Final countdown for three ITER vacuum vessel segments
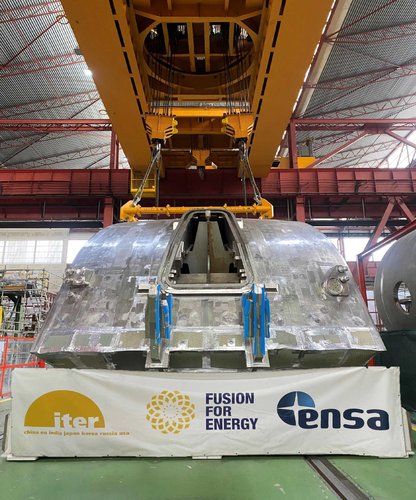
Poloidal Segment 4 of Sector 3 completed in ENSA’s factory, Spain. The component, part of Europe’s contribution to ITER for vacuum vessel, will be transported to Italy to join the rest of the pieces of the same sector to be welded. June 2023 ©ENSA
The ITER Vacuum Vessel is the chamber that will house the fusion reaction. Inside this toroidal container made of stainless steel, the super-hot plasma will be magnetically confined. Europe will deliver five of the nine sectors, while the remaining four will come from Korea. Each sector, consisting of four segments, is 12 m high, 6.5 m wide, 6.3 m deep. When all nine sectors are welded together the total load of the component is expected to reach 5 000 tonnes.
F4E is working with the Ansaldo Nucleare, Mangiarotti, Walter Tosto (AMW) consortium for the sectors to be produced in Europe. This partnership brings together at least seven companies located in Spain, Germany, Italy, involving more than 200 employees. The works performed in each factory range from welding and machining to quality assurance checks, ultra-sonic tests, assembly and transportation of the components. The list of technical tasks is endless because this piece of equipment has not been manufactured before at such scale. The inspections carried out are thorough to detect any non-conformities, and to guarantee compliance with the standards set by France’s Nuclear Safety Authority.
For every technical hurdle on the way, the team of engineers has demonstrated remarkable resilience to figure a way out. Their commitment is their main driving force, together with the thrill to break some barriers. As works unfold in different factories, each industrial partner gets an opportunity to learn, test, and acquire more expertise using new technologies. Collectively, we draw important lessons that will influence the supply chain of future fusion reactors.
ENSA is one AMW subcontractors, responsible for the production of five European segments in total. Their involvement in the fabrication of the vacuum vessel is seen as a success story. Four of the five segments have already been completed. The company boasts a proven track record on performing welding operations with robots- viewed by many in the community as a game changer. It’s quicker, more reliable and with less non-conformities compared to manual welding. A team of operators, specifically trained to use these machines, has mastered the technique even on challenging surfaces, like those of the segments, known for their tricky geometry. Click here to view how ENSA’s robots performed the task.
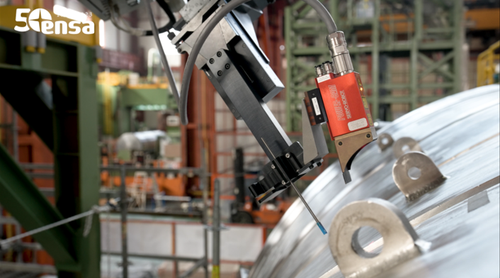
“ENSA is nearly finishing one of its most important works (the delivery of the PS1 and PS4 segments), part of three European vacuum vessel sectors under the responsibility of F4E and the AMW consortium. This has been one of the most important technological projects in the 50 years of ENSA’s history, which it commemorates this year. Our team overcame all the challenges that the work demanded, both in terms of geometry and manufacturing requirements. Specific solutions were adopted to produce these high-quality components with the firm commitment to meet our customer’s expectations. Passion for improvement in innovation, development and research define ENSA. The team is proud to be part of ITER project, to which it has given its best skills, competences, and contributed with professionalism,” explains Miguel A. Andérez, ENSA Operations, Design and Projects Vice President.
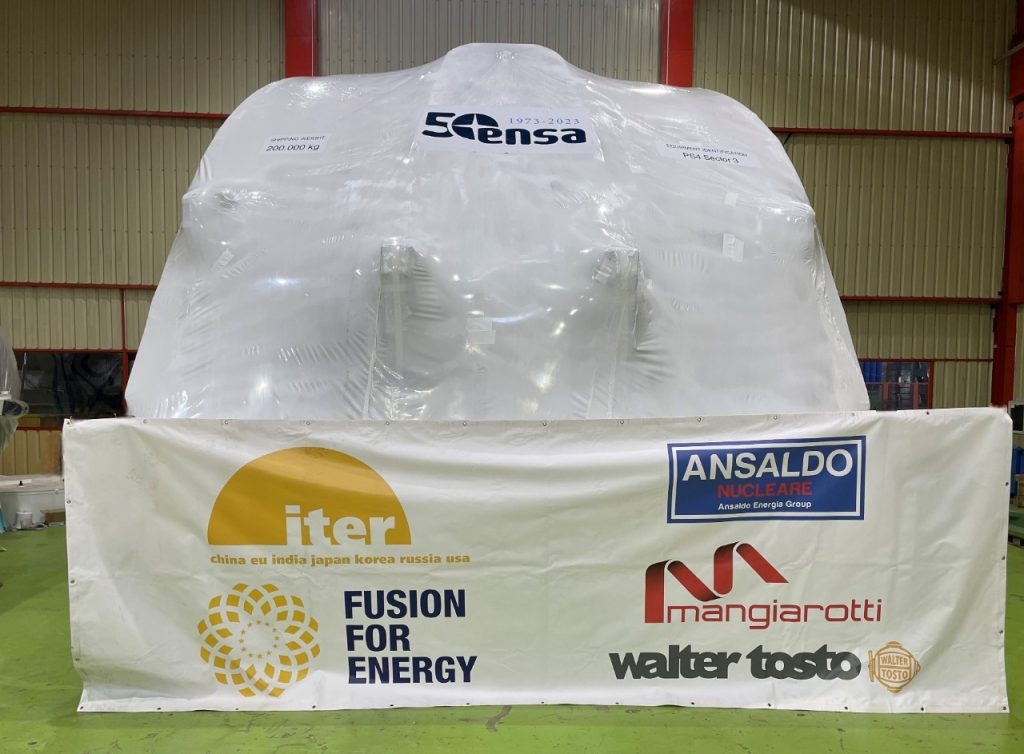
Miguel Gonzalez Fernandez, F4E Site Manager at ENSA, was there to witness the progress of the final segments. “I think what is most gratifying in this context is to see how we have ramped up activities and improved the pace of delivery. That’s mainly because we understand better the complexity of the component of the vacuum vessel and ENSA has a solid grasp of the robotic welding technique. It’s a win-win for all parties. We have built a partnership based on our capabilities, followed thorough processes to detect any issues, and established a good collaboration to address anything in an open and constructive manner.” The involvement of Tecnatom, contributing to the ultrasonic tests, was conducive to the project’s success by offering additional guarantees on the quality of the work carried out.
Two of the segments are expected to depart from Santander, Spain, in June, leaving the final one for autumn. They will travel by sea to join the other segments in Italy, where the factories of the AMW consortium are located. As ENSA is closing its final chapter in the manufacturing of the vacuum vessel, a new chapter is starting with the assembly and welding of Europe’s sectors.