First sector of Vacuum Vessel is coming together
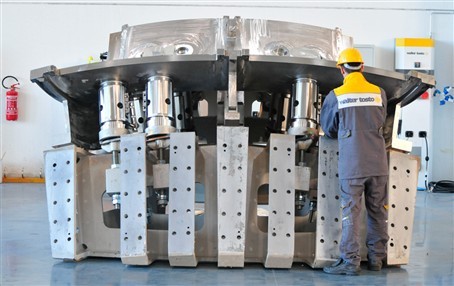

The ITER Vacuum Vessel, the heart of the ITER machine which houses the fusion reaction, is a veritable piece of art. With its massive dimensions its shape necessitates massive stainless steel pieces of metal being joined together by welding challenging geometrical forms. Each sector of the Vacuum Vessel consists of four poloidal segments joined together and for the first time, smaller parts of a poloidal segment have been welded together to form a bigger piece – the first sub-assembly of the poloidal segment 2 of Vacuum Vessel sector 5. This is the first piece which exemplifies how forgings in different sizes are machined into different shapes which are then joined together and welded onto two very large stainless steel plates which make up the first part of a Vacuum Vessel sector. In total, this sub-assembly boasts a length of 2.2 metres, a width of between 2.3-3.3 metres, and a height of 35-50 centimetres. In total, the sub-assembly weighs over 6 tonnes.
The AMW consortium, consisting of companies Ansaldo Nucleare S.p.A, Mangiarotti S.p.A and Walter Tosto S.p.A and in charge of supplying five sectors to F4E, have been dealing with this crucial sequence in the fabrication of F4E’s contribution to the ITER Vacuum Vessel. It was carried out jointly at the AMW sub-supplier ProBeam facility in Germany and at the Walter Tosto facility in Italy.
“The successful completion of the welding of this part of Vacuum Vessel sector is an important milestone which shows that we are on the right track in fabricating the Vacuum Vessel sectors that we will be delivering to ITER”, says Francesco Zacchia, F4E’s Vacuum Vessel Project Team Manager.
In total, 20 weldings, with an overall welded length of around 25 metres, were completed during the short time period of two days. Initially the separated, smaller parts were assembled together at the Walter Tosto facilty and then transported to ProBeam electron beam welding chamber (the only such big chamber existing in Europe – it has a volume of 6300 m3, roughly the same volume as an Olympic-size swimming pool). Each individual part is welded separately in the vacuum chamber – the complexity of the welding technique and the precision needed means that each welding takes around three hours to complete.
“F4E and AMW have worked together intensely to ensure a successful outcome of this manufacturing. I am grateful to AMW staff who have worked both double and triple shifts and during weekends in order to keep the tight schedule on track and bring about this achievement. We see this development as a stepping stone to full fabrication”, says Francesco Zacchia.
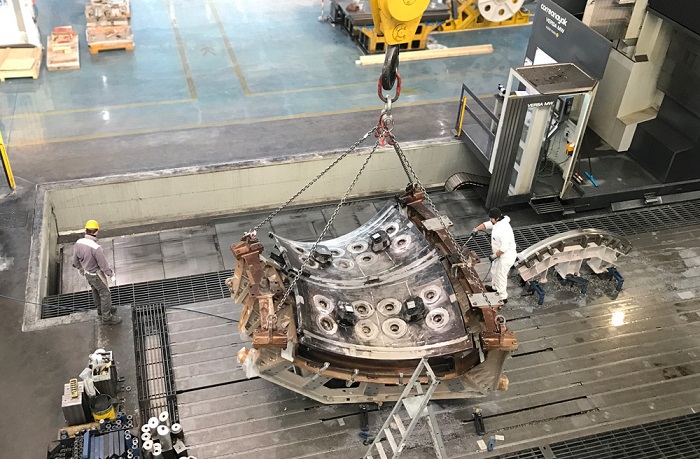
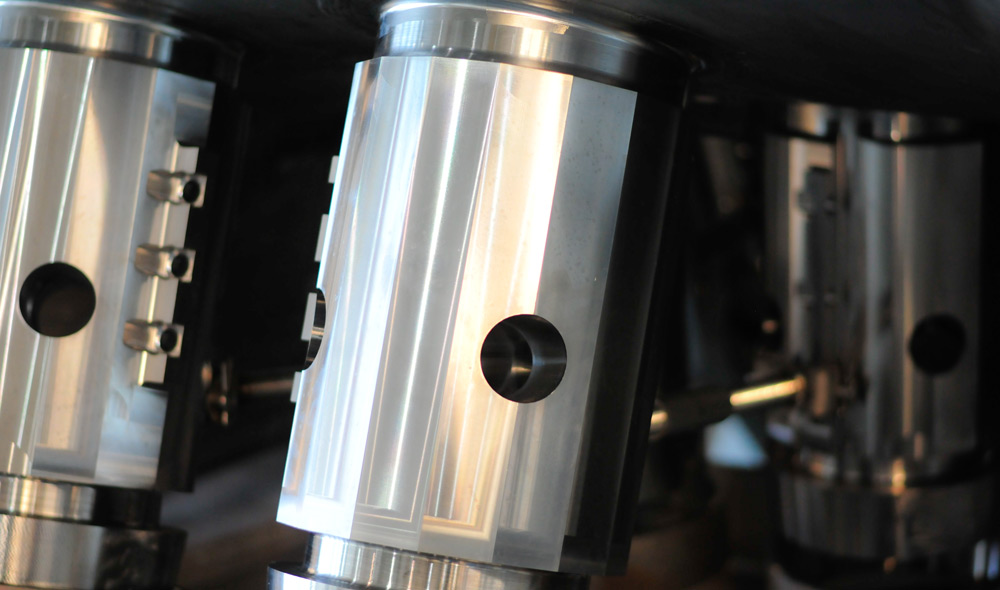
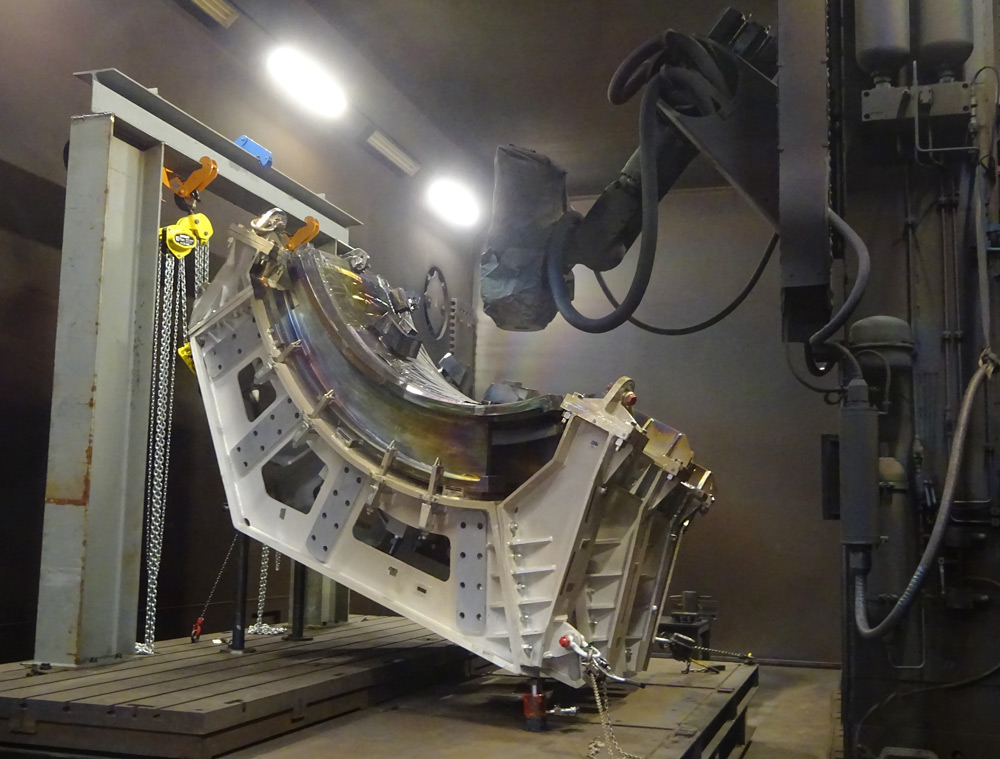
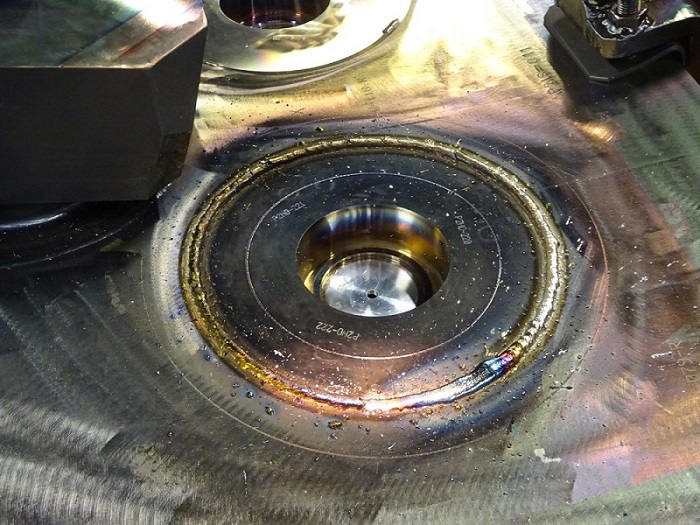