Fabrication advancing for largest superconductive magnets
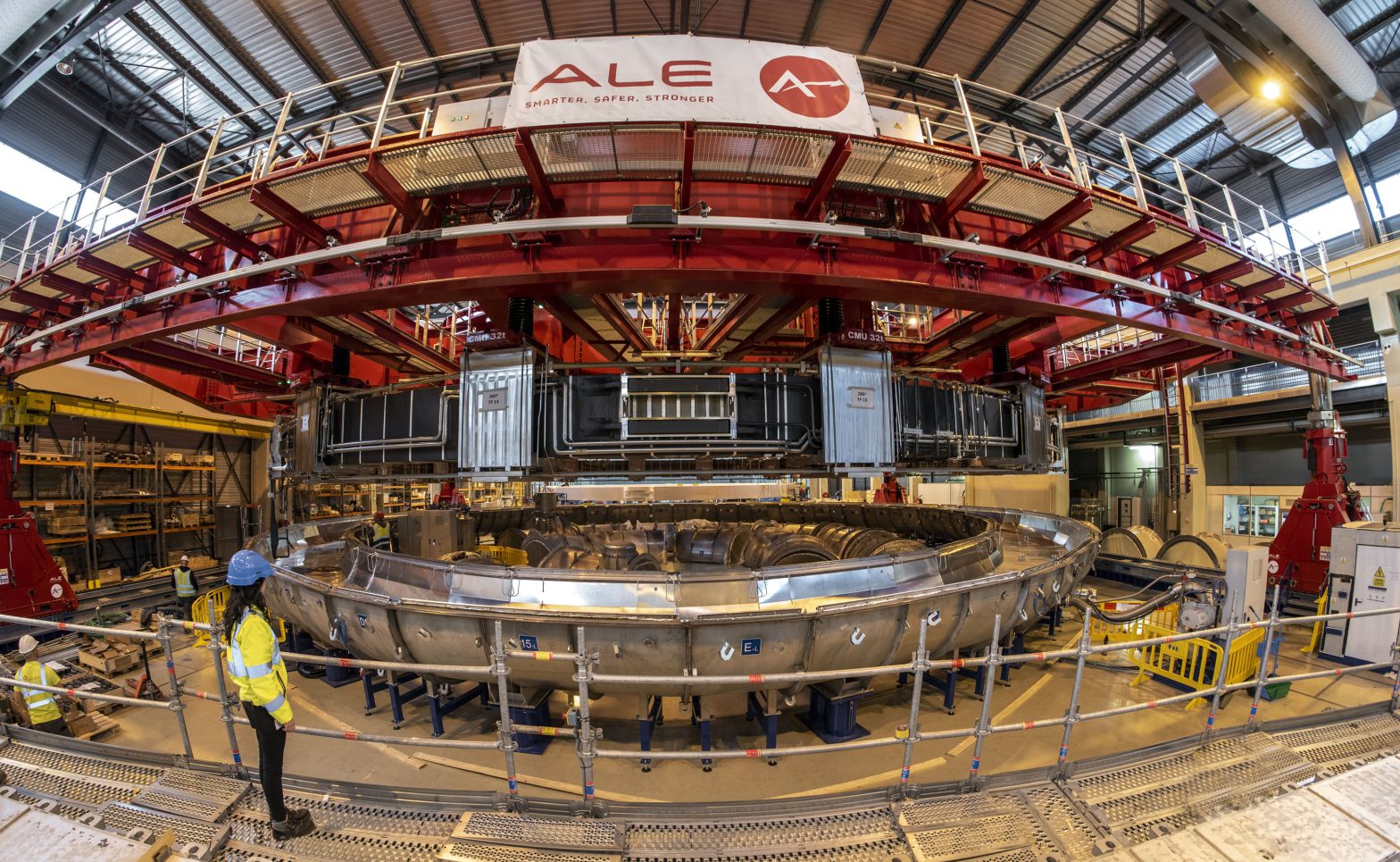
ITER's fourth Poloidal Field coil (PF4), produced by F4E, installed in the cryostat to start cryogenic tests at 80K. PF coils factory, Cadarache, February 2023 © ITER Organization
Saving the best for last is what Europe has done with the fabrication of the final two Poloidal Field (PF) coils. These two massive magnetic rings that will embrace the hot plasma from top to bottom, measure 24 m and weigh at least 350 tonnes each. They are not only the biggest PF coils of the ITER device, but in fact, they will be the largest superconductive magnets. Made in Europe, under the management of F4E, and in collaboration with 12 companies, involving more than 150 people working on the project.
The 300 m-long facility, the longest building on the ITER site, looks less cluttered than before because some of the tooling stations have been dismantled. The winding and wrapping of the electric insulation of the conductor, has been completed resulting into Double Pancakes (DPs) – flat spiral coils. Getting there, however, was no easy task. A team of experts from Sea Alp reconfigured the tooling in the facility to allow technicians from CNIM and ASG Superconductors to produce 8 DPs for each of the two last coils. And all this during the peak of the pandemic with travelling restrictions in place, self-distance measures, and new protocols on health and safety. A totally new reality which we had to become accustomed to produce the biggest superconductive magnets.
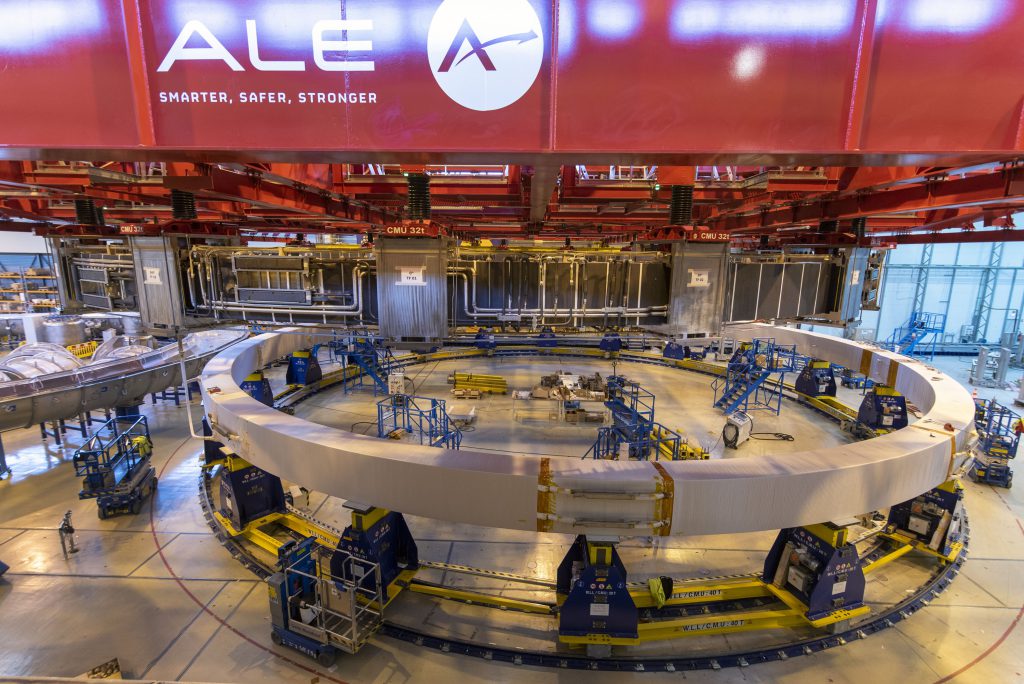
The manufacturing of PF4 started in July 2020 and later this year, around summer, it will be handed over to ITER Organization. PF 3 will soon follow, scheduled to be completed by spring 2024. There is a sense of accomplishment because our teams have successfully capitalised on the experience gained from the fabrication of other coils. For example, compared to PF5, they managed to cut down production time by 30% although they worked with a component which was 40% bigger.
Having concluded the stages of stacking, impregnation, assembly, and electrical checks, PF4 is now ready for cold tests. What do they entail? The coil will be inserted into a cryostat, where it is cooled down to -193 °C (80 K) a process which takes 20 days so that engineers perform the necessary tests. Once they are over, the component will go back to room temperature in order to carry out the final acceptance tests, so as to make sure that it withstands the mechanical stresses experienced during the thermal cycle with no technical failures. Mónica Martínez, F4E Technical Officer for PF coils, following cryotests closely, explained: ““This is the first time that we are going to cooldown a coil of such complexity and dimensions which is a challenge we have been preparing for. The full team is very excited about the months to come.”
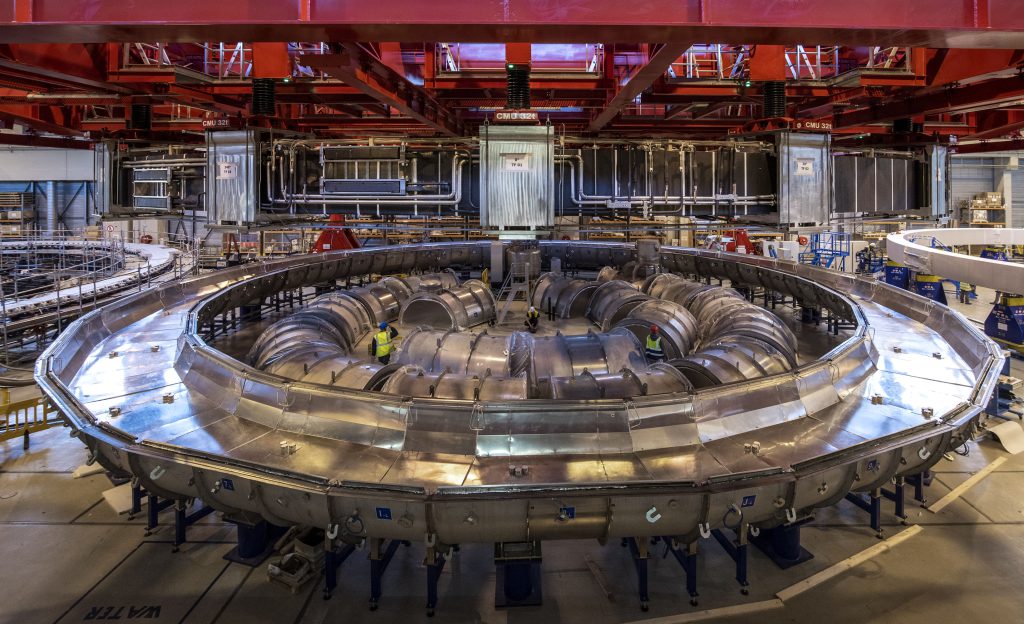
As for PF3, the 8 DPs have been completed ahead of the schedule. Ground insulation activities are nearing to their end, and the coil will soon be transferred into a gigantic station to go through impregnation with epoxy resin. Ander Loizaga, F4E Technical Officer, following this technical area closely, gave us some background. “This year we will carry out our largest and final impregnation with the winding pack of PF3. These last five years have been very intense performing this activity with other coils. And in spite of all the challenges we faced, we remain enthusiastic and fully committed to delivering Europe’s last poloidal field coil.” Pedro Carvas, F4E Technical Officer, offers a sense of optimism and caution. “The end of manufacturing is round the corner. We are getting there! But just we because we start seeing the end, it does not mean we can be complacent. We all need to remain focused and pay extra attention to every step.”
To watch the lifting operation of PF4 and its insertion in the cryostat click below