May 2019.
The ITER plasma will have to reach 150 million °C. To this end, a powerful heating system will be deployed. A set of neutral beam injectors will accelerate negative ions at 1 MV, reaching a speed that no other neutral beam system has ever provided. Once accelerated, they will be neutralised before they are injected into the ITER vessel to impact with the particles in the plasma, and heating it as a result. MITICA is the test facility located in Padua (Italy) devoted to the validation of the technology required by the neutral beam systems.
A key component of MITICA’s neutral beam injector is the cryopump, which F4E is in charge of procuring. Ravanat was awarded a contract worth 1 million EUR to produce the main components of the cryopump: the cryopanels and the thermal radiation shields. Experts working from May 2018 to December 2020 delivered 285 cryopanels and 315 thermal radiation shields that complied with the stringent conditions for MITICA.
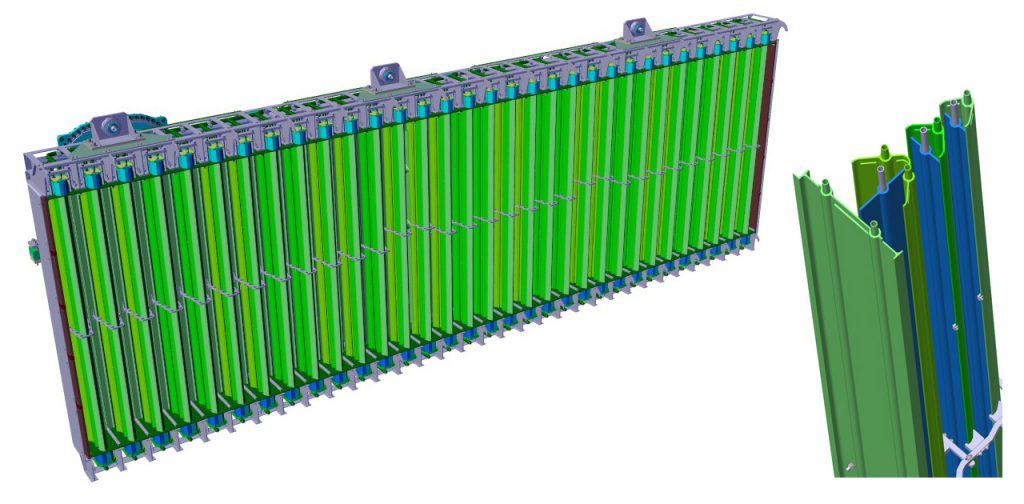
The cryopump will be located on the walls of the 10-metre vessel through which the particles travel before they are injected. It serves two main functions. First, its cryopanels, at a temperature of 4 K (-269 °C), provide the vacuum level needed for operation. Second, the cold surfaces of the cryopanels trap unwanted particles off the beam. The thermal shields at 80 K (-193 °C) act as barriers to keep the inner cryopanels at the appropriate temperature.
The fabrication process of both the cryopanels and thermal shields is quite delicate. “They are the result of introducing one or two stainless steel pipes in an aluminium profile and applying the appropriate hydrostatic pressure so that the pipe is deformed and gets attached to the profile. The goal is that when releasing the pressure (around 2200 bar, the pressure of more than two thousand atmospheres), the two surfaces are perfectly bonded,” explains Luis Mora, F4E Cryoplant & Fuel Cycle Technical Project Officer.
David Falque, Ravanat Technical Manager, and Anne-Sophie Guichou, Quality Manager, stress the challenges they had to overcome. “To be in accordance with the technical specifications of the project, we faced technical difficulties which brought us to develop specific processes such as an automatic high pressure expansion bench or chemical polishing treatment in collaboration with new subcontractors who have played a real partner role.”
“Indeed, this project presented a number of challenges that nobody had foreseen at the time we signed the contract with Ravanat, especially for the polishing process of the aluminium panels,” agrees Aurélien Rousseau, F4E Cryoplant & Fuel Cycle Project Manager, who followed the implementation of this contract. “We managed to successfully resolve those issues thanks to the collaborative mindset that had been adopted by every member of the project team, including people from Ravanat, Aluminium Ferri, RFX, ITER Organization and F4E,” he concludes.
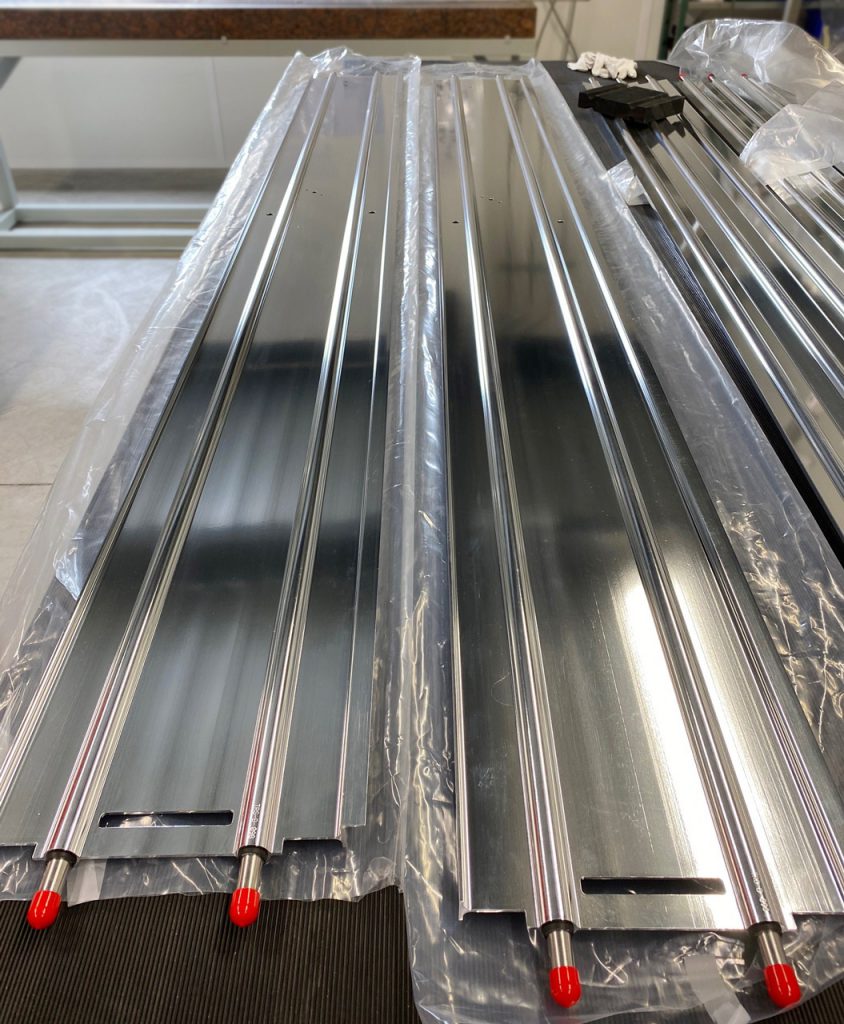
The next steps before the actual assembly of the cryopump will be to blacken the thermal shields and to add charcoal coating to the cryopanels. All the expertise acquired along this process in MITICA will certainly pave the way for the fabrication of the final neutral beam system for ITER.