F4E delivers electronics to monitor ITER’s magnetic field
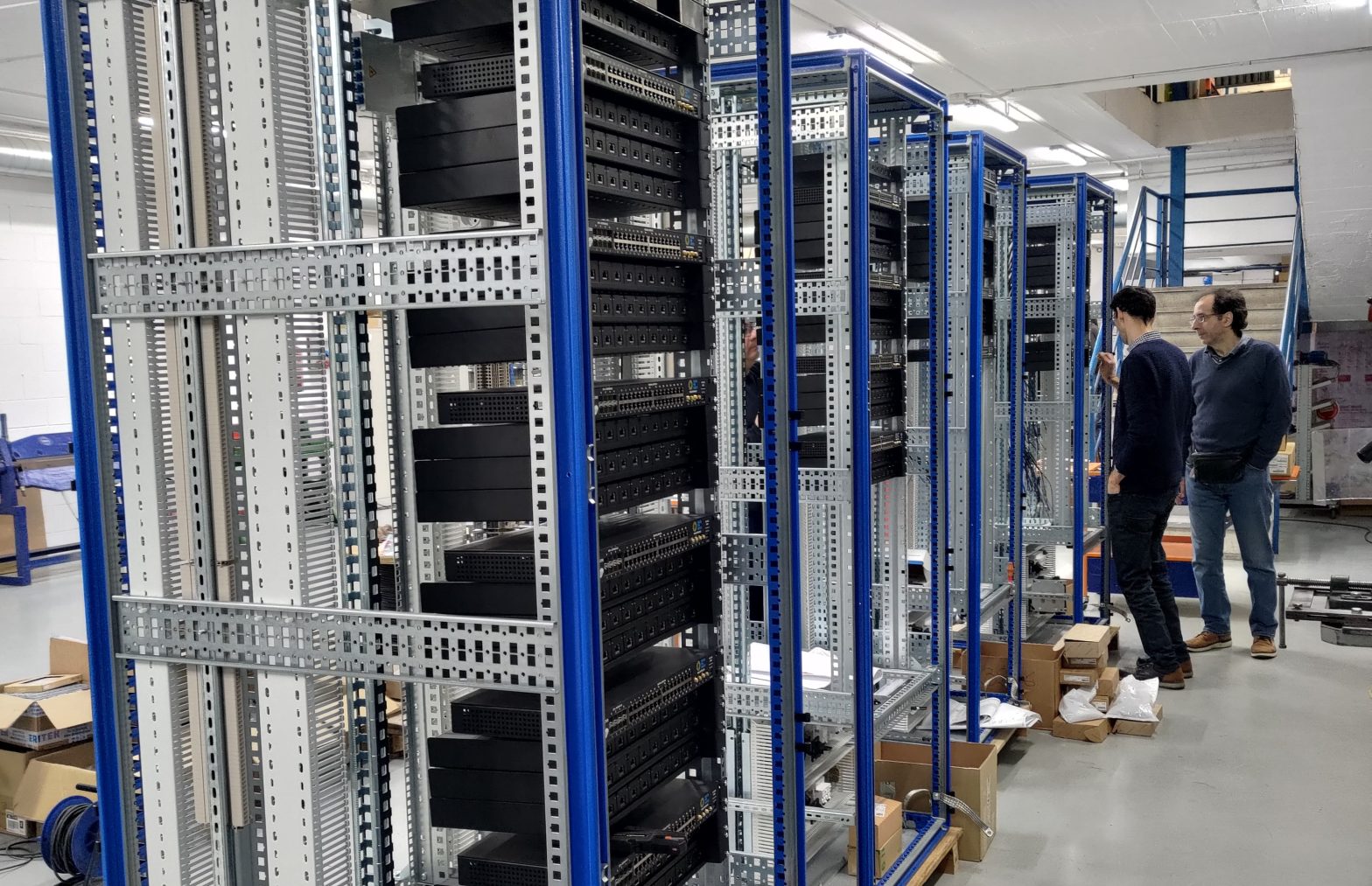
F4E colleagues revise the electronic cabinets during assembly with the electronics (black boxes) already installed. ©F4E
ITER will use powerful magnets to confine its super-hot plasma. The device needs to monitor the magnetic field in real time to ensure the plasma remains stable and optimise the conditions for the fusion reaction. To do so, it will use the so-called magnetics diagnostic. These comprise a network of sensor coils inside the device that capture any changes of the magnetic field. Their signals will be transmitted via electronic equipment, and specialised codes will then translate the vast physics data into information for automatic monitoring and for experts to analyse. In addition to most of the sensors, Fusion for Energy (F4E) is providing the electronics and the software for the magnetics diagnostic.
The electronics have been completed. During the last ten years, F4E has been collaborating with GTD and several subcontractors, to develop and manufacture this system, made of thousands of components, kilometres of cabling, and advanced software. Whilst some of the equipment was standard, other parts were specifically designed to meet ITER’s unprecedented requirements.
One of the most critical electronics were the integrators. Around 1700 integrator units will measure changes in the magnetic field. “We needed an extraordinarily stable integrator, able to work with precision in the long pulses of ITER. There weren’t any on the market, so we worked with IST and CCFE to develop an upgraded version for ITER,” asserts André Neto, technical officer following the contract for F4E.
The manufacturing of these custom-made electronics was coordinated by ALTER. Despite their complexity, the biggest challenges came from the procurement of conventional components. “Post-pandemic worldwide shortages in the supply of electronics threatened to delay the project. However, thanks to intensified efforts in redesigning and sourcing, we managed to move forward and deliver on time,” recounts Mario Rueda, Project Manager at ALTER.
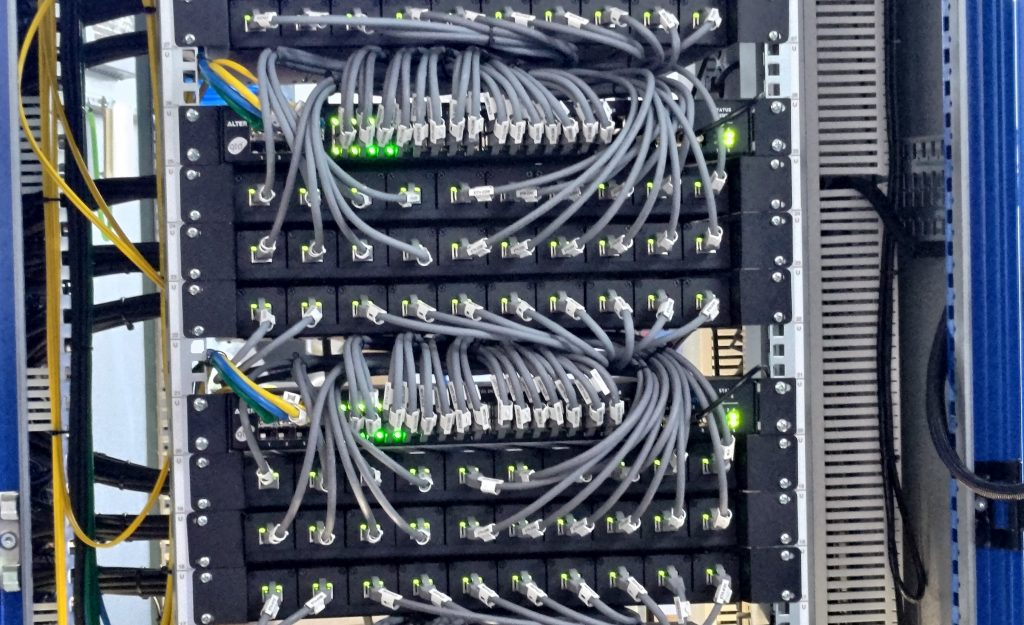
In parallel, GTD and F4E ensured the success with a marathon of tests on a sample of the systems. After months of preparation, the teams spent a full day running simulations, using the firmware and software developed by GTD to control the electronics. “Achieving this milestone took a remarkable combination of expertise, from IT and electrical engineering to commercial and project management. Our excellent teamwork with F4E and the subcontractors was essential for the timely handover of the electronics to ITER,” celebrates Waldo Méndez, Project Manager at GTD.
The electronics have been assembled in 17 cabinets, each roughly the size of a telephone booth. Simsa, based near Barcelona, was tasked with their assembly by ITER Organization. From there, F4E sent the first batches to ITER this summer. The plan is to finish deliveries and site testing in the next months. The cabinets are gradually being installed inside the ITER Diagnostics building, located next to the facility housing the device.
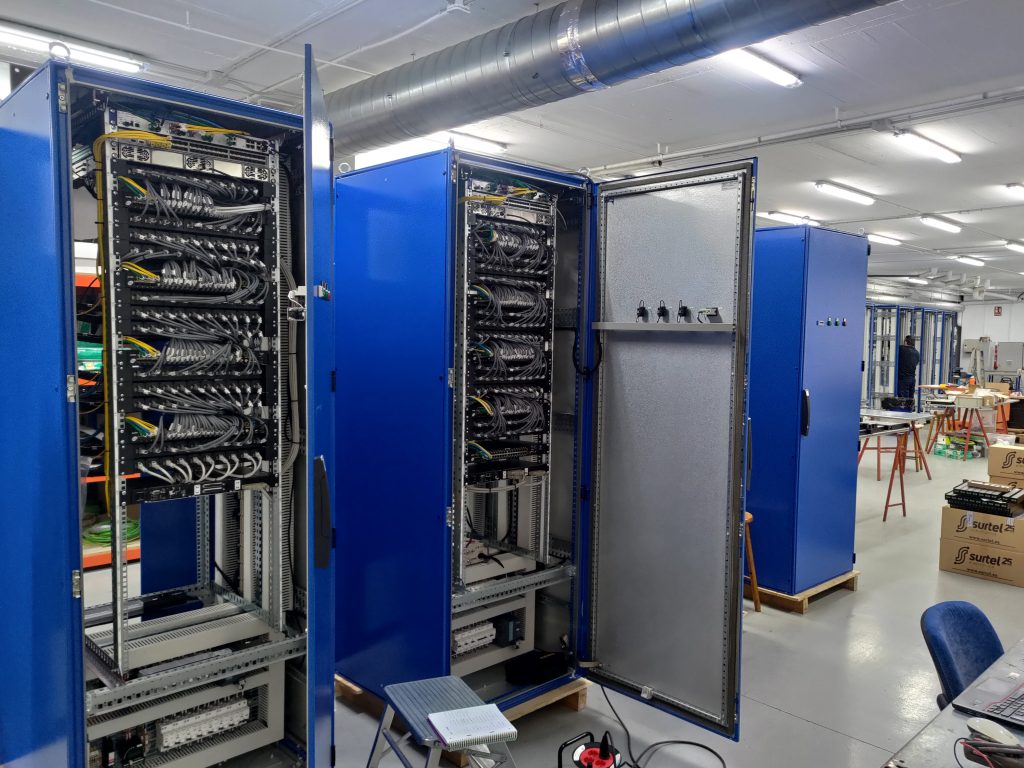