Europe’s first ITER Vacuum Vessel sector ready!
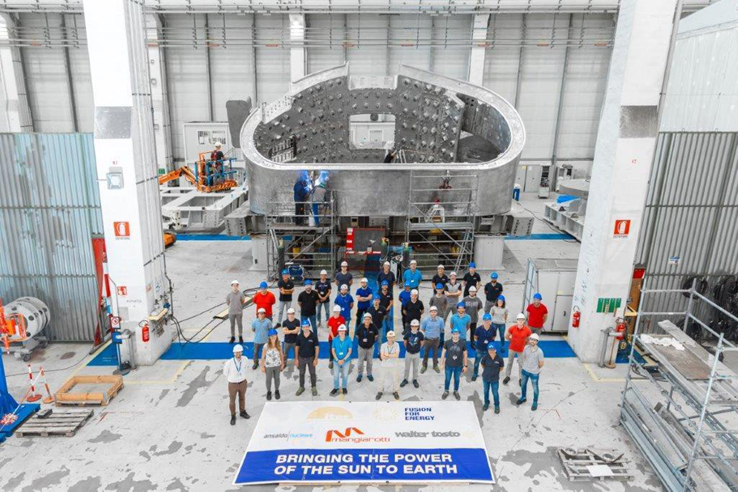
Completion of Europe’s ITER Vacuum Vessel sector 5, provided by F4E in collaboration with Ansaldo, Westinghouse, Walter Tosto (AMW) consortium, Monfalcone, August 2024. ©F4E
ITER’s fusion reaction will be housed in a massive double-walled vessel that will be hermetically sealed keeping away any dust, air, liquids and impurities. Inside this massive shell made of stainless steel, the blazing hot plasma will be ignited. Thanks to a set of powerful superconducting magnets that will embrace the vessel from top to bottom and all around, the plasma will float without touching its walls. Nine sectors in total will be welded together to form this component with Europe producing five of them, and Korea the remaining four. The completion of Europe’s first ITER Vacuum Vessel sector provided the perfect opportunity to celebrate this achievement in the presence of F4E with representatives from Ansaldo Nucleare, Westinghouse, Walter Tosto, ITER Organization and various stakeholders.
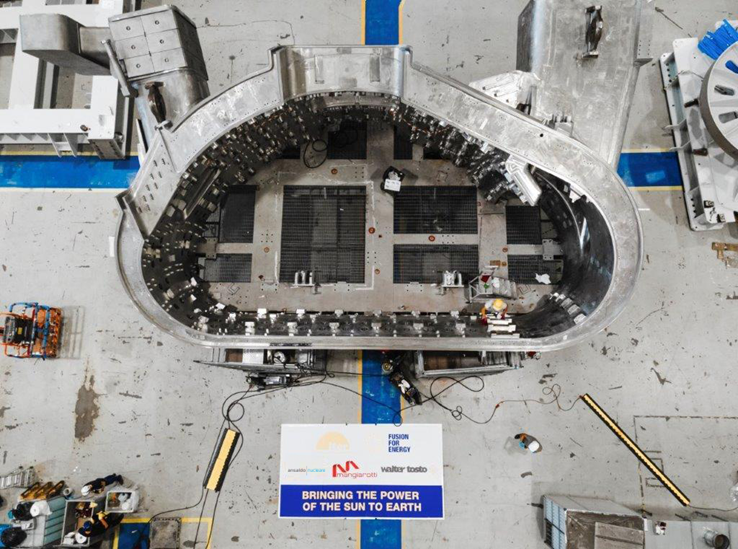
First, let’s get familiar with some basics. The vacuum vessel will measure 19.4 m in diameter by 11.4 m high and weigh approximately 5200 tonnes. The component complies with high standards set by the French Nuclear Safety Authority to operate safely. The geometry and dimensions of the component can be described as challenging. The stringent manufacturing specifications have also raised the benchmark for all industrial partners. With each sector counting roughly 150 km of welding beads, the risk of deformations and non-conformities is high. Europe has mobilised several teams of technicians, metrology experts, engineers and quality assurance officers to perform continuously detailed checks along the way. Today’s first sector results from the strong collaboration between different parties all over Europe and the drive to succeed no matter the technical challenges.
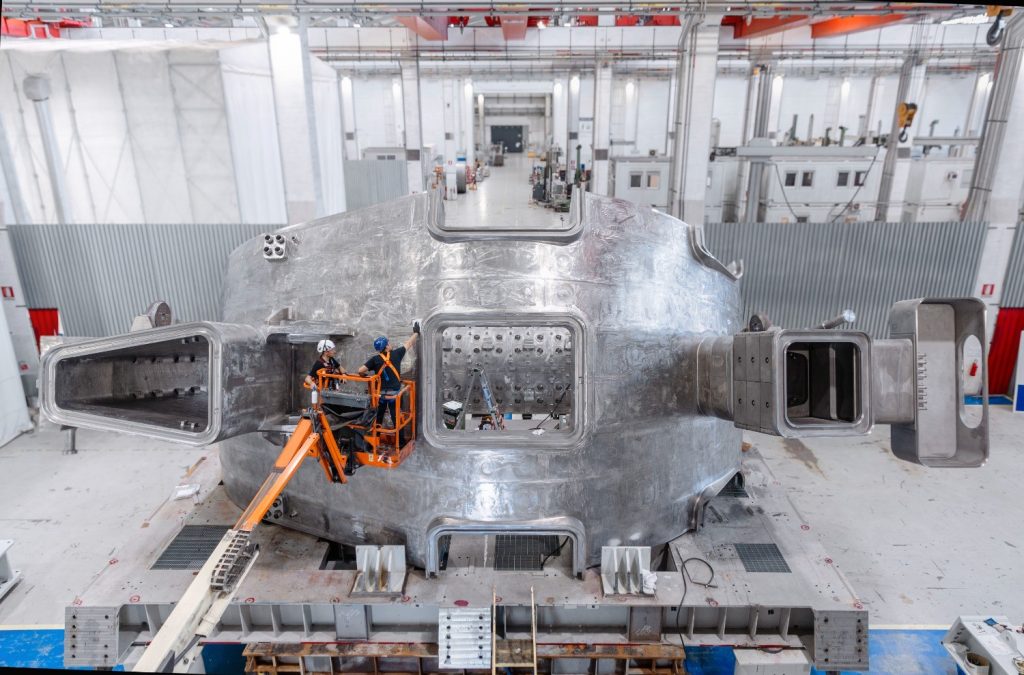
F4E has been collaborating for more than ten years with the AMW consortium of Ansaldo Nucleare, Westinghouse and Walter Tosto, involving directly 150 professionals, and more than 15 companies across Europe with their respective teams.
If we had to simplify the fabrication process in few steps, we would break them down to the following: i) cutting and machining of raw forgings, ii) fabrication of segments, iii) welding and assembly of segments, iv) assembly of sector and v) final machining. In between there are hundreds of sub-tasks and many exchanges and interfaces between the companies. To grasp the web of contractors involved in the production, machining, and manufacturing of sector 5 we have identified few where key operations were performed. For instance: Industeel supplied the material for the plates base. The forgings were produced in Rolf Kind, Forgiatura A.Vienna, Valbruna Ibérica, Aubert & Dubal, Thyssenkrupp. The filler material for the welds was produced by BÖHLER.
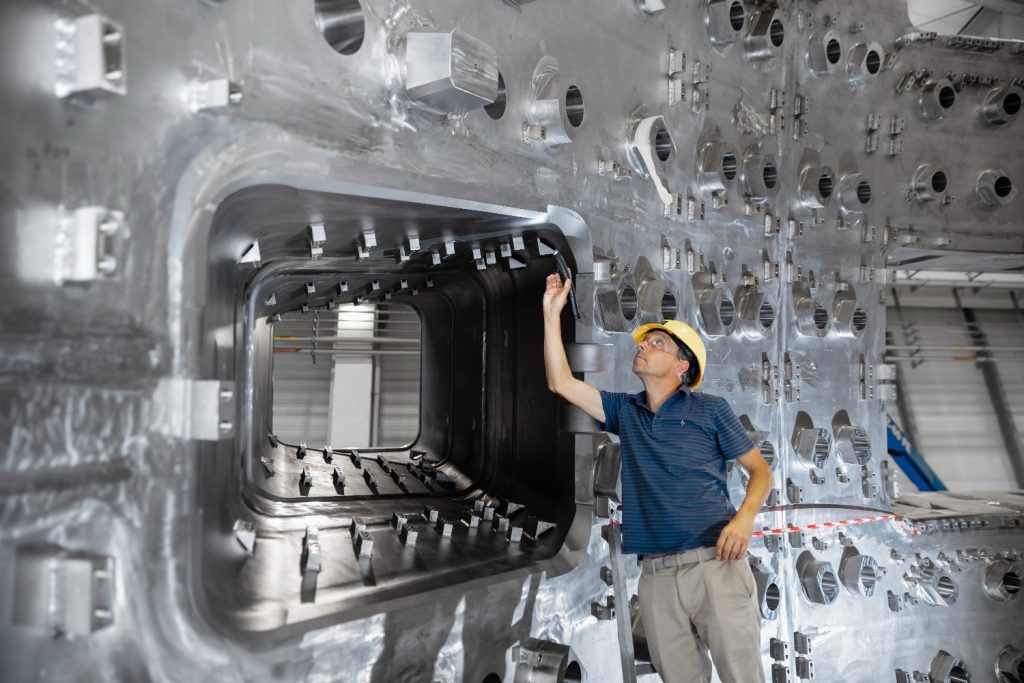
Sector 5 is the first of the five that F4E will deliver to ITER Organization. In Westinghouse, Monfalcone, two of its segments (1 and 4) were manufactured while the other two (2, 3) were produced in Walter Tosto, Chieti, roughly 150 km away from Rome. The segments were assembled, and then welded to become one, following a specific sequence (1-3-2-4). For the work behind each segment, we estimated roughly four weeks to complete the welding of forgings and plates using electro-beam welding, and at least 90 days to complete their inspection.
Andrés Dans Alvarez De Sotomayor, F4E Technical Officer based in Westinghouse for more than eight years, looks back at some of the key moments that defined the progress of sector 5. “It is the achievement of so many years of work trying to respond to several technical challenges for this one-of-a-kind component. I remember witnessing the manufacturing of raw material, starting from the casting of the ingots, that become the small forgings and plates, which slowly transformed into this massive steel structure. How the works advanced in parallel in different factories and eventually all pieces were united under the same roof. Most importantly, I recall the teams of people from F4E, AMW and ITER Organization who have been instrumental to today’s success. Thanks to our collective team effort, and our perseverance to never ever give up, we made it. The human story behind this component is what makes it so special.”
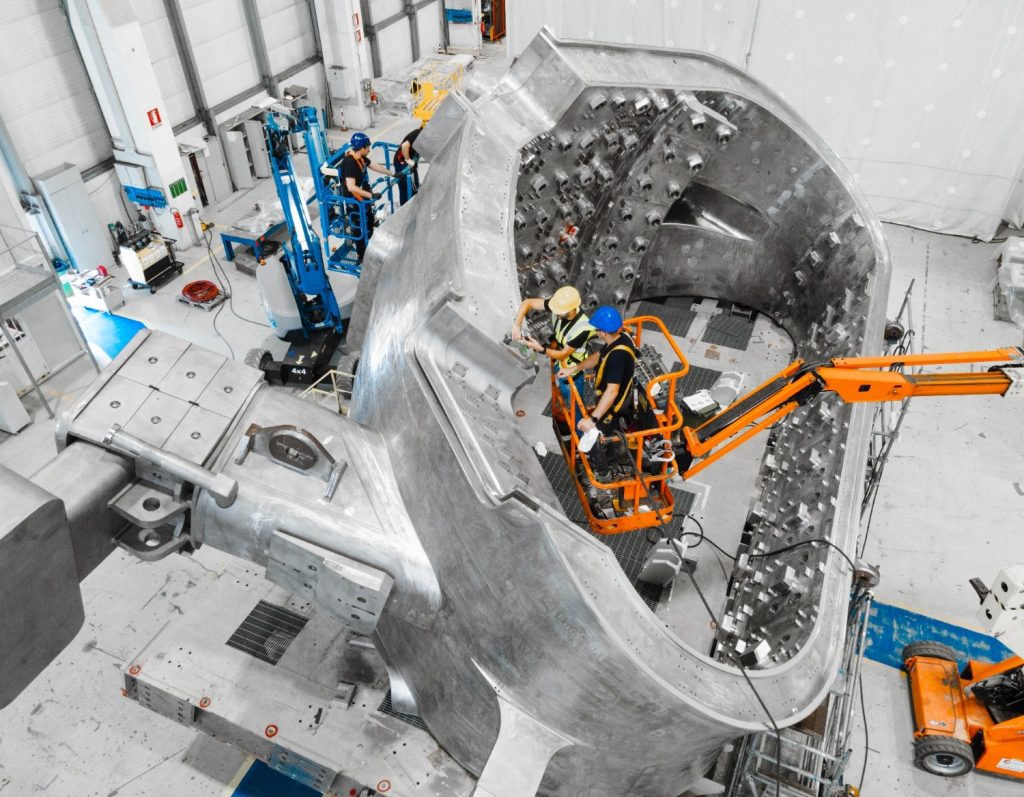
According to Marcello Parodi, Project Director of the AMW Consortium: “…the successful completion of Sector 5 of the Vacuum Vessel, undertaken by the AMW consortium (Ansaldo Nucleare, Westinghouse, and Walter Tosto), highlights the excellent collaboration between the consortium, our customer F4E, and ITER Organization, resulting in complete satisfaction.”
For Joan Caixas, F4E Project Manager for the Vacuum Vessel, “…the production of sector 5 has been a fascinating learning curve for Europe and its industrial suppliers. We managed to overcome the technical challenges in production, and those of schedule, successfully. We followed the manufacturing process with rigour and made progress with great care and confidence. This results from the meaningful collaboration between F4E, the AMW consortium, their sub-suppliers and ITER Organization, who took part to so many meetings, contributed to the revision of strategies, and travelled to so many of our factories. Personally, I feel very proud to be part of a team of colleagues that delivered Europe’s first vacuum vessel sector.”
The component was completed towards the end of August and is expected to depart from Italy in September. It will be delivered to Fos-sur- Mer, the industrial port of Marseille, where it will be loaded onto a massive trailer to transport it to the ITER site. Europe’s remaining four sectors are in production and will be delivered in the next two years.
To view more images of Europe’s ITER Vacuum Vessel sector 5 click here.