Europe concludes winding another ITER Poloidal Field coil
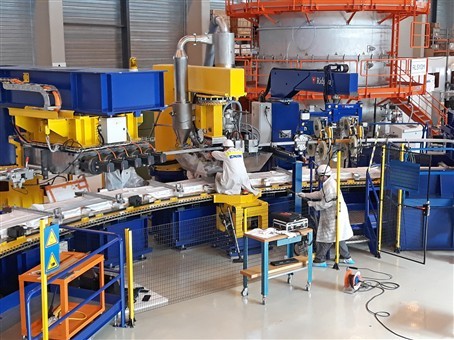
Technicians from CNIM, the F4E contractor involved in the manufacturing of the Poloidal Field coils, performing maintenance works on the tooling used for the winding of the conductor, PF coils factory, February 2019, Cadarache
Europe is responsible for the fabrication of five out of the six Poloidal Field (PF) coils which will be used to control the shape and stability of the hot plasma. Due to their impressive size and weight, ranging between 17 – 25 m in diameter and weighing between 200 – 400 t, the only possible way getting them to the ITER site is manufacturing them there. As a result, F4E agreed to build a factory to produce four of them.

The conductor lengths of the fifth Poloidal Field (PF5) coil have been wound. The efforts made by engineers from F4E, ASG Superconductors and CNIM have paid off. Manufacturing is accelerating and the gigantic magnetic ring is in good shape. Four pair of its windings, known as Double Pancakes, have been impregnated, three of which have already been stacked one on top of the other to form a bigger coil, known as winding pack.

Several European companies have been involved in this operation. Dalkia and Veolia look after the facility and take care of its maintenance. Criotec, Elytt, SEA ALP, ALE, ONET, SEIV, and ALSYOM have provided the tooling. APAVE is responsible for matters of safety. The site acceptance tests for one of the cryostats delivered by Criotec have been successfully completed, and the Factory Acceptance Tests (FAT) for a new cryostat is on-going.
“We are getting closer to the target set for winding operations,” explains Pierluigi Valente, Technical Responsible Officer for the supply of the European share of PF coils. “The re-allocation of resources, and further training consolidating the skills we picked during the learning curve, contributed to this achievement.”

Technicians from CNIM, the F4E contractor involved in the manufacturing of the Poloidal Field coils, preparing to do a layer joggle to the conductor, PF coils factory, February 2019, Cadarache