F4E vacuum vessel forgings are progressing
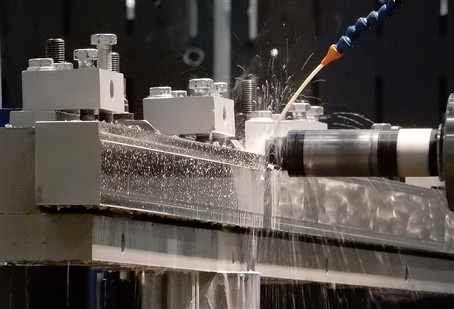

Within the framework of the contract between F4E and the AMW consortium (Ansaldo Nucleare S.p.A, Mangiarotti S.p.A and Walter Tosto S.p.A) for the fabrication of 7 vacuum vessel sectors for ITER, stainless steel forgings, which will used in the manufacturing of these sectors, are currently being produced.
The ITER vacuum vessel is located inside the cryostat of the ITER device and its basic function is to operate as the chamber that hosts the fusion reaction. Within this doughnut-shaped vessel, or torus, plasma particles collide and release energy without touching any of its walls due to the process of magnetic confinement. Each vacuum vessel sector is 13 metres high, 6.5 metres wide and 60 cm thick. The weight of each sector is approximately 500 tonnes and the weight of the entire component, when welded together, will reach an impressive total of 4,500 tonnes which is equivalent to the weight of the Eiffel Tower.
Three sub-contractors, Rolf Kind GmbH (Germany), Acciaierie Valbruna (Italy) and ThyssenKrupp (Germany), have carried out the task of producing different kinds of forgings which will be used on the first three of the seven sectors (out of the total nine) that Europe is contributing to the ITER project (the two other sectors of the vacuum vessel are supplied by Korea). For the first three sectors, around 1,000 forgings will be produced in various different shapes and sizes. They are of several different weights, although the maximum weight of a forging produced is 10 tonnes, depending on what part of the vacuum vessel it will be assembled into. The total of different forgings will weigh around 300 tonnes per vacuum vessel sector.
The forgings consist of big blocks of 316 LN ITER grade stainless steel (a type of steel which is made up of a low carbon and high nitrogen content). These blocks have been produced by mixing pellets of materials such as chromium, nickel, and of course, steel. The mixture is heated to a temperature of approximately 1,500 degrees C and poured into moulds for cooling. “Following production of these square blocks of steel, where the metal is shaped of using hot pressing – the steel block is heated to a temperature of approximately 1,000 degrees C and then hammered into shape using a large steel hammer,” explains Angel Bayon, F4E Senior Technical Officer.
While the blocks are being produced by sub-contractors, the first available blocks will be shipped to the Mangiarotti S.p.A and Walter Tosto S.p.A premises for machining (when the steel block will be cut into a desired final shape and size). Following completion of machining, they will be welded in order to create parts of the vacuum vessel segments.
“We are very proud to have worked on the procurement of the vacuum vessel forgings as they are vital in contributing to the fabrication of the ITER vacuum vessel sectors, the heart of the ITER machine”, says Francesco Zacchia, Project Manager for F4E’s Vacuum Vessel team.