How will tritium move inside ITER and DEMO?
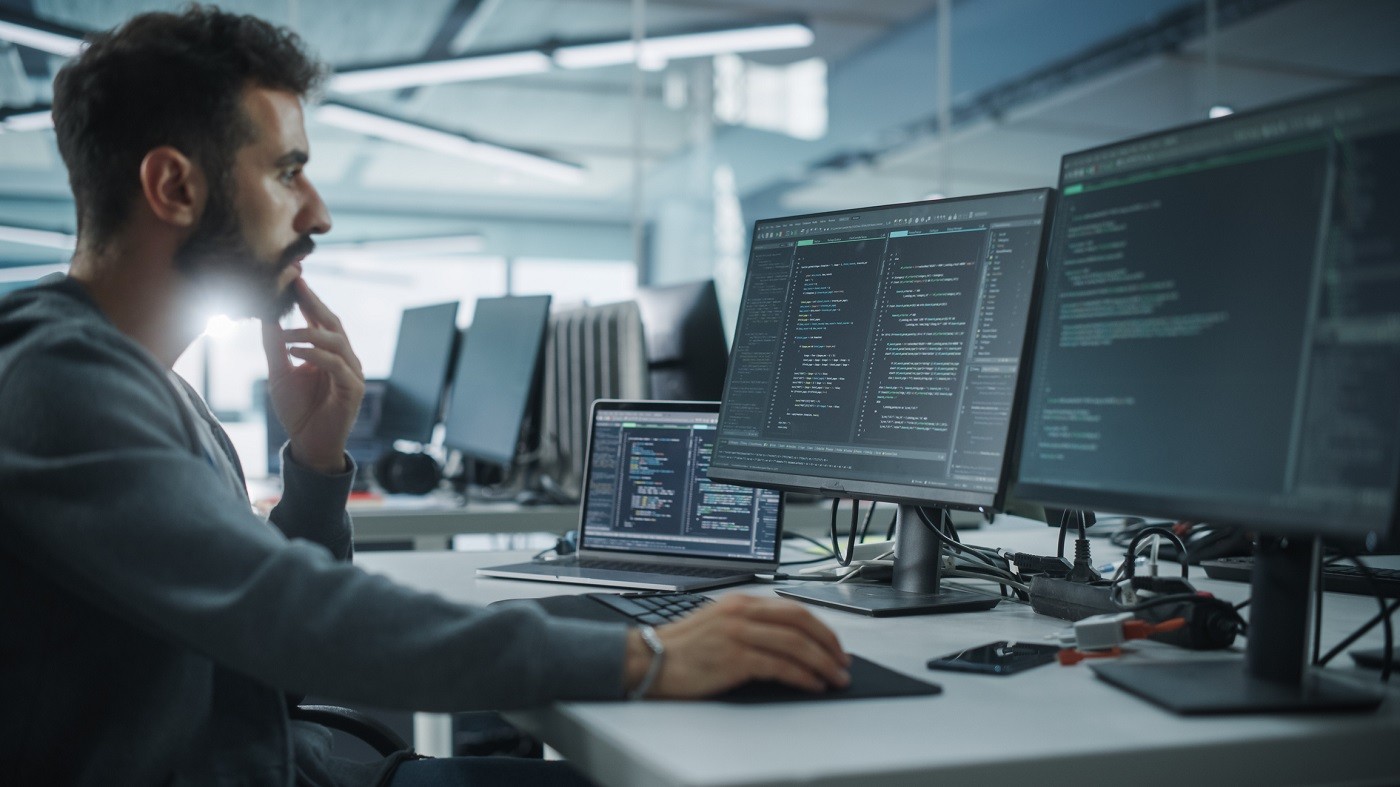
Computer modelling helps scientists simulate the behaviour of complex phenomena such as the motion of tritium in ITER.
Fusion devices that will come after ITER, such as DEMO, will require the so-called “tritium self-sufficiency”, the capability to produce the amount of tritium consumed in fusion reactions in a given period. This will be accomplished by the breeding blanket, a big structure containing lithium-based materials (lithium is needed to convert the neutrons produced in fusion reactions into tritium) located in the vacuum vessel. Tritium transport modelling allows experts to predict how the tritium generated in the breeding blankets will move towards the systems that have to recover it in order to refuel the plasma.
This is one of the areas developed by the European Test Blanket Modules (TBM) Programme, which will use ITER to validate two types of breeding blankets that will be developed and installed in DEMO. The Test Blanket System (TBS) includes the TBM box —the plasma-facing component where tritium is generated— and several sub-systems through which tritium will circulate before joining the inner fuel cycle —the system that feeds tritium into the vacuum vessel.
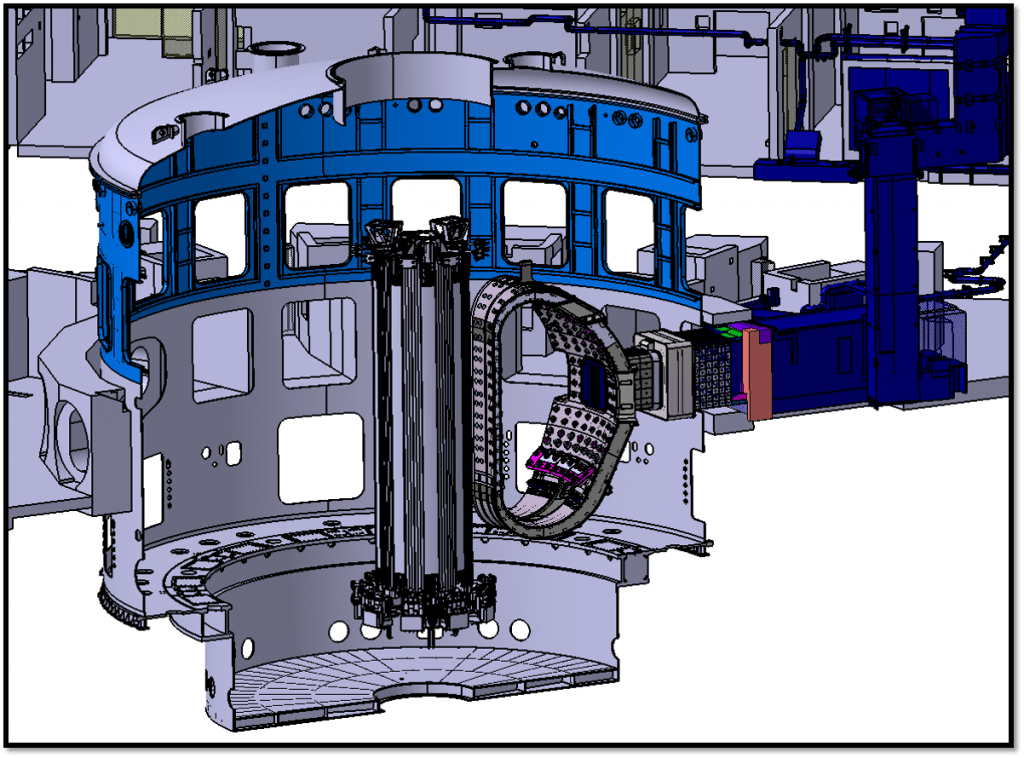
Why do we need to model tritium transport? Mainly for two reasons. First, tritium does not simply go from point A to B. It is a gas that diffuses easily, especially at high temperatures, and as its atoms are so small, it can enter and mix with the materials in pipes, valves and other components it finds along the way. Second, tritium is radioactive, therefore, it is of high interest to know where it might accumulate.
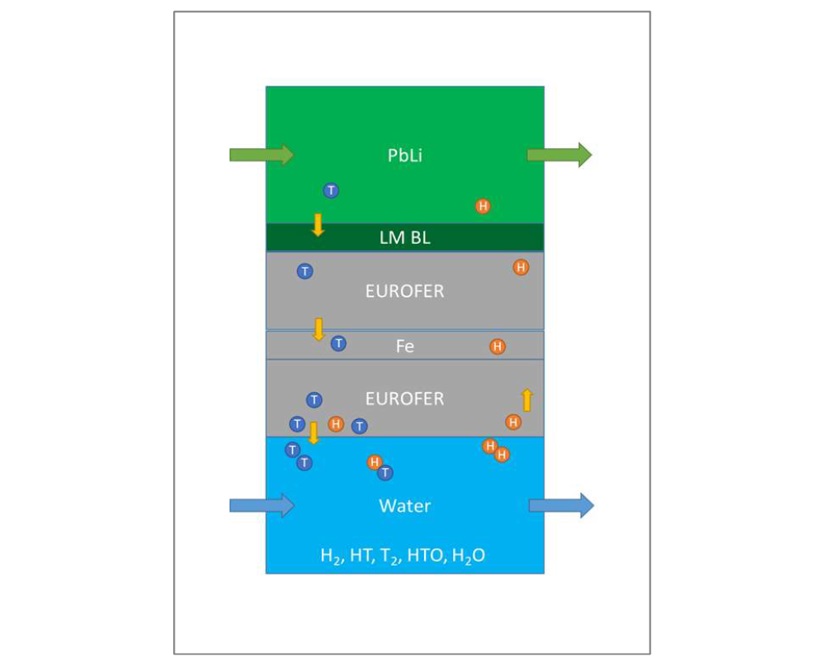
The TBM Programme is very involved in the development of the tritium transport modelling. Thanks to a long and fruitful collaboration from 2011 to 2018, between F4E, CIEMAT (Spain) and Empresarios Agrupados (Spain), a first version of the “EcosimPro” simulation code was developed. It implements the physics of tritium transport in the different TBS subsystems. Since then, following an agreement between F4E and EUROfusion, the activity has continued with the same contractors but under the co-ordination and budget of EUROfusion.
At present, experts are working to include in their modelling more detailed physical phenomena and more accurate descriptions of components such as tanks, heat exchangers or valves. For instance, EcosimPro currently does not take into account a phenomenon called tritium trapping: fusion neutrons hitting the TBM box cause the appearance of tiny damaged parts (defects) in the steel (EUROFER). A significant amount of tritium could get trapped and accumulate in these defects, depending on the type of material and the conditions of neutron irradiation. This is complicated to take into account, but must be considered as it can have an important impact on the mapping of the tritium in the system. IPP Garching is developing “TESSIM”, a specific code devoted only to the TBM box and breeding blanket modules that simulates this phenomenon accurately.
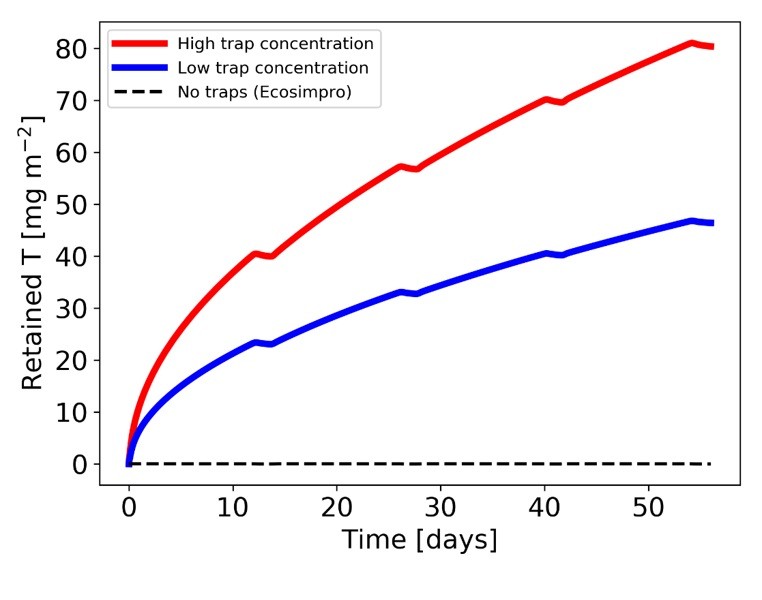
The objective is to achieve a more comprehensive simulation code by the end of 2025, coinciding with the end of the Final Design phase for the TBM Programme. Italo Ricapito, F4E Project Manager and Chief Engineer of the Water-Cooled Lithium Lead TBS Project, offers his insight. “Counting on the collaboration with IPP Garching, we intend to use TESSIM to have a more precise understanding of the tritium behaviour in the TBM box. Once we combine the EcosimPro code with TESSIM and verify the code in terms of predictive accuracy (with appropriate experimental campaigns in ITER), we will have gained important knowledge for the design of the DEMO breeding blankets, which is one of the main objectives of the TBM Programme.”