Europe’s second Toroidal Field coil delivered to ITER
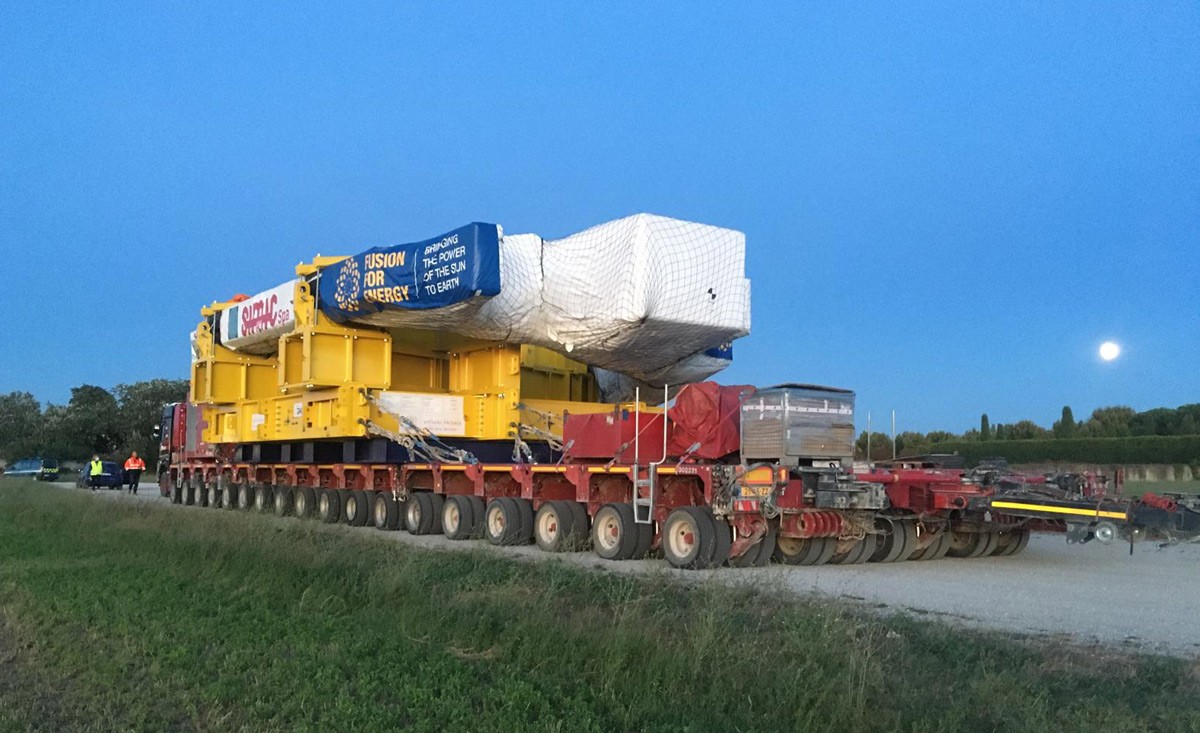
Europe’s second Toroidal Field coil loaded on the trailer. DAHER, managing the logistics, followed the route of the ITER Heavy Exceptional Convoys to deliver the component to the ITER site, September 2020
“The will to do, the soul to dare” they say. But when you have to face a pandemic which puts countries in lockdown and paralyses the brave, where do you find the will? Most likely in your soul. F4E and its suppliers stood united, showed courage and put forward a well-thought through project plan. “The ITER Toroidal Field coils are by far the most technically-complex superconducting magnets to date. Those involved in their manufacturing have demonstrated that they can cope with tough challenges. It’s no wonder this team managed to complete the magnet and deliver it in the middle of a pandemic which shook every plan to its core” explains Alessandro Bonito-Oliva, F4E’s Magnets Programme Manager.
Europe has to provide ten of the 18 Toroidal Field coils which will be used to confine the ITER plasma by generating a powerful magnetic cage. The massive components will measure approximately 14 m and weigh 320 t with their cases. One needs to understand the scale and the complexity of their production under normal circumstances to imagine how things could get complicated during the pandemic. Europe’s first magnet left from SIMIC, close to the port of Marghera, Venice, a few days after Italy started coming into terms with the new COVID-19 reality. The fabrication and delivery of the second magnet, however, unfolded in the midst of the pandemic. How they did F4E and the companies involved kept the production going and managed risk?
SIMIC introduced an array of measures complying with the decree issued by the Italian authorities. With fewer people on-site and with additional health and safety checks, the work advanced in the best possible manner in order to contain risks and delays. “The COVID-19 pandemic has been affecting significantly our working and private life. SIMIC has been considering the matter seriously since the very beginning and has established a dedicated internal committee composed by our Health, Safety & Environmental Manager, the company doctor, and representatives of the management, to analyse the issue and establish the company rules to be followed in line with the Italian and international guidelines for the pandemic. Thanks to the application of strict measures like smart working, fever checks, travelling limitations, distancing, hygiene and the use of masks, we were able to limit stop-of-activities to the strict necessary during the lockdown. Today, SIMIC counts zero COVID-19 cases and we are proud of this. However, the emergency is not over and we have to maintain our attention at the highest levels,” explains Marianna Ginola, SIMIC Commercial Manager.
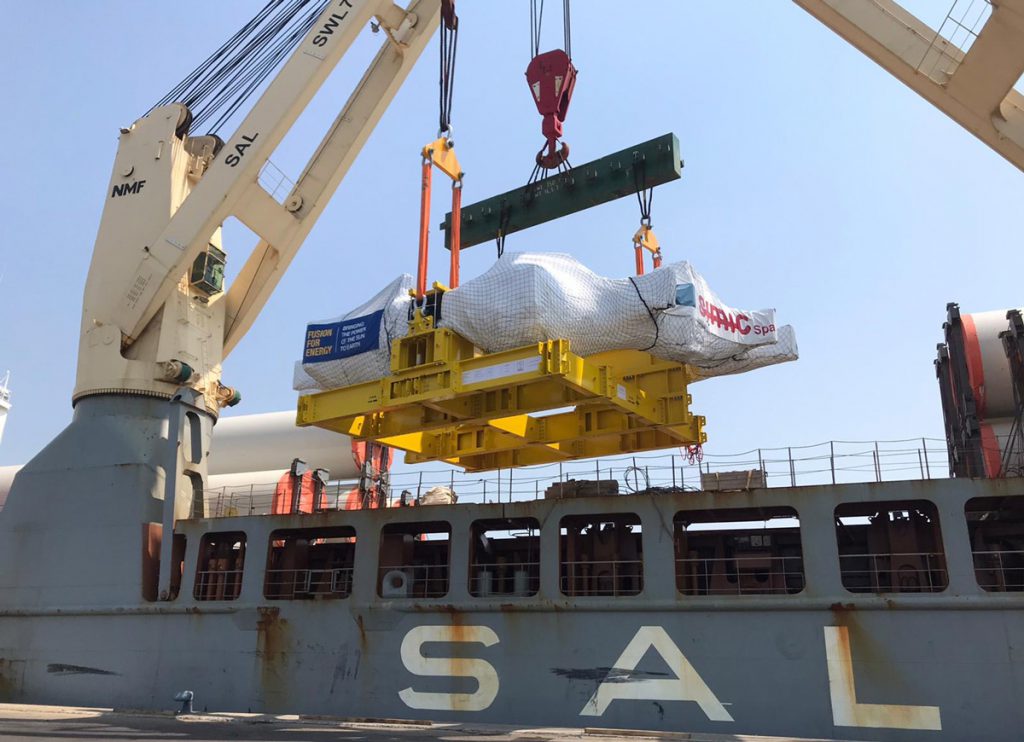
With travel restrictions in place making visits on-site from abroad impossible, Boris Bellesia, F4E Magnets Project Manager, increased the periodicity of meetings and improved the communication flow between all parties. “In order to remain focused on the tight schedule, we came up with a list of topics which we were recurrent and discussed their progress. Daily team meetings were scheduled to address specific aspects of manufacturing, quality assurance and project control aspects. We also developed an online kanban-technique platform to allow contributors to encode progress, actions, and solutions. The dashboard was shared with colleagues increasing our awareness, commitment and collaboration,” he explains.
Receiving different inputs and ensuring that everyone is on the same page is one of the main tasks of Eduard Viladiu-Martinez, who has been acting on behalf of F4E as the Interface focal point for the different companies. “Although the ten magnets go through the same manufacturing steps, they are all unique in their way. Each one of them has its own set of challenges,” he says. Ensuring the timely delivery of the second magnet was no easy task. More human resources were required to cope with the situation and various contingency plans were developed. “The uncertainty caused by the virus, the different measures applying from one country to another, and the fear of local lockdowns complicated things. For example, the planning of the days in transit from Italy to France, the transport between the two ports of Marseille, and the loading on the exceptional convoy could change. For this reason, extra measures had to be taken to monitor the levels of humidity which could have had an impact on some of the materials in the core of the magnet. In particular, two additional humidity sensors were used to continuously monitor this parameter via Bluetooth offering updates and recordings during the entire trip. The good team spirit between F4E, SIMIC, DAHER, overlooking the logistics, was essential to finding solutions.”
For Piergiorgio Aprili, F4E Magnets Technical Support Officer, the fact that this was Europe’s second coil to be manufactured came with some benefits. “We had already validated the processes and managed to make improvements which paid off in the fabrication of the magnet. The knowledge we acquired and the confidence we gained helped us move ahead. But due to COVID-19 we had to accept that we could not go to the factory for some time and consequently, had to follow part of the production remotely. This was a new working method that we had to come into terms with. I think we all came out stronger by building more trust both with our inspectors on the ground and our suppliers.”
It took approximately six weeks to complete the trip from the port of Marghera to the ITER site. On 4 September, F4E’s second Toroidal Field coil made it “home” paving the way for the next one expected towards the end of the year. “In the end, everything worked well in spite of the COVID-19 emergency,” concludes Alessandro Bonito Oliva. “This success relies on the work done upfront in the previous 12 years during which we created the foundations. Thanks to a robust manufacturing strategy and the rigorous processes devised during the previous phases, the production was successfully carried out in spite of the reduced physical supervision caused by COVID-19 restrictions. The use of automated processes, well defined procedures, and very skilled operators guaranteed the smooth completion of all steps. Finally, the good collaboration and constructive spirit among all parties, suppliers, F4E and ITER Organization helped to solve any issues encountered during the fabrication and transportation phases unfolding during the pandemic.”