F4E and Ansaldo Nucleare unveil ITER Inner Vertical Target prototype
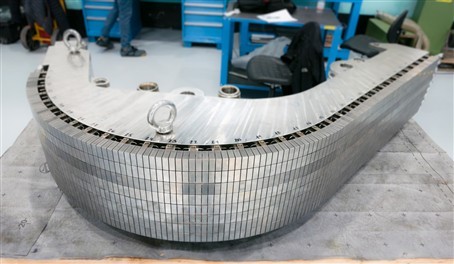

ITER has often been described as the experiment that will put a sun inside a box. Naturally, one question that comes to mind is: what kind of material can sustain its superhot plasma of 150 million °C— ten times the temperature at the core of the sun? Will it not melt? The answer is that not all components will be exposed to the same level of heat power. Within the same machine, magnets will be frozen with liquid helium at -269 °C to become superconducting so as to confine the superhot plasma, and in less than one metre away, in-vessel components will be exposed to extremely hot temperatures. Roughly 20% of the plasma heat will be directed to the ITER Divertor, targeting components installed on each of the 54 Divertor cassettes that will be facing the plasma. The Inner Vertical Target, located on the upper part of the cassette, is one of these components. The maximum expected temperature on the tungsten surface will be about 1000 °C in normal operating conditions and about 2000 degrees °C in off normal conditions, the so-called slow transient event. Its manufacturing has been considered rather challenging because Europe’s industry has not previously produced it at such scale and with these specifications. But, with ITER there is always a first time for everything.
Apart from the fabrication of the 54 ITER Divertor cassettes, F4E has to deliver the Inner Vertical Target for each of them. With the help of Ansaldo Nucleare, and its main subcontractors Ansaldo Energia, ENEA and Walter Tosto, Europe’s first-ever full scale prototype of the ITER Inner Vertical Target is ready. The component, weighing 0.5 t and measuring approximately 1.5 m, has been recently unveiled at the workshop of the manufacturer in Genoa, Italy. Its surface is covered by 1104 tungsten blocks, which resemble to steel-made tiles. The blocks will be facing the hot plasma and are piled up on copper alloy pipes in which pressurised water will flow to cool down the component. We spoke to Bruno Riccardi, F4E Divertor Technical Co-ordinator, to understand better the manufacturing process. “First, we need to acknowledge the years of R&D that we have capitalised on to get where we are. We started more than 20 years ago developing the concepts of this component. Then, we made the transition to manufacturing and addressed several challenges. For instance, we needed to optimise the bonding between the tungsten blocks and the copper alloy pipes to ensure the required heat removal and their overall performance. Furthermore, the positioning of the blocks is fundamentally important in order to avoid the concentration of heat on some, rather than the even distribution to all, resulting in the melting of tungsten” he explains.

In a few days, the plasma facing units will leave from the north of Italy to travel to Russia. It will have to undergo a series of thermal tests at the Efremov Institute in Saint Petersburg. Pierre Gavila, managing this contract on behalf of F4E, elaborates on what will follow. “At the ITER Divertor Test Facility, the component will go through cycles of high power electron beam irradiation for roughly three months. On the basis of the results, we will be able to achieve an important milestone towards the qualification for the series production scheduled to be launched in 2021”. For F4E, the successful completion of the prototype has been an important milestone proving that the component can be manufactured according to the demanding specifications. The joining of all the parts and the geometrical features of the component did not make life easy for the technical teams involved, but in the end, they made it. Gian Paolo Sanguinetti, Ansaldo Nucleare Fusion Business Leader, explains in more detail. “We are proud of the fabrication of the Inner Vertical Target component achieving the challenging assembly tolerances. No final machining of the plasma facing units was necessary, avoiding the associated risk and cost. This confirms the soundness of the Ansaldo fabrication process and makes the Inner Vertical Target prototype a real pre-production component. We believe that this result is of real value to our present and future customers, by significantly reducing any technical uncertainties.