Europe manufactures its first cryopump components for ITER
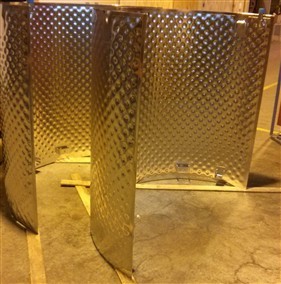

F4E starts the new year with the completion of an important milestone linked to Europe’s contribution to ITER: the successful manufacturing of the cryopanels and thermal shields for the Pre-Production Cryopump (PPC).
The PPC is the spare cryopump of ITER’s eight cryopumps- two are located in the cryostat and six in the torus. The torus cryopumps extract the air out of the machine, capture the speedy hydrogen isotopes and remove the Helium ash. The cryopumps will be constantly operational in the ITER machine and will play a vital role in the production of the Ultra High Vacuum (UHV) inside the torus. In a nutshell, these components will help us attain optimum plasma performance.
After an intense period of research, development and design, F4E was entrusted with the responsibility to manufacture the components. In November 2012, a series of contracts were signed with four companies – based in Germany and in France – as well as with the Karlsruhe Institute of Technology (KIT) for the manufacturing of the PPC. Alain Teissier, Head of F4E’s Cryoplant and Fuel Cycle Team, explained that “the successful completion of this contract at SDMS and Ziemex is the fruit of the excellent collaboration between F4E and the ITER International Organization’s Vacuum Team led by Robert Pearce, in line with the ethos of a unique ITER team”. For Stamos Papastergiou, co-ordinator of the F4E Vacuum Pumping activities, “this cutting edge technological partnership between companies and laboratories, is a clear demonstration of how the ITER project offers opportunities to different innovation actors”. Francina Canadell and Jose Andrade, responsible for the monitoring of the contract and the final acceptance activities, highlighted the importance of this big engineering step.
The PPC and the rest of the torus cryopumps operate with Helium at 4.5 K (-268.5oC, 4.5oC above absolute zero). They consist of the cryopanels, which perform the pumping action, and thermal shields that protect the cryopanels from excessive thermal loads. The components were put through complex dimensional controls and UHV leak tests. The design of these components was based on laser welded heat exchangers formed by water pressure (hydroformed), a technique usually employed in chemical and process industries. This design guarantees minimum temperature gradients in the heat exchanger for the production of the UHV conditions inside the torus.
The cryopanels have already been delivered to KIT and the thermal shields to Research Instruments, a German company, which will integrate the manufacturing activities. At KIT, the cryopanels will be sprayed with charcoal, which is necessary for the pumping of Helium and hydrogen isotopes from the torus. Research Instruments, together with Alsyom/Seiv will play a pivotal role in the production of the rest of the cryopump components, their assembly as well as the final cold UHV leak tests of the PPC.
Watch Dr. Michael Peiniger, Managing Director of Research Instruments, expressing his opinion on the benefits of his company’s participation to ITER by clicking here.
