Europe delivers all of its cryogenic tanks to ITER
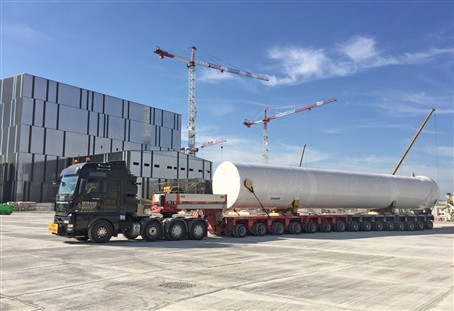

The last out of the 11 tanks that Europe is responsible to provide, as part of its contribution to ITER’s Cryoplant, has arrived. The successful delivery on–site of the gigantic pieces of equipment is considered an important milestone for F4E’s team of experts working in the fields of cryogenics and transport logistics. Europe’s first tank crossed the gates of the ITER facility in November 2016 and almost a year later all other tanks followed departing from different countries (Sweden, Czech Republic, China, and Turkey). The manufacturing of all components was undertaken by Air Liquide, and its subcontractors, while the logistics were handled by DAHER
The biggest fusion device will require a massive “refrigerator” to perform several tasks: first, it will have to cool down its magnets to -179 ° C so that they become superconductive, second, it will help the cryopumps to minimise any thermal losses in the cryostat, and third, it is going to improve the thermal insulation of ITER’s massive vessel in order to create a vacuum.
ITER’s Helium (He) plant is estimated to handle approximately 24 T of He, which corresponds to the gas needed to fill up 14 million helium balloons. The plant will consist of 7 warm Gaseous Helium (GHe) tanks (7 x 360 m3); one Liquid Helium (LHe) storage tank with a capacity of 175 m3 at 4.5K (-268.5 °C), able to store up to 85% of the gas that the plant will need, and two quench tanks.

The LHe tank, widely considered as the “jewel” of the ITER Cryoplant, has finally reached the construction site. This double walled vessel measuring 25.5 x 3.8 m, manufactured by CryoAB (Sweden), has the capacity to handle 20 T of Helium. The whole manufacturing and testing activities required for the acceptance of this tank took one year and a half since the approval of its design. The transportation from Goteborg has been performed in two phases: one by boat up to Fos-Sur-Mer, the industrial port of Marseille, and the final trip to the ITER site by a special convoy.
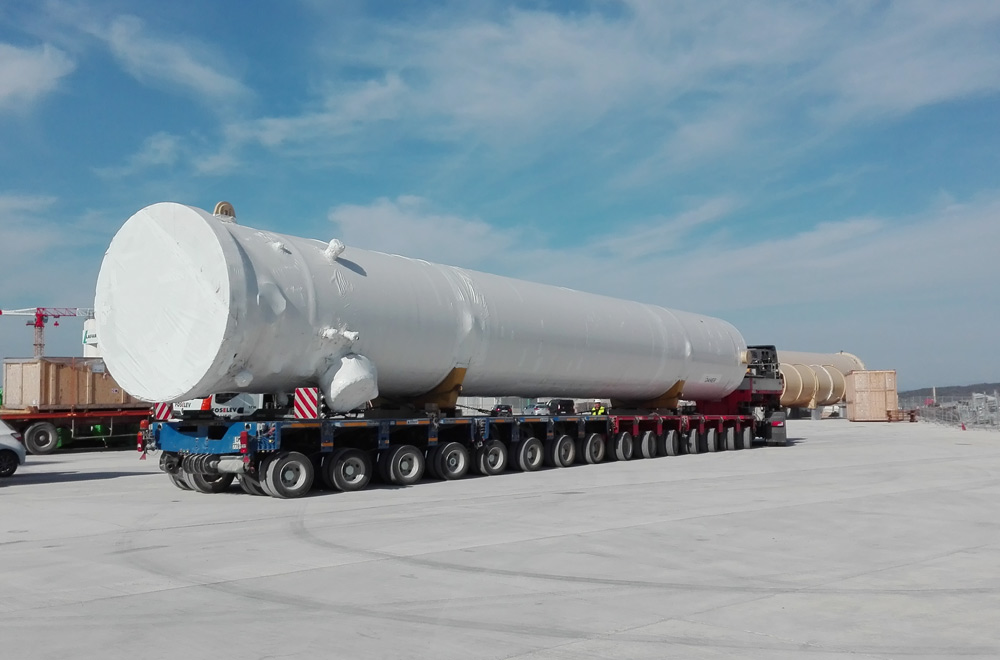
The other arrival on-site has been that of the GN2 buffer tank which also plays an important role in the LN2 plant. This vessel has been manufactured in China by FURUI. The main function of this carbon steel pressure tank is to cope with different pressure levels of the LN2 Plant. It will be connected to the Nitrogen compressors where a panel of control valves will stabilise the pressure levels. Earlier this year, the LN2 tank was delivered on-site
Thanks to the excellent collaboration between all parties, F4E, DAHER and its suppliers, as well as Air Liquide, the components were delivered with less risk avoiding night transport, without highway closures, and intensive police escorts. Ben Slee, following on behalf of F4E the contract signed with DAHER, explains that “good co-ordination can generate substantial financial gains. For instance, the transportation costs have been significantly reduced because of these new measures. In addition, combining the delivery of these components with those of other ITER Parties resulted to more savings.”
Meanwhile on the construction site, a few metres away from the Tokamak complex, the Cryoplant facility is shaping up. It boasts a brand new façade and the last layer of cladding is almost completed. The building is getting ready to house the equipment that has been delivered.