Europe delivers magnetic sensors for ITER Vacuum Vessel
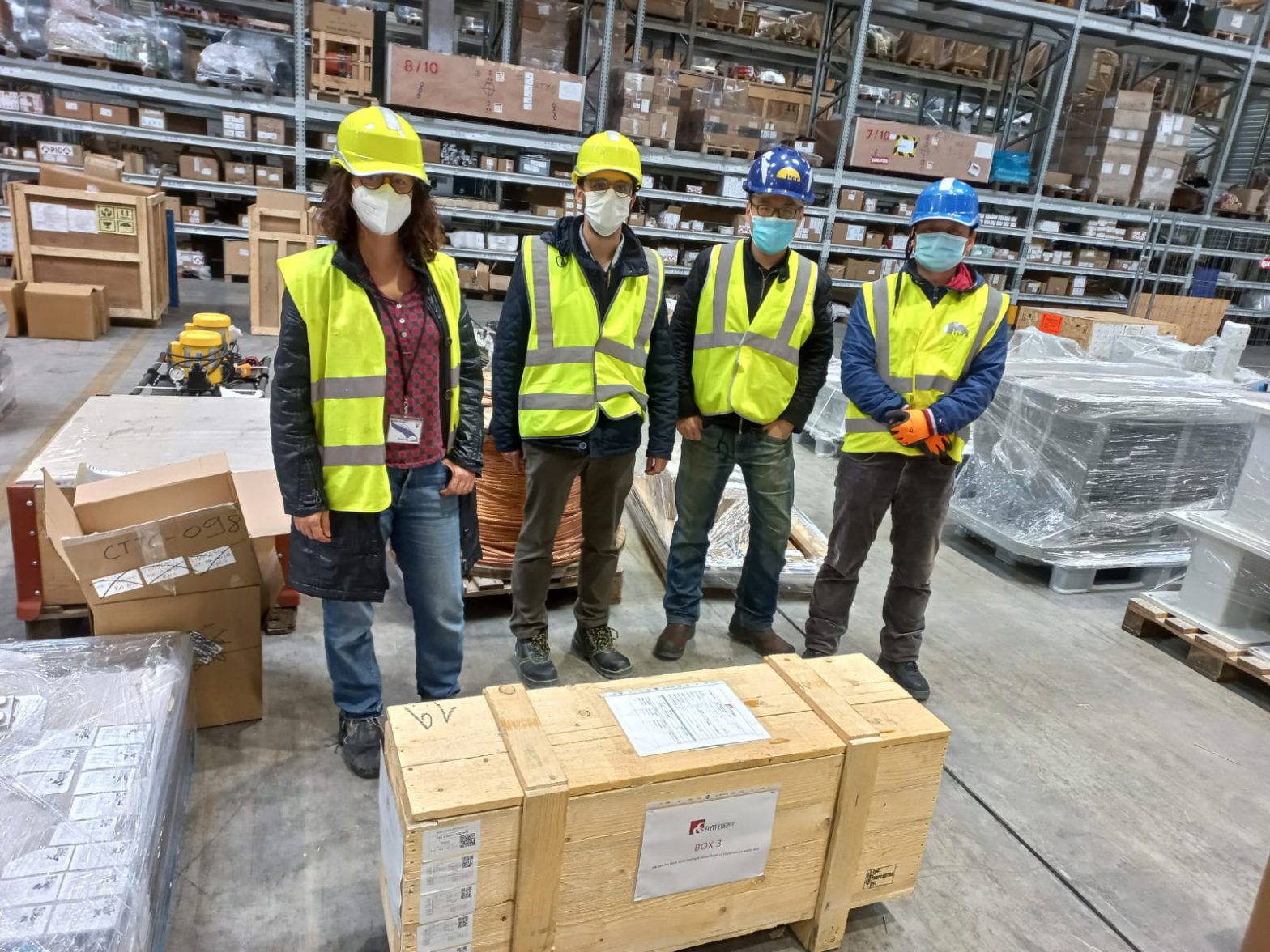
A total of 144 inner vessel magnetic sensors has been delivered to ITER Organization. Behind one of the boxes containing them, from left to right, Paz Casas (F4E), Francisco Fernández (Elytt), Yunxing Ma (ITER Organization) and Ce Ye (ITER Organization). © F4E
The ITER Poloidal Field coils and Toroidal Field coils are massive magnets that will help scientists confine the super-hot plasma ensuring its shape and stability. However, these will not be the only coils in the machine. Spread throughout the vacuum vessel, there will be hundreds of little coils measuring different plasma parameters. Among them, the Inner Vessel Coils, which will provide information on the changes in the magnetic field over the course of the experiment. Europe has delivered to ITER Organization a first batch of these sensors.
In total, there will be around 450 sensors to be installed on the inner surface of the ITER Vacuum Vessel, behind the blanket modules facing the plasma. In spite of the relatively protected location, engineers needed to address some of the challenges resulting from the harsh operating conditions. The sensors, which fit in the palm of one’s hand, will perform measurements that are essential to determine some key parameters for plasma operation: the shape of the plasma, its energy and instabilities among others.
The production of these sensors results from the collaboration of several companies and a fusion laboratory, which joined forces to deliver these extremely delicate components. How did it all start and who did what?
In 2018, Europe started the production of this equipment. Sgenia Industrial was entrusted with the manufacturing of several kinds of platforms that will hold the sensors. The fixation systems to attach the sensors to the inner wall of the vacuum vessel were delivered to ITER Organization last year, while the manufacturing of five types of housings for the sensors started in 2019.
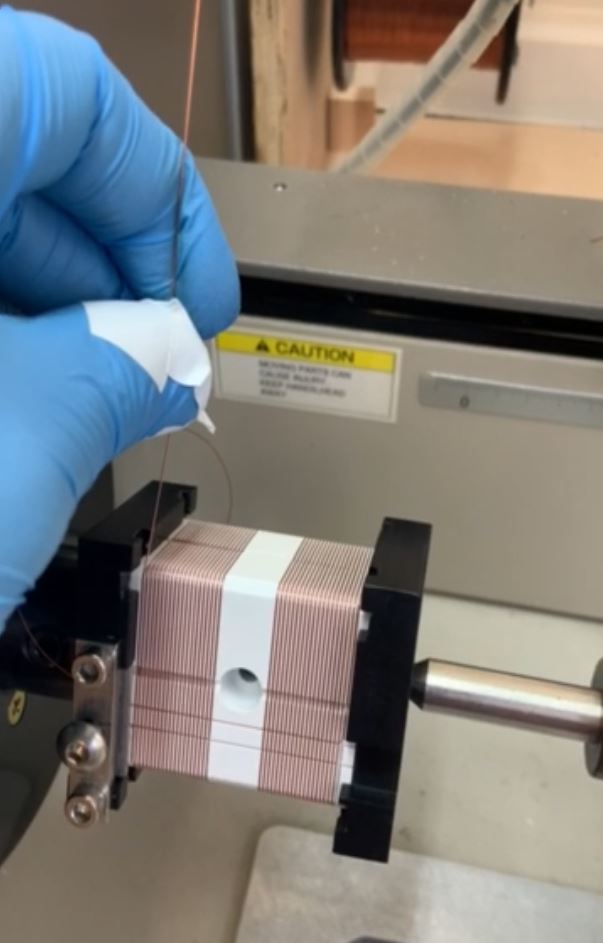
Two different kind of coils have been fabricated for the first batch of Inner Vessel Coils: the United Kingdom Atomic Energy Authority (UKAEA) has been in charge of the High Frequency coils, and VIA electronic manufactured the Low Temperature Cofired Ceramic (LTCC) coils. David Croft, UKAEA Project Manager, offers some details regarding their manufacturing. “The machining of the intricate coil support was both technically challenging and time sensitive with the COVID-19 pandemic spanning the whole period of the contract. The commitment, and harmonised collaboration, between Fusion for Energy, ITER Organization and UKAEA allowed for the contract to be completed ahead of schedule.”
Marc Bochard, VIA electronic R&D Manager, adds his point of view. “Manufacturing the Low Temperature Cofired Ceramic (LTCC) sensors with 40 layers of complex interconnected coils with extremely tight tolerances is a challenging task. We are truly proud to be part of the ITER project, which will be the future of energy production.”
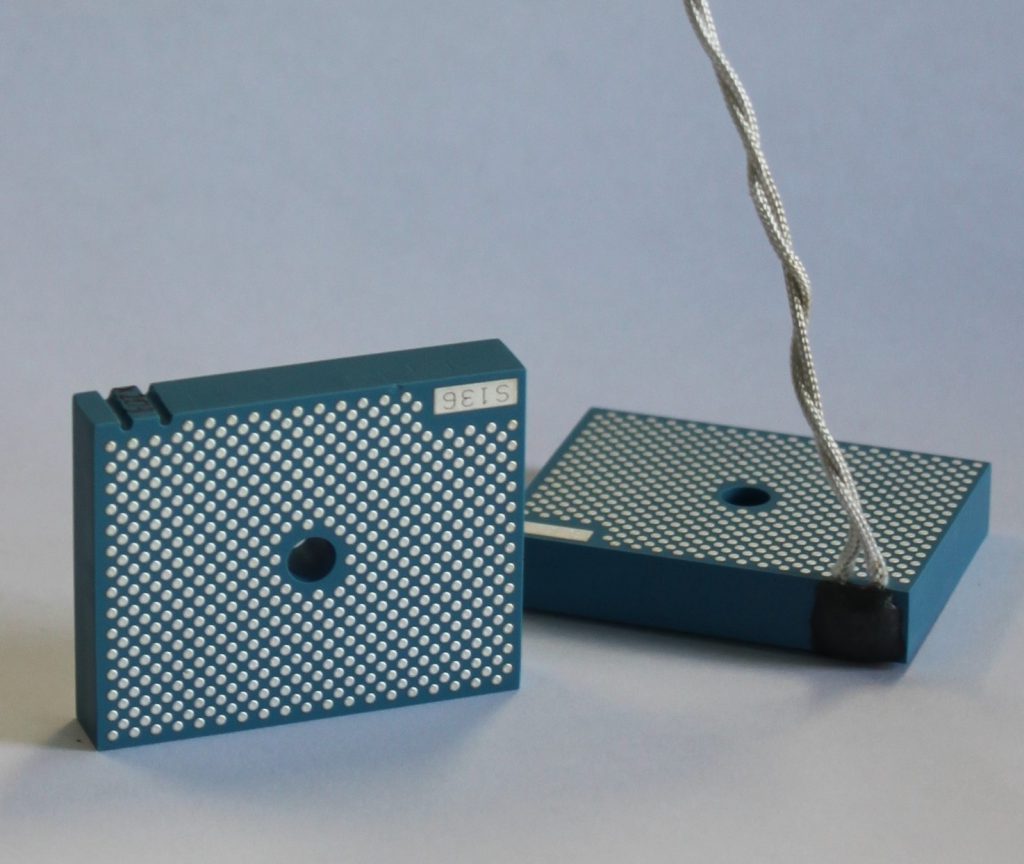
Subsequently, Sgenia Industrial assembled the coils into the housings they had prepared. They also performed testing activities. “The manufacturing and assembly of the mechanical platforms for the Inner Vessel Coils requires advanced techniques, care and precision,” explains Jesús Lama, Sgenia Industrial Director. The last step in the chain was to calibrate the sensors, which was carried out by Elytt. “One of the challenges has been to determine what we call the magnetic angles, as they were altered by the measurement conditions. Adapting the measuring system to the different sizes of the Inner Vessel Coils with the required precision also required special attention,” explains Aitor Echeandia, Elytt CEO.
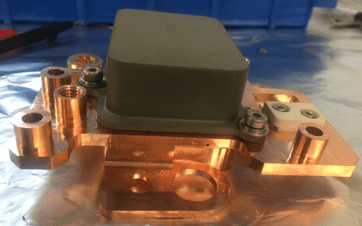
After all the production process, the first batch, made of 144 sensors, has been delivered to ITER Organization and put to storage after concluding the site acceptance test. Two more batches containing the rest of the sensors are expected to be delivered next year. Yunxing Ma, ITER Magnetics Development Officer, elaborates on the co-ordination of all the partners in this project. “The management of this complex supply chain involved close interactions with multiple suppliers to make sure that different activities were well co-ordinated, with rigorous quality control and consistent acceptance standards implemented throughout the entire manufacturing process.”
Paz Casas, F4E Project Manager, emphasises the collaborative mind set underpinning the project. “All main stakeholders had the same approach. We have been working as one team, helping each other in order to deliver a final product of high quality. Mutual understanding and flexibility have been conducive to the production of these components. I would also like to stress the commitment of the F4E team, including the support received by external colleagues.”