ITER Poloidal Field coil enters final phase of production
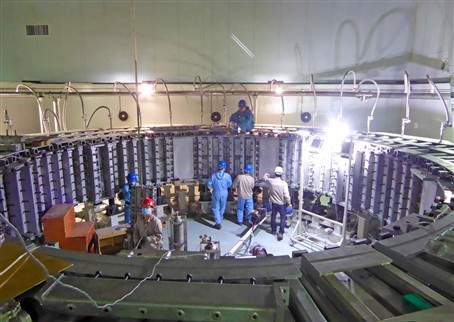
Technicians preparing for Vacuum Pressure Impregnation on PF6, ASIPP, Hefei, China
The teams of F4E and ASIPP (The Institute of Plasma Physics of the Chinese Academy of Sciences) have every reason to be happy with the manufacturing progress of ITER’s sixth Poloidal Field coil (PF6)—they are only a few steps away from the finish line for this magnetic ring which has a 10 m diameter and a total weight of 400 t. The first of the six PF coils which will be part of ITER’s powerful magnetic system is almost ready.
The hard work of 80 people involved throughout the production lifecycle of this component, carried out every day of the week, including weekends, has paid off. Europe partnered with China for the production of PF6 in order to capitalise on the resources and expertise. The result is a win-win for both parties and above all for the ITER project.
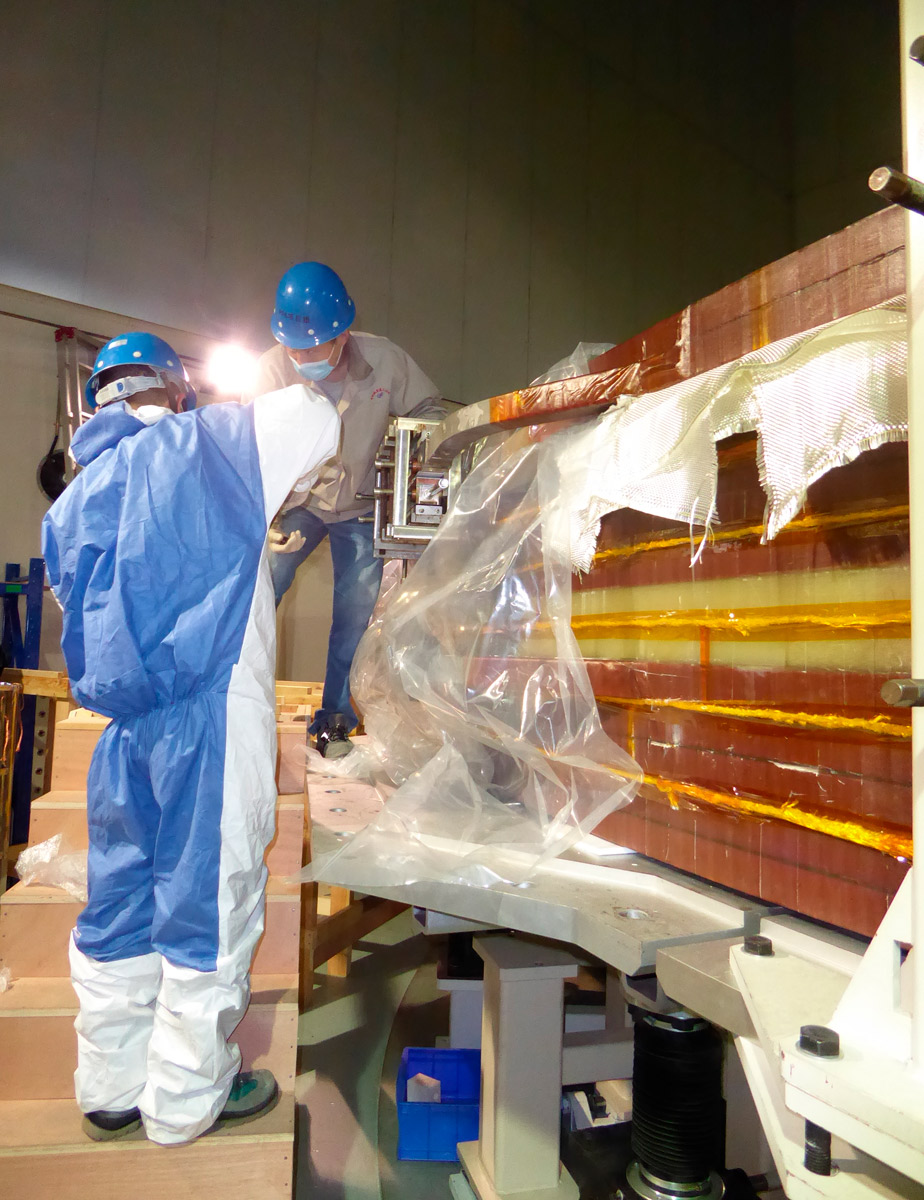
In spite of the fact that we are entering the final phase, there is no sign of the activity slowing down in the workshop. Late last year the workforces managed to complete the stacking of the nine double pancakes (the main pairs of conductor that make the coil) by placing one on top of the other with extreme precision. Early this year the technical teams started working on the ground insulation and the wrapping of the coil. For nearly three weeks during March they were all focused on completing the assembly of the joint supports, and in April they started working on the vacuum pressure impregnation mold paving the way for the next steps to come.
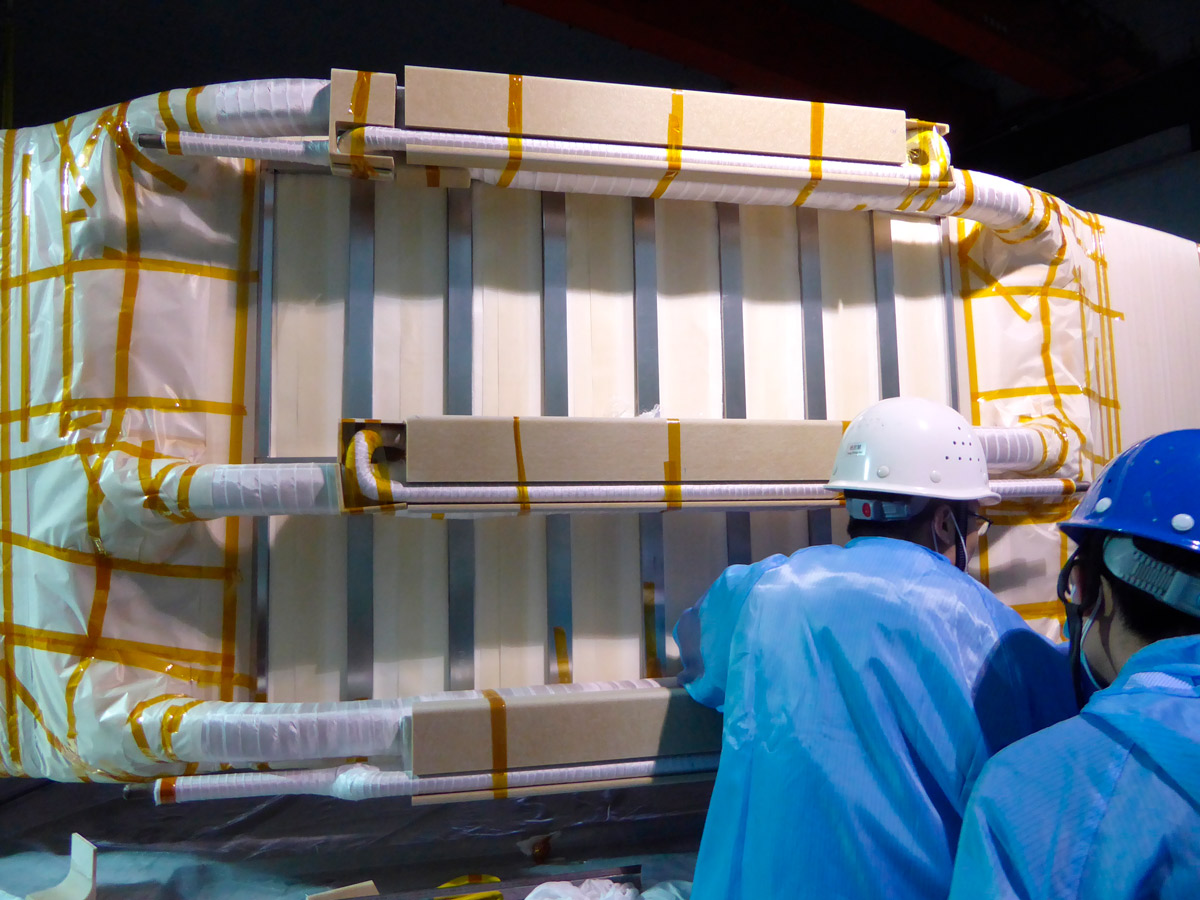
In essence what is left is the impregnation of the entire coil with epoxy resin which is going to last 2-3 weeks after leak testing and drying the component with a heating cycle. Once these last steps are concluded, and after piping and instrumentation will be completed, the coil will be tested and packed to be shipped to ITER. It will be delivered to F4E’s PF coils factory to go through cold testing— being the final acceptance test.
Carlo Sborchia and Peter Readman, working for F4E, have been following closely the fabrication of PF6 from its early days when lengths of conductor were carefully wound to comply with the geometry of the component. “Don’t be fooled by the circular shape of the component,” Carlo explains. “There are several pieces of equipment, such as the 17 joints on the side or the 18 helium inlets, which require special care during the stage of manufacturing and ground insulation. The fact that they are spread all over the component makes things more complicated” he says.
Admittedly, the technicians from Europe and China have come a long way reaching this important technical milestone. Looking back on the learning curve of this exercise Peter singles out a few steps: “the winding of the conductors and the qualification activities proved to be challenging in the beginning …but eventually we found ways addressing them. There was a solid team spirit where trial and error did not matter much in the beginning, because we were all there to get first-hand experience producing the first ITER PF coil. And we are nearly there!” he says.
The finished component will be unveiled at a ceremony, planned on 18 July, and soon after it will cross the sea to make its way to the industrial port of Marseille, where it will be prepared for delivery by a convoy to Cadarache.
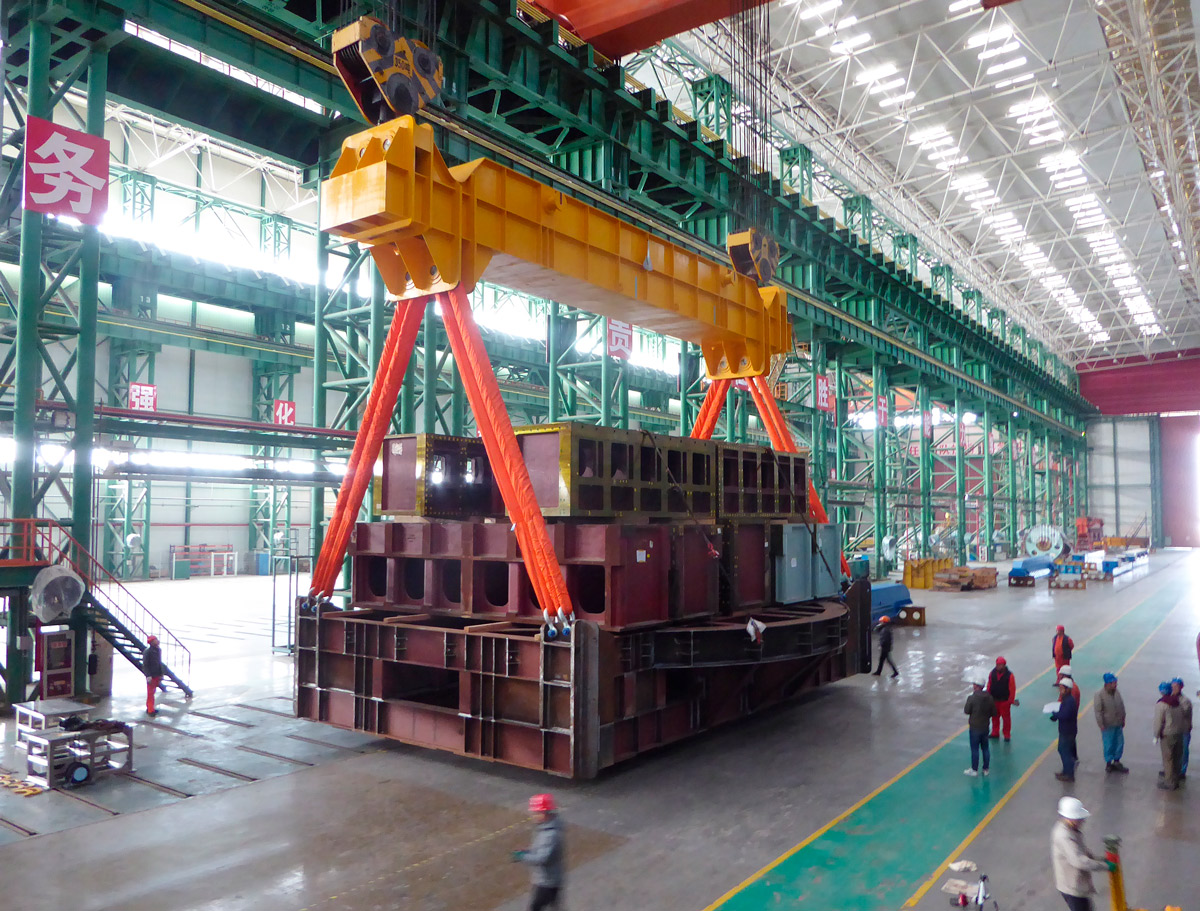