Europe’s final ITER Toroidal Field coil heading to ITER

Transporting Europe’s last ITER Toroidal Field coil, from the SIMIC factory to the Port of Maghera, Italy, November 2023 ©DAHER
As the heavy doors of the SIMIC factory in Marghera are slowly opening, the track carrying Europe’s last Toroidal Field (TF) coil is ready to make its way to the port. It’s the final journey, full of symbolism, for F4E’s multi-million contract providing these complex superconducting magnets. It’s wrapped with protective covers featuring the logos of those who contributed. Every one of them tells their story and that of their staff who have been part of this incredibly adventure. Once the coil was carefully loaded on the vessel, sailing to the south of France, a spontaneous round of applause echoed in the port. It’s a farewell filled with pride and the sense of accomplishment. Europe did it!
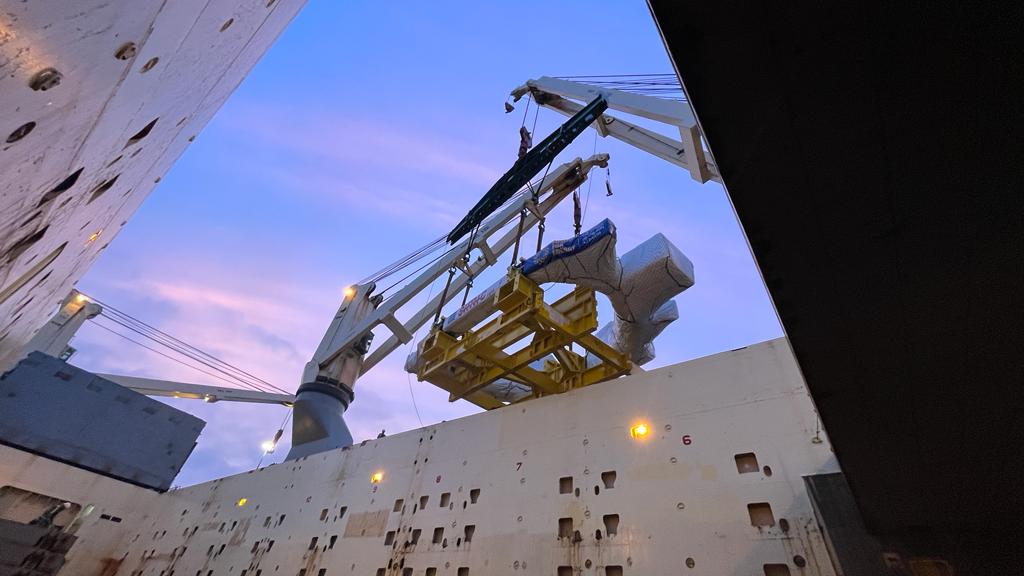
ITER will use 18 of these magnets to confine the super-hot plasma which will reach 150 million ° C. Europe has manufactured ten of them while Japan eight plus one spare. How will these magnets work? They will create a magnetic cage to keep the hot plasma away from the vessel of the machine. When powered with current (68 000 A) the magnetic field will reach up to 11.8 Tesla—about 250 000 times the magnetic field of the Earth!
How big are theses magnets? Each of them measures 17 x 9 m and weighs 320 tonnes— as much as an Airbus A350. Europe held two records: it was the first party to be deliver a TF coil to ITER, and it was the first EU component of such size to be handed over to the project. The EU has financed the works of this high-tech component, through Fusion for Energy (F4E) which has been collaborating with at least 40 companies, and more than 700 people, to produce the ten coils.
The main contractors are SIMIC, ASG Superconductors, CNIM, Iberdrola Ingeniería y Construcción, Elytt Energy and the ICAS consortium. The manufacturing of the ten European magnets took place in several factories: Turin (Italy), where ICAS produced the conductor; La Spezia (Italy), where ASG Superconductors, in collaboration with Elytt Energy, and Iberdrola Ingeniería y Construcción, manufacture the inner-core of the magnets; Toulon (France), where CNIM produced the equipment to insert the conductor into the magnet; Marghera (Italy), where SIMIC produced similar equipment to insert the conductor into the magnet and in addition has been carrying out cold tests, and been inserting the magnet into its case. When the coil arrives by boat at the port of Fos-sur-Mer (Marseille) and then it will be transported to the ITER site, Cadarache.
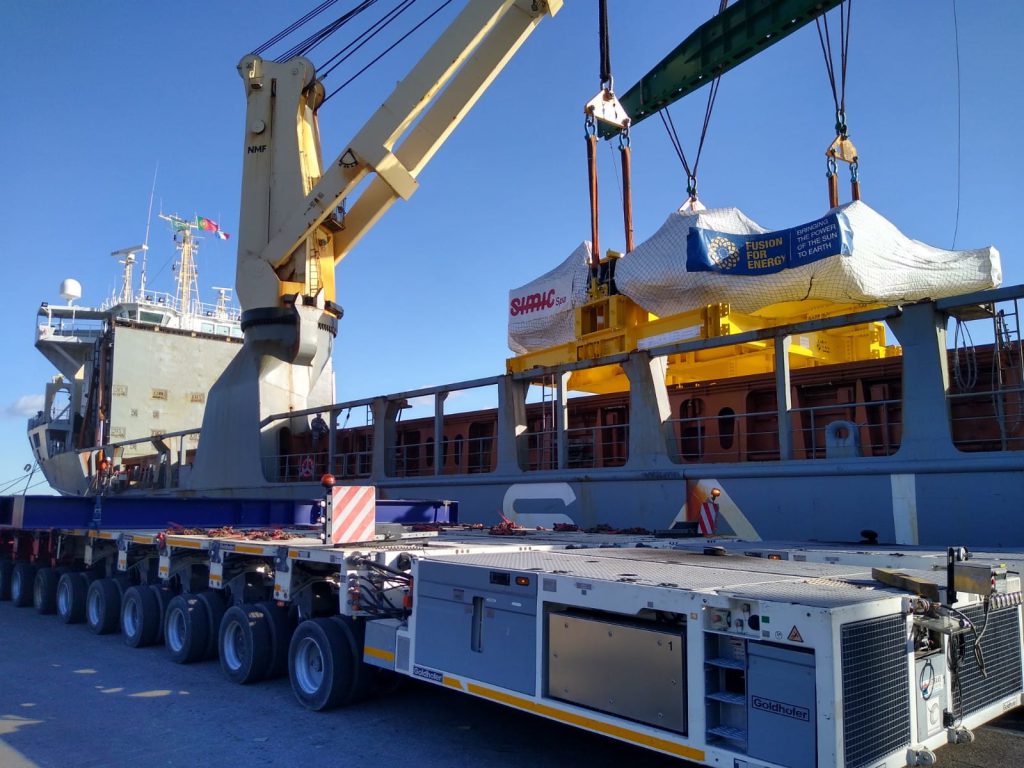
Alessandro Bonito-Oliva, until recently F4E Programme Manager for Magnets, leading the European TF coils project since 2008, elaborated on the importance of this significant milestone for Europe. “This achievement results from 15 years of work involving more than 700 people and at least 40 companies. Many factors have shaped this outcome: vision in developing the best procurement strategy and interfaces between suppliers; expertise in defining the right technical solutions; cooperation between all parties to tackle issues in manufacturing the most complex magnet to date; and last but not least, passion, perseverance and the full commitment of a highly qualified team. All these factors helped us to complete this manufacturing project successfully.”
Boris Bellesia, until recently F4E Magnets Deputy Programme Manager, responsible for the large industrial contract with SIMIC, underlined the fruitful collaboration between F4E and SIMIC: “We accomplished some major achievements throughout the fabrication process: The delivery of the first coil to ITER, the optimisation of time in production, and the extremely high level of technical homogeneity between all TF coils. Today, we have sent off our final coil and it feels like the end oof an amazing adventure.”
Looking back as to how we reached this important milestone for Europe, more people come to mind who have contributed with their technical skills and expertise. Robert Harrison, who followed in the factory of ASG Superconductors the production of the ten winding packs (the core component of the magnets), Eva Boter who followed the production of the 54 radial plates produced by CNIM and SIMIC. Last but not least, all colleagues who offered support from the Project Management, Commercial, and Administration Departments towards the successful execution of these contracts.
To see the manufacturing steps of the Toroidal Field coils download the F4E poster.
To view the F4E video on how the TF coils were manufactured click here.
To view how ASG Superconductors has produced the core (Winding Packs) of the magnets click here.
To view how SIMIC has produced its radial plates click here.
To view how CMIM Group has produced its radial plates click here.