Europe’s superconducting magnet is ready to confine the energy of the Sun
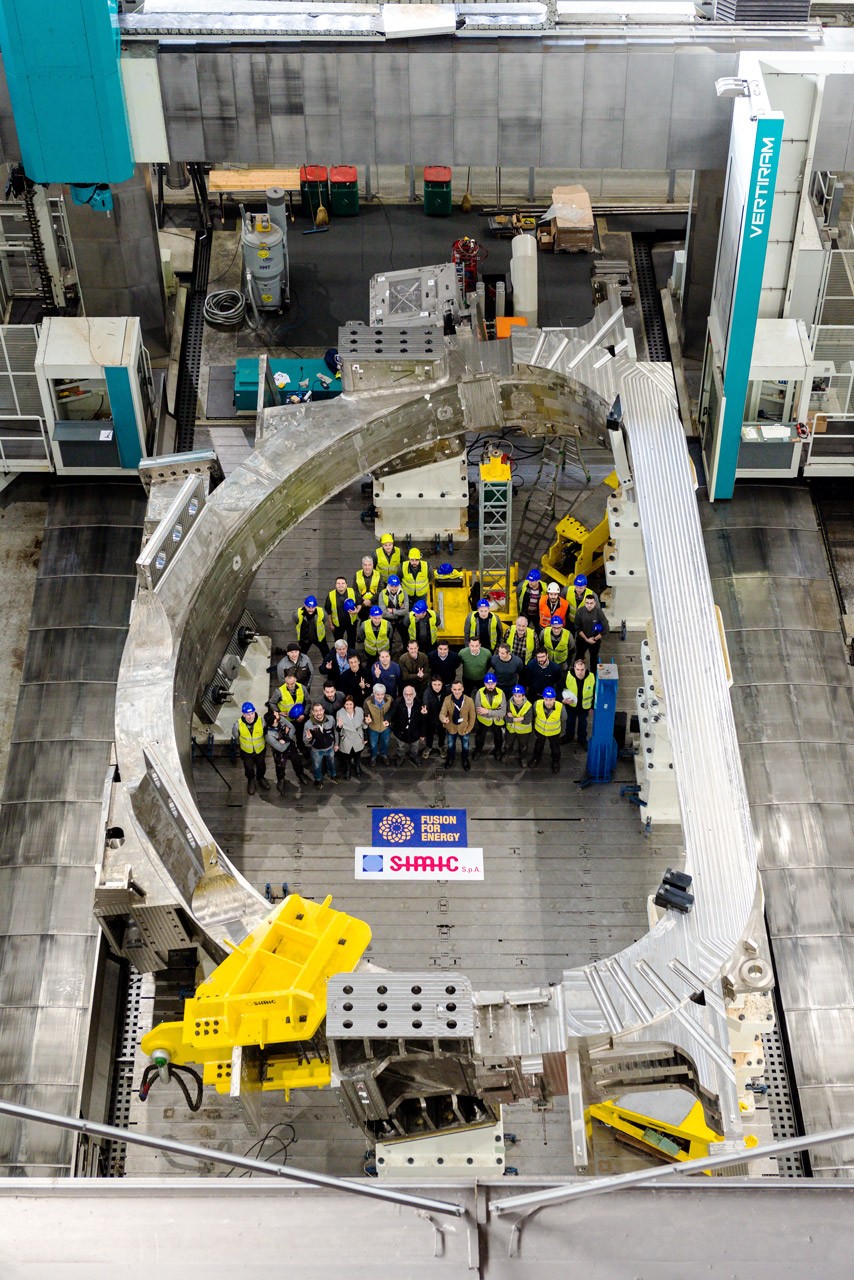
Europe’s first powerful superconducting magnet for ITER is ready. More than 40 companies, counting 700 people, have received money from the EU to manufacture this component. Nine more magnets are in production. F4E, SIMIC members of staff stand in the middle of the component (17 m high x 9 m wide, 320 tonnes). Picture taken at SIMIC factory, Marghera, Italy, March 2020.
This is the first of–a–kind magnet made in Europe and it will be part of ITER, the biggest international experiment in the history of mankind to test the potential of fusion energy—the power of the Sun and the stars which when replicated on Earth will help us enjoy limitless, safe, clean energy without greenhouse gas emissions.
ITER will use 18 of these magnets[1], known as Toroidal Field coils, to confine the super-hot plasma which will reach 150 million ° C. How?They will create a magnetic cage to keep the hot plasma away from the vessel of the machine. When powered with current (68 000 A) the magnetic field will reach up to 11.8 Tesla—about 250 000 times the magnetic field of the Earth! Each magnet measures 17 x 9 m and weighs 320 tonnes— as much as an Airbus A350. Europe’s magnet will be the first of the 18 Toroidal Field coils to be delivered to ITER, and will also be the first EU component of such size to be handed over to the project. The EU has financed the works of this high-tech component, through Fusion for Energy (F4E), the organisation managing Europe’s contribution to ITER, which has been collaborating with at least 40 companies, and more than 700 people, to produce the ten coils. The main contractors are SIMIC, ASG Superconductors, CNIM, Iberdrola Ingeniería y Construcción, Elytt y and the ICAS consortium. The manufacturing of the ten European magnetsunfolds in several factories.
Let’s discover the main locations of the factories involved in the production process:
-Turin (Italy), where ICAS produced the conductor;

-La Spezia (Italy), where ASG Superconductors, in collaboration with Elytt Energy, and Iberdrola Ingeniería y Construcción, collaborate for the production of the ITER Winding Packs, the inner-core of the magnets;

-Toulon (France), where CNIM produced the equipment to insert the conductor into the magnet and Marghera (Italy), where SIMIC produced similar equipment to insert the conductor into the magnet. At SIMIC the final steps (cold tests, and insertion into coil cases are also carried out).



Thanks to involvement of the EU in ITER, European industry has a unique opportunity to collaborate in this groundbreaking international experiment with China, Japan, India, the Republic of Korea, Russia, US. As a consequence, companies get to improve their manufacturing standards, to employ and train workforces, and last but not least, to acquire industrial expertise in an emerging energy market with potential economic and environmental benefits.
Alessandro Bonito-Oliva, F4E Programme Manager for Magnets, elaborated on the importance of this significant milestone for Europe. “This achievement results from 12 years of work involving more than 700 people and at least 40 companies. Many factors have made this possible: vision in developing the best procurement strategy and interfaces among suppliers; competence in defining the correct technical solutions; cooperation between the different parties to tackle issues in manufacturing the most complex magnet to date; and last but not least, passion, perseverance and the full commitment of a highly qualified team. Without any of these elements, it would have been impossible to complete this long journey.”
Marianna Ginola, SIMIC Commercial Manager, explained that “the completion of the first European Toroidal Field coil for ITER has been an important milestone for SIMIC. It has given us the opportunity to demonstrate our skills in complex manufacturing. Our staff has been working relentlessly to meet this objective and continues to do so for the remaining coils. We are proud to be part of the manufacturing supply chain of ITER, and to be involved in its final assembly through another contract.”
For Davide Malacalza, Chairman of ASG Superconductors, “the completion of Europe’s first ITER Toroidal Field coil is a significant milestone towards the energy of the future. Thanks to unique international projects research such as ITER, our know-how in magnet technology will have cost effective returns in the industrial and medical sectors as well.”
Philippe Lazare, CEO of CNIMIndustrial Systems, stated that “in order to manufacture our share of ITER components we had to upgrade our industrial facilities, establish new working methods and train new talent. In return, we have become a French reference in high-precision manufacturing for large components.”
For Aitor Echeandia, CEO of Elytt, there are clear benefits from their involvement in the fabrication of the ITER magnets. “Our SME has acquired further know-how in superconducting technologies for fusion and particle accelerators.”
Antonio della Corte, President of the ICAS consortium and Head of ENEA Superconducting Laboratory, explained that “our contribution to the superconducting conductor for the ITER magnets allowed us to develop new ideas which helped us improve our production technologies and transfer them in different applications.”
The coil is now ready to travel from Italy to France, and should arrive by boat a month later at the port of Fos-sur-Mer (Marseille). Then it will be transported to the ITER site, Cadarache.
