All forgings and plates for European vacuum vessel sectors have been delivered
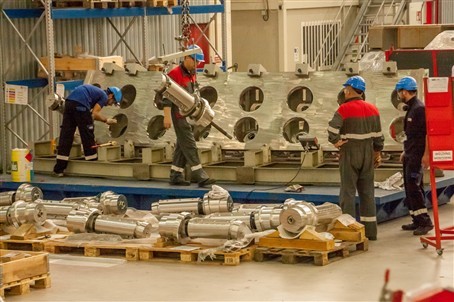

Five sub-contractors, namely Acciaierie Valbruna (Italy), Forgiatura A. Vienna (Italy), Industeel (France), Rolf Kind GmbH (Germany) and ThyssenKrupp (Germany), have produced and delivered all the remaining forgings and plates which will be used on the five vacuum vessel sectors (out of the total nine) that Europe is contributing to the ITER project.
All in all, for the 5 EU sectors, around 1100 forgings (big blocks of 316 LN ITER grade stainless steel) with a total weight of approximately 1900 tonnes, have been delivered. This delivery comprises individual forgings weighing up to 3750 kg depending on where in the vacuum vessel it is to be placed. The forgings come in various different shapes and sizes (round bars, rectangular bars, square blocks etc.) and will at a later stage be machined into subcomponents which will be assembled together to make up the remaining vacuum vessel sectors.
Around 150 plates boasting a total weight of 1120 tonnes have also been delivered. These plates (flat stainless steel slabs which have rolled flat to become plates in various different thicknesses) will be used to manufacture the inner and outer shells making up the inner and outer walls of vacuum vessel sectors.
The forgings and plates have been manufactured by mixing pellets of materials such as chromium, nickel with low alloyed steel in order to produce 316 LN ITER grade stainless steel which is low on carbon and high in nitrogen. “This is an exceptionally strong, corrosion resistant high-quality stainless steel which has good weldability. It has been especially selected and developed because of its suitability for a fusion machine such as ITER”, says Stefan Wikman, F4E Technical Officer dealing with materials. The mixture for the forgings is heated to a temperature of approximately 1,500º C and poured into block moulds for cooling. “The next stage is what we call hot pressing: the steel block is shaped by being heated to a temperature of approximately 1,000 degrees C and then hammered into shape using a large steel hammer, pressed or rolled. The plates also start as stainless steel slabs that are rolled flat using high temperatures and equipment to become plates in various different thicknesses,” explains Vassilis Stamos, F4E Technical Officer, responsible for material fabrication procurement for the nuclear fabrication of the vacuum vessel sectors.
The forgings and plates are now at the Mangiarotti S.p.A and Walter Tosto S.p.A premises for cutting and machining into desired shapes and sizes. “We are pleased that delivery of the vacuum vessel forgings and plates has been finalised as this marks the completion of another step to streamline the fabrication of the ITER vacuum vessel sectors, the heart of the ITER machine”, says Francesco Zacchia, Project Manager for F4E’s Vacuum Vessel team.