First of the six ITER Poloidal Field coils manufactured
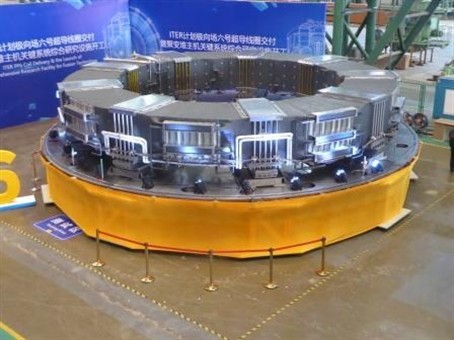
Europe (F4E) and China (ASIPP) complete manufacturing of Poloidal Field coil six (PF6). The magnet, which weighs 400 t and has a diameter of 10 m, was unveiled at the ceremony which took place in the workshop of ASIPP, Hefei, China, September 2019.
Powerful superconductive magnets hold the key to ITER’s success in demonstrating the potential of fusion energy. The superhot gas resulting from the reaction will be confined by 18 Toroidal Field (TF) coils which will generate a strong magnetic field keeping it away from the walls of the vessel. In parallel, six massive magnetic rings, known as Poloidal Field (PF) coils, will embrace from top to bottom the TF coils and the vacuum vessel to control the shape and stability of the hot gas.
Delegates from the teams of Europe and China gathered in Hefei, at the seat of the Institute of Physics of the Chinese Academy of Sciences (ASIPP), to celebrate an important technical milestone – the completion of the first out of the six PF coils. This happens to be sixth Poloidal Field coil, known in the jargon of the ITER project as PF6. F4E, managing Europe’s contribution to ITER, and ASIPP, established a partnership nearly six years ago to produce PF6 so as to facilitate the exchange of technical know-how and deliver the component on time. The remaining four PF coils that Europe is responsible for are being manufactured on the ITER site. Russia is also responsible for the production of one of the PFs.

Nearly 100 people were involved at various periods of time to produce PF6, which weighs 400 t and measures 10 m in diameter. Members of F4E and ASIPP worked as one team under the supervision of Europeans. It took roughly three years to finalise the qualification stages plus another three to complete fabrication. Timing is of paramount importance because the sixth and fifth PF coils will need to be fitted in the bottom of the cryostat of ITER device in the second half of 2020 before the TF coils and parts of the vacuum vessel are fully installed.
During those six years, European representatives rotated on the premises of ASIPP and the staff based there worked long shifts even during the weekends if needed. Bearing into consideration that this was the first of a kind, the teams managed to defy the odds. During the ceremony, Jean-Marc Filhol, F4E’s Head of ITER Programme Department, paid tribute to the members of staff from ASIPP, F4E, and ITER Organization, who contributed to this successful outcome showing high levels of motivation and dedication.

Manufacturing this component presented various engineering challenges. A total of 18 spools of superconducting cables – each measuring 720 m long – were manufactured through a collaboration between Russia and Europe. The cables were delivered to ASIPP where they were wounded to form the inner layers of PF6. Peter Readman, Technical Officer, and Carlo Sborchia, Technical Responsible Officer, following closely the production on-site, identified the most delicate steps. “There are 17 joints which have to be perfectly made to avoid any potential quenches during operation. A quench occurs when the coil or joint is no longer superconducting. If the joint becomes resistive then a lot of stored energy can be released and potentially damage the magnets if the current and energy stored are not dumped quickly (in the order of 10 sec),” explains Peter. Carlo explains that “…the impregnation with epoxy resin under vacuum has been one of the greatest challenges on such a large coil, due to the complex geometry with many cooling inlets on the inside and joints outside.”
PF6 will have to pass some final checks and acceptance tests before it leaves China. The component will head to Shanghai by barge and from there it will travel by boat to Fos-sur-Mer, the industrial port of Marseille, via the Suez Canal. Its delivery to the ITER site is scheduled for early next year. When it gets there, the F4E teams will perform final acceptance tests, plus further electrical, leak and cold tests.