Europe’s ITER Vacuum Vessel sectors in the making
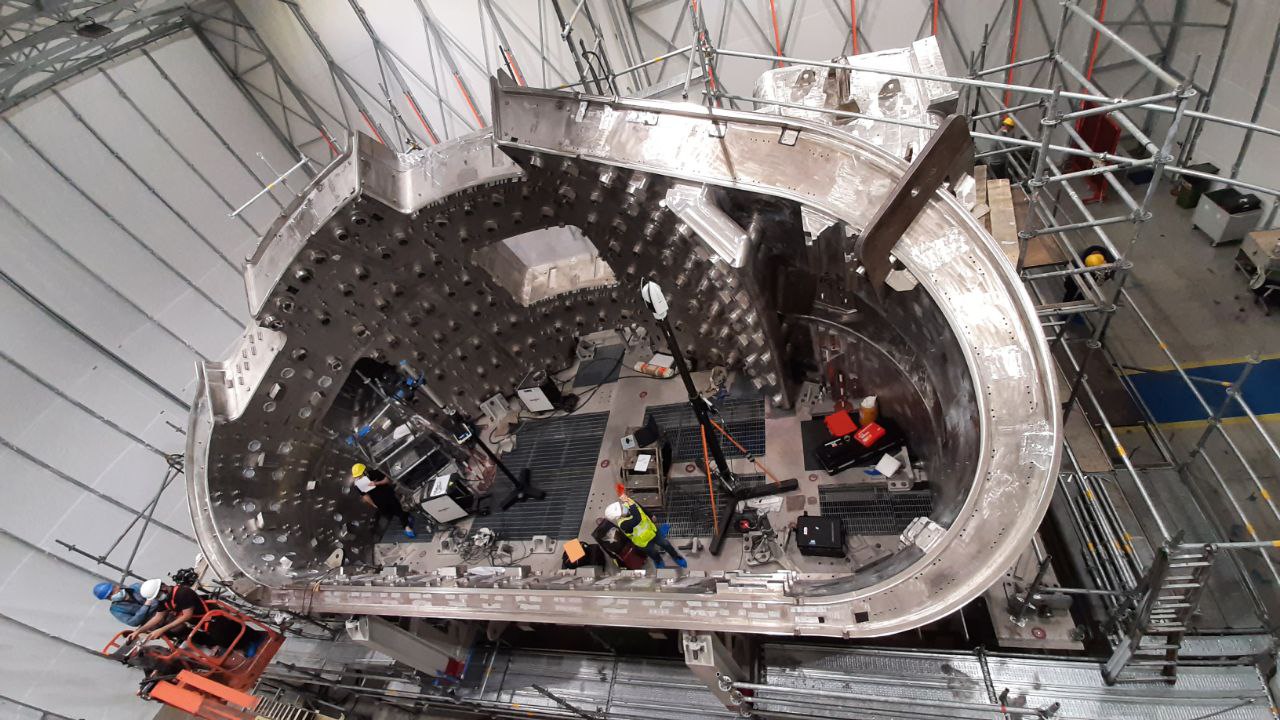
Top-down view of Europe’s ITER Vacuum Vessel sector 5 on the assembly tool, Mangiarotti, Italy, March 2022. © F4E
Is it possible to house the fusion reaction inside a box? Are there materials to sustain temperatures as high as 150 million °C? Can such vessel be produced in different countries and then be assembled as one? The answer to all these questions is yes but the human effort is immense. The ITER Vacuum Vessel is one of the components that has fascinated engineers and industry for several reasons. First, its impressive size and weight reaching 5 200 t, qualify it as one of the big and critical components of the ITER device. Second, the complexity and the tolerances required are far too many. This double-walled container made of stainless steel will be embraced by massive superconducting magnets, creating a powerful “cage” around the hot gas, obstructing it from touching its walls. The vacuum vessel is made of nine sectors. Five are produced in Europe and four in Korea following a manufacturing design prepared by ITER Organization. When delivered to the ITER site, the sectors will go through more checks, inspections, assembly and finally, welding to become one.
F4E, managing the European contribution to ITER, has entrusted its share of vacuum vessel sectors to Ansaldo Nucleare, Mangiarotti, Walter Tosto (AMW), and their subcontractors ENSA, Belleli. The work is unfolding in many countries making this a truly European partnership between companies in Italy, Spain, and Germany. Two of the sectors are quickly advancing in parallel. We visited three of the factories, and interviewed some of the main engineers, to learn more about the latest progress.
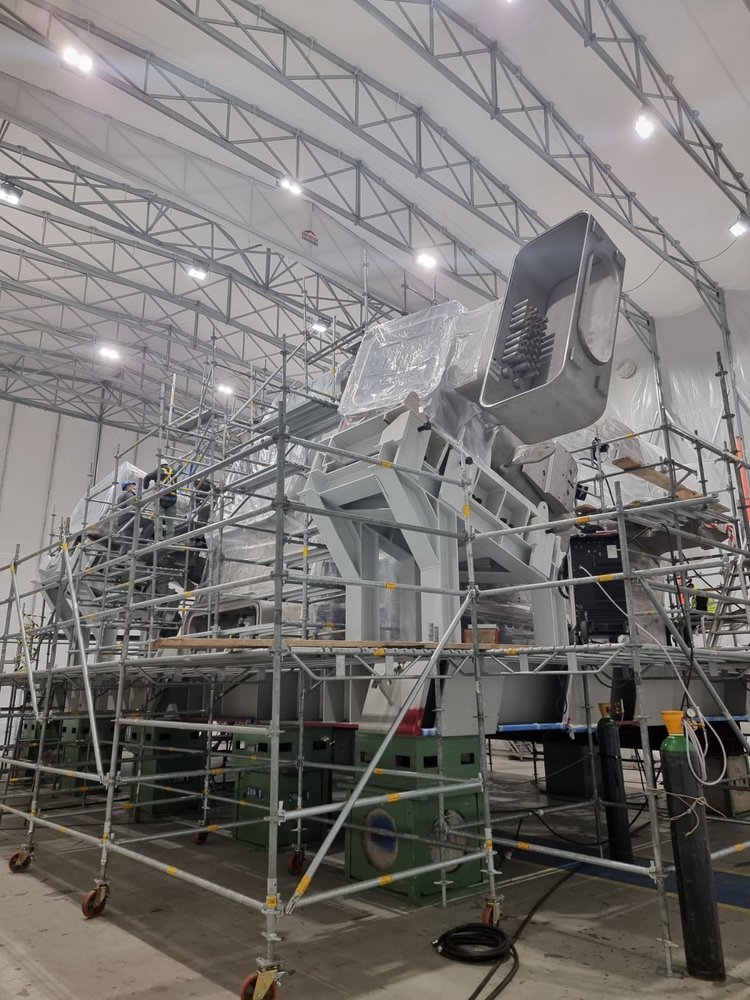
F4E’s first vacuum vessel sector will leave this year from Mangiarotti, Italy. It’s ITER’s sector five. A total of 100 people from approximately 15 companies have been involved during its manufacturing lifecycle. Its four segments weighing in total 500 t are on the assembly frame. Next, the in-welding shielding blocks, the joint ribs and the outer shells will be installed. These pieces will be fixed internally and externally to make the component even more robust. Subsequently, the team of engineers will proceed with further inspections and final factory acceptance tests.
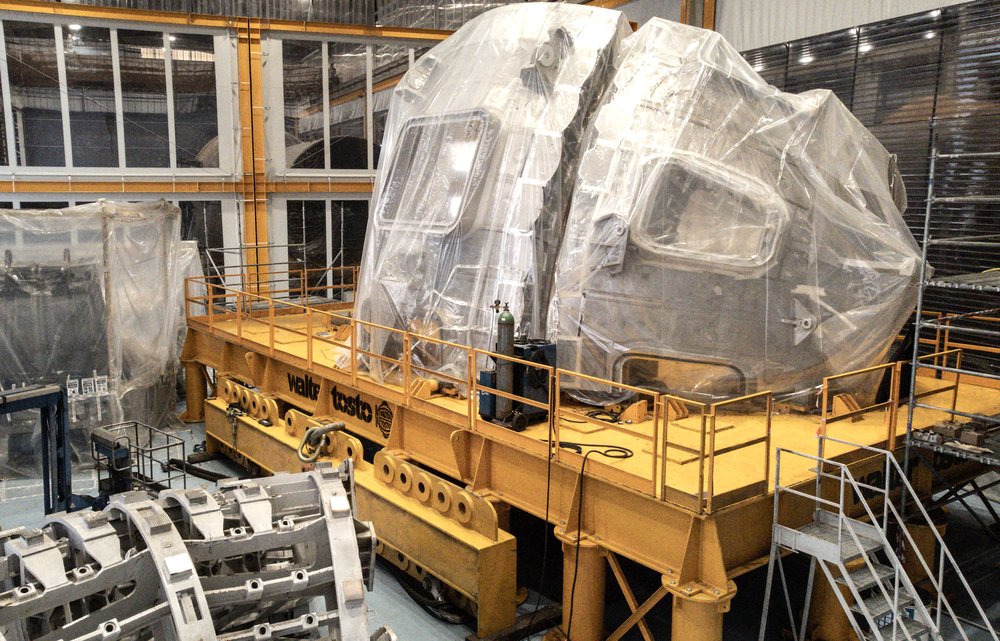
A few things come to mind when Andrés Dans Alvarez De Sotomayor, F4E Technical Officer based in Mangiarotti, looks back. “Performing tests on such a voluminous component is a real challenge but I would single out the ultrasound tests. It’s not only the geometry of the component, which is particular. It’s also the number of welds, in hidden and visible parts, that require thorough inspection. When the four pieces, produced in two different factories, were finally united on the same assembly tooling, we saw for first time the entire component coming together. All the efforts unfolding in so many factories under one roof. Until then, we only focused on the segments of the sector. Now, we are working on delivering it as one to ITER.”
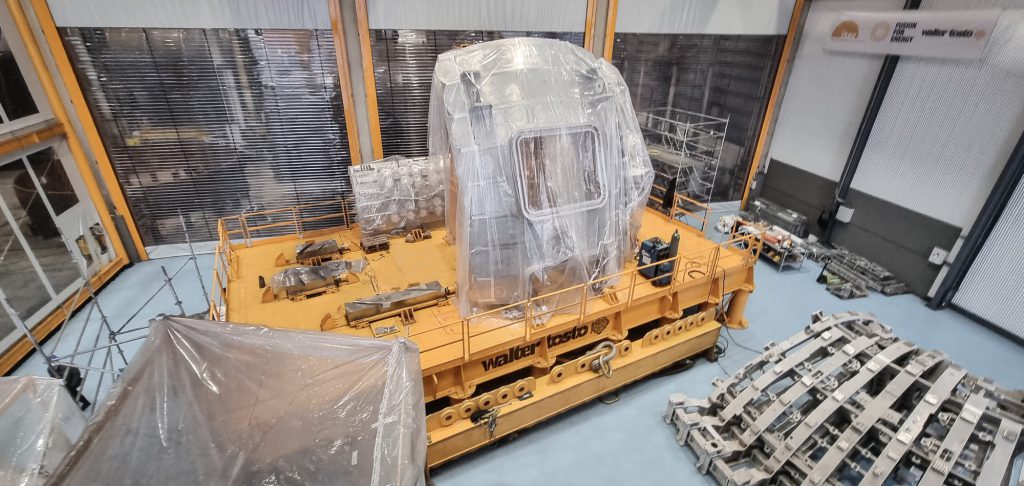
Max Febvre, F4E Manufacturing Project Manager for the vacuum vessel, is based in Walter Tosto, it’s where the action is happening for sector 4, Europe’s second in line to be delivered. All four of its pieces, two from Mangiarotti and two from Walter Tosto, have arrived in the brand-new workshop in Ortona. Three of them are already on the assembly tooling. When all segments are positioned on the jig, the dimensional checks will be performed, and the inner and outer shells will be installed. There is some way to go for the completion of this sector, whose fabrication started nearly five years ago, but the finish line is visible. For Max two operations stood out in terms of complexity: dimensional checks and compliance with nuclear codes. “The sheer number of welds, approximately 730 m/sector, make checks extremely complicated. They are many and all over the component. But what is most demanding is identifying any distortions resulting from welding and fixing them. And then there is the whole issue of compliance with nuclear codes. Remember the ITER Vacuum Vessel will house the fusion reaction and it need to meet extremely high standards set by France’s nuclear authority,” he explains.
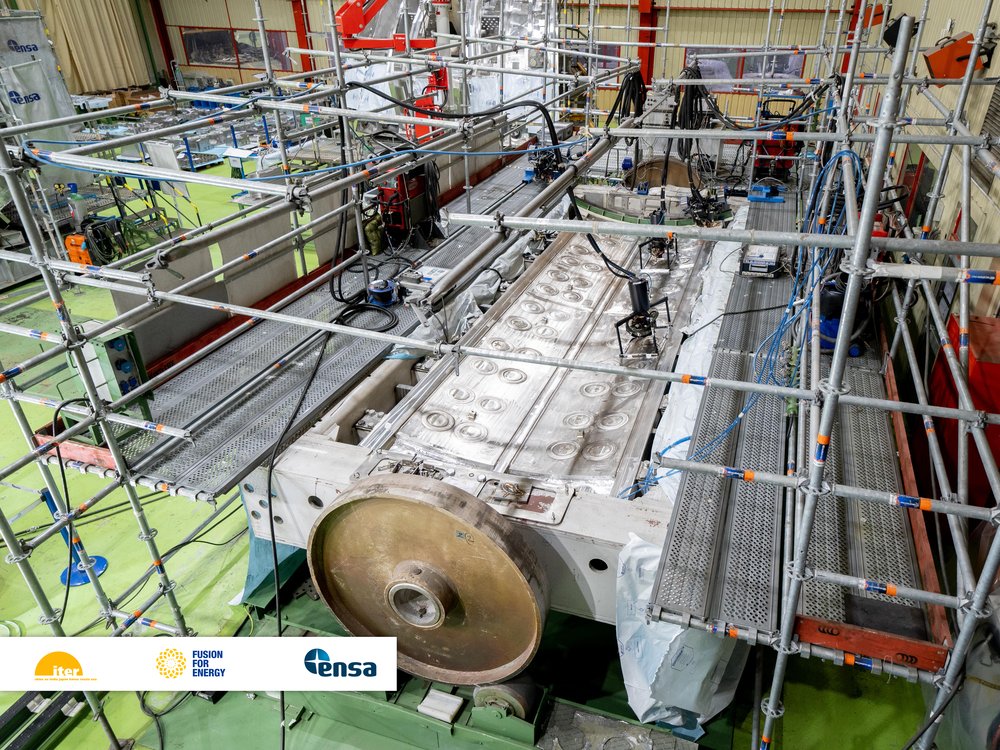
The AMW subcontractors spread in several European countries. This time, however, we stopped in the workshop of ENSA, Spain, where segments for sectors 2,3 and 9 are advancing. In fact, a total of three segments from different sectors should soon be completed. Building on the know-how from the other two sectors, the team of engineers is making further advances. And there is another twist in the story: automatic welding performed by robots. Contrary to manual welding, mainly used for the fabrication of the other sectors, ENSA has opted extensively for this technique, which is fast and reliable. It may be less flexible that manual operations but comes with time savings and less distortions. Around 50 people are rotating in the workshop following the progress of the segments.
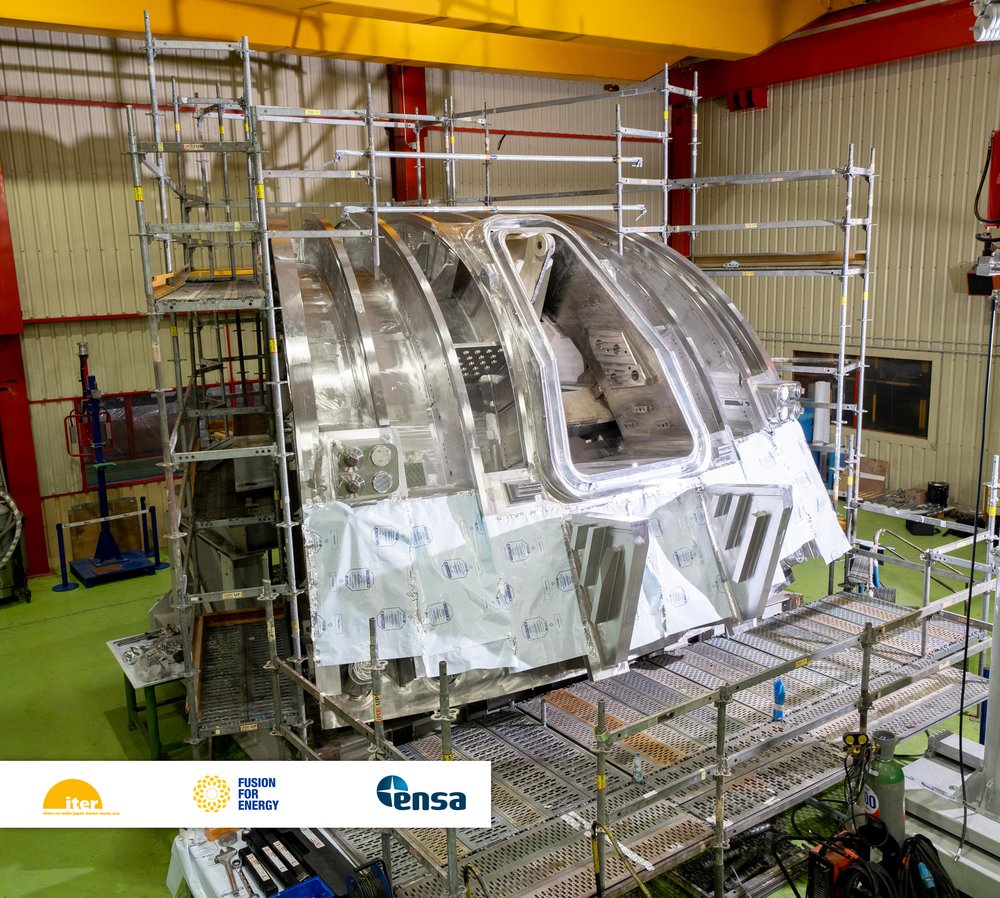
For Joan Caixas, F4E Assembly Project Manager, the completion of the first segment in ENSA last year, and the progress of all others, is a step in the right direction. “When we started our collaboration with ENSA, we capitalised on previous know-how, which we complemented with own experience. The last two years, starting with the purchase of materials to the production of the components, we have created a more solid partnership based on good team spirit.” Alejandro Sampedro, who has also been following the works in ENSA, sounds confident about the progress. “I have been involved in the fabrication of the vacuum vessel since 2015 and I can honestly say that there is a new impulse since last autumn which helped us improve. A big part of the work in the vacuum vessel consists of welding and ENSA’s expertise in this field was crucial. The results so far are satisfactory, and we will tackle any technical challenges along the way. The delivery of the first segment was a tremendous boost for all of us showing that we can deliver as one team.”
Managing the technical and commercial aspects of the European vacuum vessel sectors is a challenging balancing act for F4E’s Programme Manager, Cristian Casanova. As the pace of production is accelerating in the different factories, he spends most of his time there between senior management meetings and progress reviews. He identifies a few factors that make this operation particularly demanding. “Time is of the essence for Europe’s first sector putting immense pressure on the teams. In parallel, our industrial partners are working hard to deliver such state-of-the-art component which needs to meet very high manufacturing standards. We are dealing with a complex piece of equipment which needs to tick all boxes, and to be fully compliant for ITER assembly avoiding any revisions afterwards. Therefore, thorough follow up, communication and collaboration between all parties is of fundamental importance. We have been working hard for the delivery of the first EU sector which in many ways has been our learning curve for the ones to follow. Personally, I’m grateful to our staff and collaborators for keeping up the good work and for staying focused until the end during very difficult times.”