ITER magnets celebrate landmark achievement
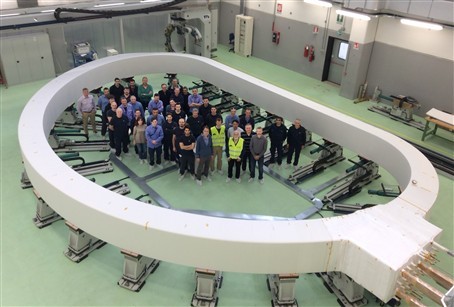

The inner-core of the first ITER magnet has been manufactured. One of the biggest and most complex magnets in mankind is coming to light. This landmark achievement for the ITER project has been supervised by F4E in close collaboration with ITER IO and other ITER parties. The workforces that have been working diligently all these years to accomplish this challenging task have gathered at the ASG premises, Italy, to witness history in the making. More than 600 people have contributed to this milestone from at least 26 companies. Work started in 2008 with the production of the conductor that will be used in the Toroidal Field coils which has reached in total a length of 20 km.
ITER- the biggest fusion device in history will use powerful magnets to confine its super-hot plasma, which is expected to reach 150 million ˚C, so that it refrains from touching the walls of its vessel. This gigantic “D” shaped magnet, known as Toroidal Field (TF) coil, will form part of the 10 out of the 18 TF coils that Europe will manufacture. These will be the biggest Niobium-tin (Nb3Sn) magnets ever produced, which once powered with 68000 A, they will generate a magnetic field that will reach 11.8 Tesla- about one million times stronger the magnetic fields of the Earth.
To create the inner-core of the TF coil, a pack of seven structures have to be impregnated, stacked, electrically jointed, wrapped, and fully electrically insulated. Pipes through which cold liquid helium will circulate inside the magnet to help it reach a superconducting state and instruments to measure its performance have also been added. Each of these packs, known as a winding pack in the ITER jargon, is 14 m high, 9 m wide and 1 m thick. Its weight is approximately 110 tonnes which compares to that of a Boeing 747!
Iberdrola, ASG and Elytt Energy, have all been working together to manufacture the core of this magnet in close collaboration with CNIM and SIMIC, responsible for the production of radial plates which keep the superconductor wrapped inside their grooves and protect it.
For Alessandro Bonito-Oliva, F4E’s Manager for Magnets, and his team, the accomplishment of this milestone is of significant importance. “This is a landmark achievement for the whole project. We have been working really hard to meet the tight planning and manage all interfaces so that all pieces come together at the right time. The very good collaboration between the teams of F4E, ITER International Organization and Japan’s Domestic Agency for ITER has helped us to reach this point and go beyond as production accelerates.”
What are the next steps? After some additional operations are concluded in the ASG facility, the inner-core of the magnet will be transferred to SIMIC to conduct a series of tests. Then, it will be inserted in the massive case of the coil and in the end the final casting process will be performed, during which additional epoxy resin will be injected to fill in any remaining gaps. Next in line is the second TF coil, with manufacturing of the components of its components completed and assembly underway.
To watch how the TF coils are being manufactured click here.
To view images of the different ITER components click here.