European Toroidal Field coils manufactured at full speed
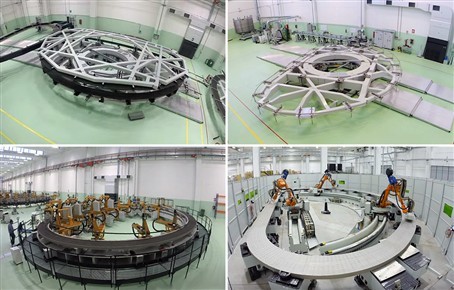

Europe is responsible for the manufacturing of 10 out of the 18 Toroidal Field (TF) coils of the ITER machine. The TF coils are “D” shaped gigantic superconducting magnets whose main task will be to create a massive magnetic cage where the plasma will be confined. To help you understand the progress made by F4E and its suppliers, we visited the ASG facility, where the works for the winding packs are being carried out, to film some of the main manufacturing steps. The clips document the life of a conductor from the moment it arrives to the facility till it nestles inside the grooves of a laser welded radial plate.
First, we started filming the winding of the conductor to show you how the winding tooling is bending with accuracy of fractions of millimetres the 750 m long cable-in-conduit conductor to form a double spiral trajectory known as a Double Pancake (DP). Next, we visited the insertion tooling station to capture how the heat treated conductor is being inserted inside the 750 m long groove of the radial plate. Then, we moved our cameras to the wrapping tooling to show you how the electrical insulation of the conductor is applied to the conductor. Finally, we filmed the way three robots work simultaneously to laser weld the cover plates of the radial plates containing the conductor.
In September F4E reported that 32 radial plates- enough for four TF coils- have been successfully manufactured by CNIM and SIMC and delivered to the ASG facility. A full size superconducting DP prototype has been successfully fabricated and subjected to a thermal cycle to 80K. So far 36 Double Pancakes (DPs) have been wound (enough to make 5 TF coils), 30 DPs have been heat treated and 28 DPs have been successfully transferred into the radial plate grooves. The cover plate welding has been successfully completed on 19 DPs.