Is robotic welding quicker and more precise?
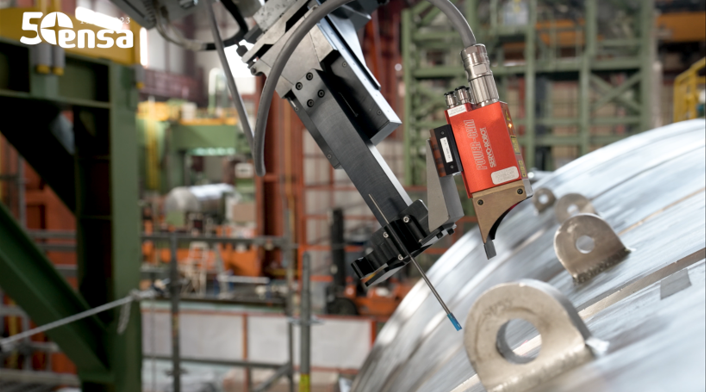
One of Europe’s segments where ENSA performed welding operations with the help of robots, ENSA, Spain, March 2023 © ENSA
Fusion is often described as putting a small sun inside a box that will be connected to the grid. It’s a new energy attracting a lot of interest because it does not emit greenhouse gases, it comes with strong commercial benefits, and offers Europe the possibility to be less dependent on third countries for its power supply. However, creating an artificial “sun” and developing “the box” is no easy feat.
The fusion reaction, which is expected to reach 150 million °C, will be housed inside a toroidal double-walled shell made of stainless steel that will be hermitically sealed, known as the vacuum vessel. Powerful superconducting coils will embrace the container, creating a magnetic cage, so that the hot gas will float without touching any of its walls. And although this may sound like science fiction for some, accomplishing this dream is the daily reality of those involved in the ITER project. Europe is responsible for nearly half of it, and in the case of the vacuum vessel, it is providing five out of its nine sectors, while the remaining four will be provided by Korea. Each sector consists of four segments which need to be assembled to form one sector, and each of the nine sectors will need to be joined together to form the vacuum vessel. To understand the size and load of the “box” we are talking about it’s worth keeping in mind some figures. Each sector is 12 m high, 6.5 m wide, 6.3 m deep and weighs approximately 500 tonnes. When all nine sectors are welded together, they will reach a total of 5 000 tonnes.
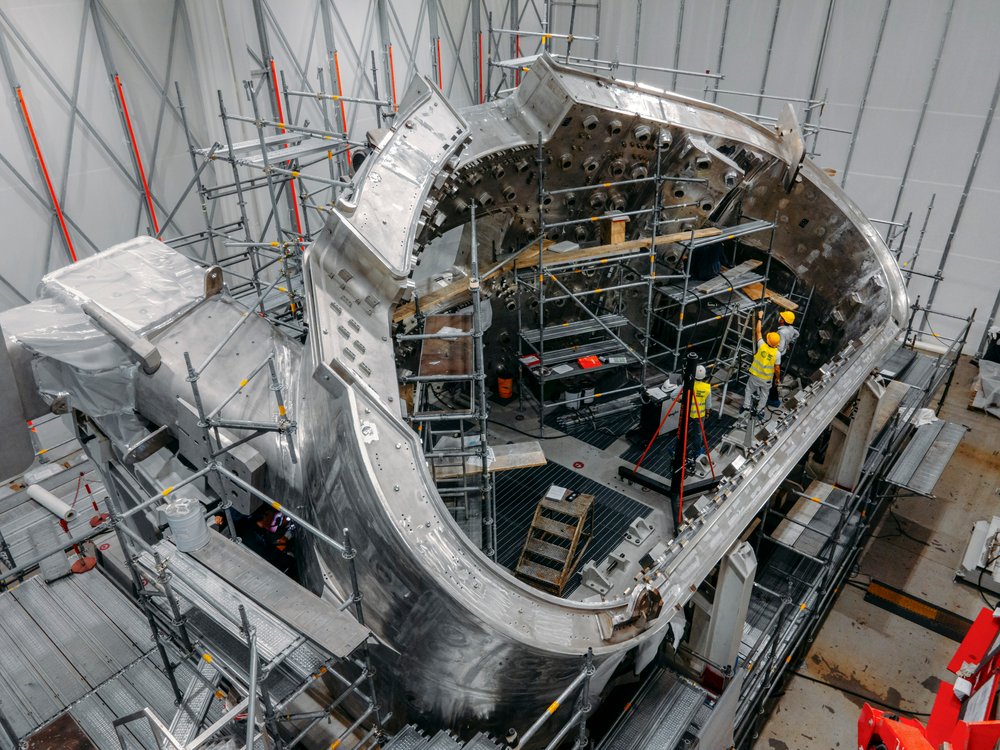
F4E has entrusted the AMW consortium (Ansaldo Nucleare, Mangiarotti, Walter Tosto) and their contractors, with the production of Europe’s five sectors. Various techniques are applied in the different workshops, and any lessons learned will help engineers produce the fusion reactors of the future. One of the areas of key importance is welding. We are talking about 1500 m of welds roughly per sector, where some are performed manually and in other cases with the help of robots. Checking meticulously the surface of each sector is necessary to identify any distortions that would need to be fixed, while ensuring strict compliance with the nuclear standards.
In northern Spain, ENSA, has a large facility where five of these segments are welded. Nearly four months ago, the first of them left for Italy to form part of a sector. Recently, a second one was shipped, and towards the end of April another one is expected to depart. The secret lies in the technique used by ENSA performed with welding robots. Initially, the first 20 mm are welded manually, while the remaining 40 mm with the help of robots.
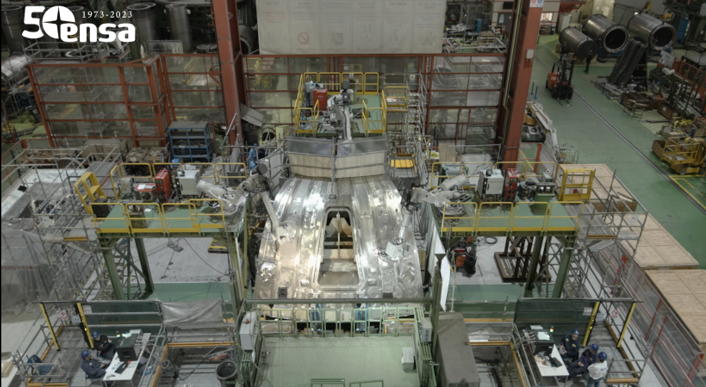
At first glance, robots seem less flexible compared to humans performing this task, but as it turns out there are substantial time savings and less distortions. The ENSA project team involved in the manufacturing of the ITER segments for F4E consists of about 17 people dedicated full time, both engineers and technicians, from different areas. As far as the robotised equipment is concerned, it is operated by a qualified and trained welder under the supervision of ENSA engineers in 24/7 shifts. The three robots are used in parallel for welds in three directions. To illustrate the precision gains, we have calculated that on average out of the 90 m of welds only 1 m needs repairs.
We spoke to Miguel Gonzalez Fernandez, F4E Site Manager, who has been following the works at ENSA. “It has been a privilege to be involved in the follow-up of ENSA activities. The professional attitude, and the great experience in manufacturing complex nuclear components, have been instrumental to the manufacturing of these segments. Furthermore, their expertise in the different welding processes, both manual and robotic, has been clearly demonstrated in the quality of the work.”
With the help of ENSA, we went back in time to understand more about the R&D history of these robots and the company’s knowhow. The first trials started in 2000 but it was not until 2013 when they started performing automatic welding activities with robots on nuclear components. For the European sectors of the ITER Vacuum Vessel, the design and development of robots started in 2018 and was done entirely in-house by ENSA engineers, in order to weld inner and outer shell pieces. For the welding of PS1 segments, a section of the vacuum vessel, two different pieces of equipment were designed and used, while for PS4 segments, a system to perform automatic welds with up to three robots in parallel was developed.
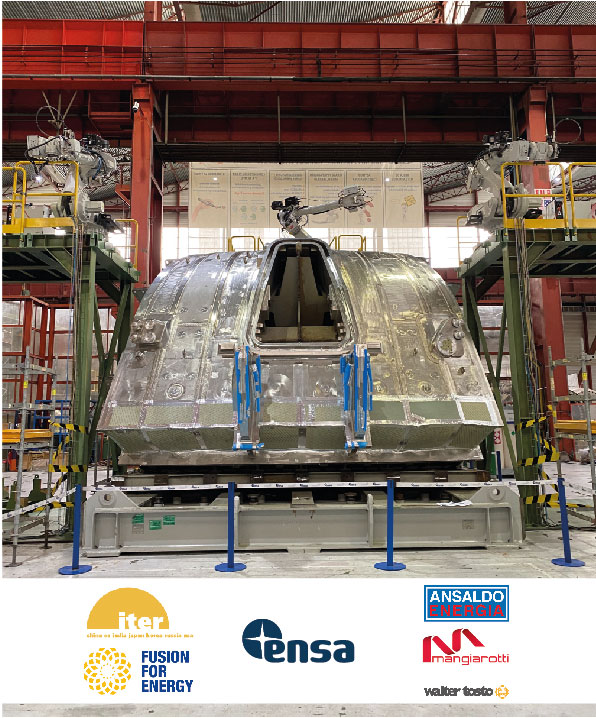
The biggest challenge the team faced was the integration of all necessary equipment to perform works in a seamless manner, and the long 3D welding trajectories of some segments. Furthermore, the size of the components and their complex geometry required the involvement of their most experienced engineers and technicians. According to ENSA, these robots proved to be more reliable, safer for the operators and with better results in terms of the quality of welding.
Beyond the importance of R&D, and the tangible benefits resulting from the use of this technology, this is above all a success story of good collaboration and teamwork between all parties. In spite of the challenging technical specifications, and the multiple levels of co-ordination and management, the team successfully met its goals. F4E in collaboration with the AMW consortium, and in this case ENSA, invested time and human capital in a new welding process with extremely promising results for the future.
To have a look inside the ENSA factory where Europe’s vacuum vessel sectors are welded click here.