AI at the service of ITER and nuclear engineering
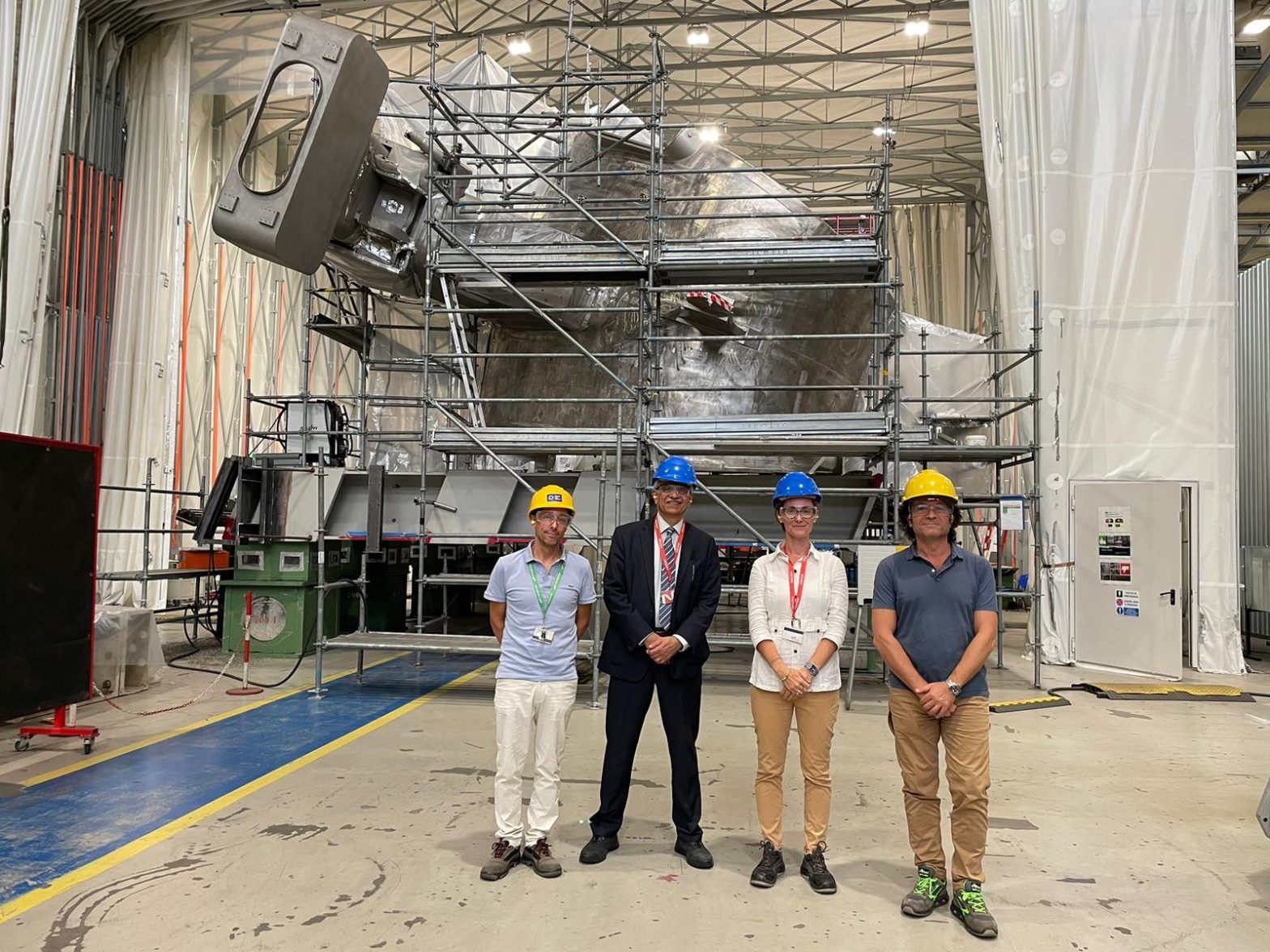
(L-R) A. Dans, N. Prinja, M. Ortiz de Zúñiga, A. T. Megna in Mangiarotti, where Europe’s sector 5 of the vacuum vessel is manufactured. ©F4E
It was only a matter of time for ITER, one of the biggest international technology projects, to cross paths with Artificial Intelligence (AI). There has been a lot of speculation about its possible impact, as countries are competing to capture its potential. For instance, during this year’s World Economic Forum an AI Governance Alliance has been launched bringing together governments, civil society, industry, and academia to ensure that there this so-called revolution benefits all.
While the rest of us are trying to make sense of the changes that it will bring, a team of experts in F4E has been working in this field for more than two years to test the contribution of AI in nuclear engineering. María Ortiz de Zúñiga, Senior Technical Officer, and Cristian Casanova, Vacuum Vessel Programme Manager at the time, decided to innovate by conducting a pilot study with Europe’s vacuum vessel sectors. The wealth of data previously collected from welds with defects, would be used to train AI in order to predict which welds in progress would present defects. Without knowing exactly where this would take them, they entered a universe of combined algorithms and prediction models. Thanks to this pilot project they managed to harvest new data, improved the level of precision for possible non-conformities and identified impressive time gains. The transfer of knowledge resulting from this initiative and the take aways were valuable. How did they decide to embark on this journey?
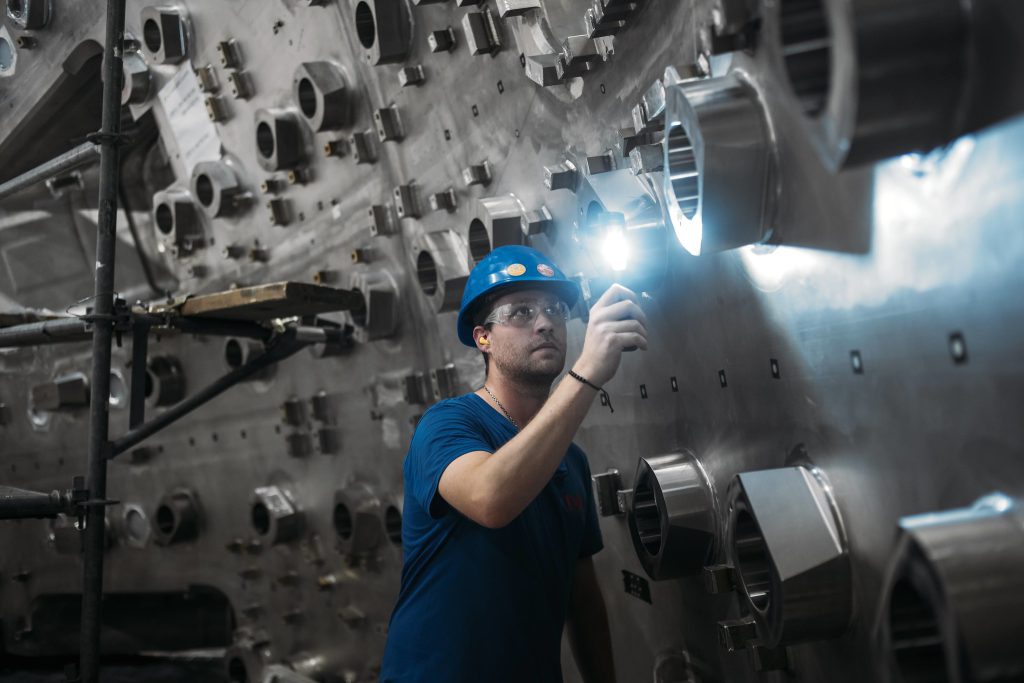
The ITER Vacuum Vessel will house the fusion reaction. It’s a double-walled container, in the form of a torus, made of nine sectors. Europe is responsible for five of them, and Korea for four. Each sector is 12 m high, 6.5 m wide, 6.3 m deep. F4E is working with the consortium of Ansaldo Nucleare, Mangiarotti, Walter Tosto (AMW). It’s a partnership that brings together at least seven companies located in Spain, Germany, Italy, and involves more than 200 employees. The works performed in each factory range from welding and machining to quality assurance checks, ultra-sonic tests, assembly, and the transportation of the components The pieces that make each sector, known as segments, need to be welded in order to become one. The total length of welds per vacuum vessel sector is in the range of 1 km, which amounts to 10 059 welds! In other words, there is room for human error and non-conformities. But there is also an opportunity for improvement and risk mitigation given the amount of data we have. Could they provide us with new intelligence?
“Big Science projects like ITER offer a wealth of data which is ideal for AI. They provide us with a one-of-a-kind opportunity to learn, train, extrapolate and apply these skills in other fields of manufacturing. There are very few attempts in bringing AI in nuclear engineering, so we decided to give it a try and break new ground. We are the first ITER party to test the waters and since this pilot project, there has been an unprecedented interest and enthusiasm harnessing its potential,” explains María Ortiz de Zúñiga.
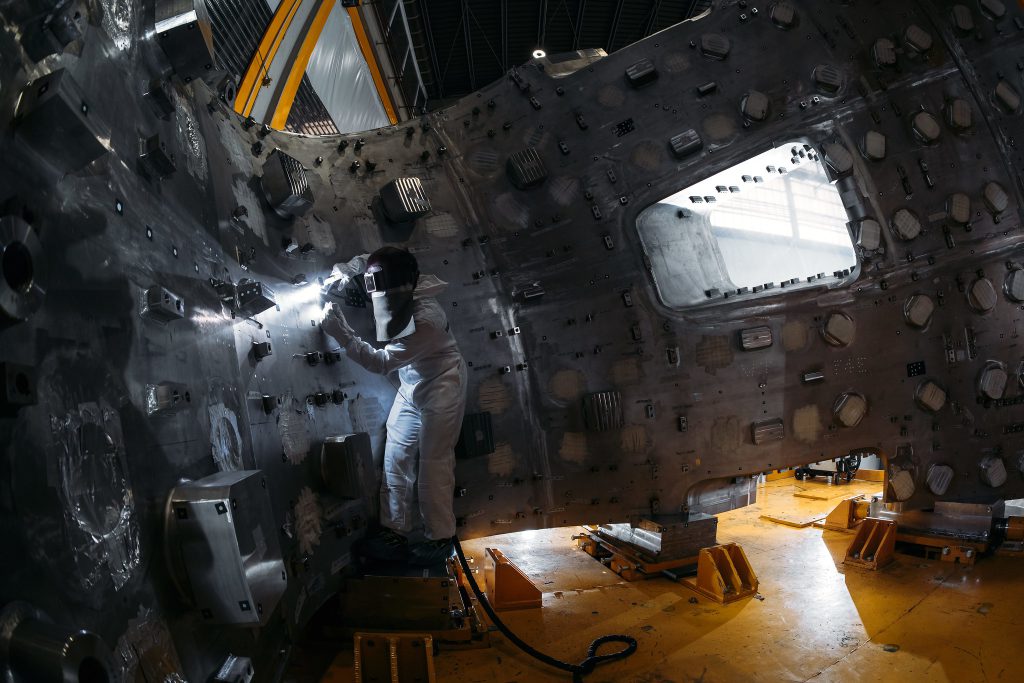
Electron beam welding is the preferred technique used for the vacuum vessel. Data collected from 2000 welds were used to train an AI model and subsequently to test its predictive accuracy. Would the model match the results of the inspectors conducting the checks? The model predicted with 100% accuracy how many of the 100 welds in progress would pass or fail conformity checks. Similarly, tests were performed using data from Tungsten Inert Gas (TIG) welding. These are high quality welds ideally used for stainless steel. Data were collected from all workshops where works were performed. The AI model was trained using information from 2662 welds without defects and 266 with defects.
The application of AI can also be interpretative in understanding data. The F4E team checked the values collected from Phased Array Ultrasonic Testing (PAUT) to validate results. Basically, beams are sent on the surface of a component by a probe at an angle allowing us to check any defects as the ultrasonic waves bounce back. The process is costly, it can take from one day to a week depending on the complexity of the weld and is carried out by an expert using images. There is, however, a 3% probability for a human not to spot the defect. With AI this margin of error is eliminated, and the model provided a high level of accuracy scoring 96% completing the task in a matter of minutes. In nutshell there were gains in time and accuracy, and in the meantime a decrease in costs and human error.
“This is by far one of the most innovative initiatives we took in Europe’s vacuum vessel team, which will have long-lasting implications in other areas of work. We took a decision at the time to start this project and take advantage of the possibilities offered by AI as a first step. We started planting the seeds towards a future application to other components to be manufactured and delivered to ITER. F4E needs to embrace and harness the full potential of the AI,” explains Cristian Casanova.
Thanks to this pilot project, F4E was able to draw some key lessons in manufacturing with significant implications for industry. The first AI is here to stay. It is therefore in our interest to become more familiar with its potential to obtain quicker forecasts in a more accurate manner. One of the key lessons is the importance of good quality data and the time required to collect them. The analysis, together with the design of the right AI model, and its training, are fundamentally important. In essence this means that we need to adopt a different mindset. We need to stop thinking of data in very mechanical terms as a necessary evil and start thinking on how to make use of their full potential.
This AI initiative performed on Europe’s vacuum vessel sectors, was entirely driven by F4E, and counted with the full support of its governance. They saw an opportunity to understand its potential and assist European industry in manufacturing. During this year’s World Economic Forum, Open AI CEO Sam Altman, tried to manage expectations on the impact of AI. He explained that the so-called revolution may not be as shocking as once claimed, and jobs may change a lot less than we think. To meet, however, the consumption needs of AI models and achieve breakthroughs, we will need fusion energy. If he’s right, Europe has showed real business acumen and strategic foresight.