ITER Poloidal Field coils made in Europe
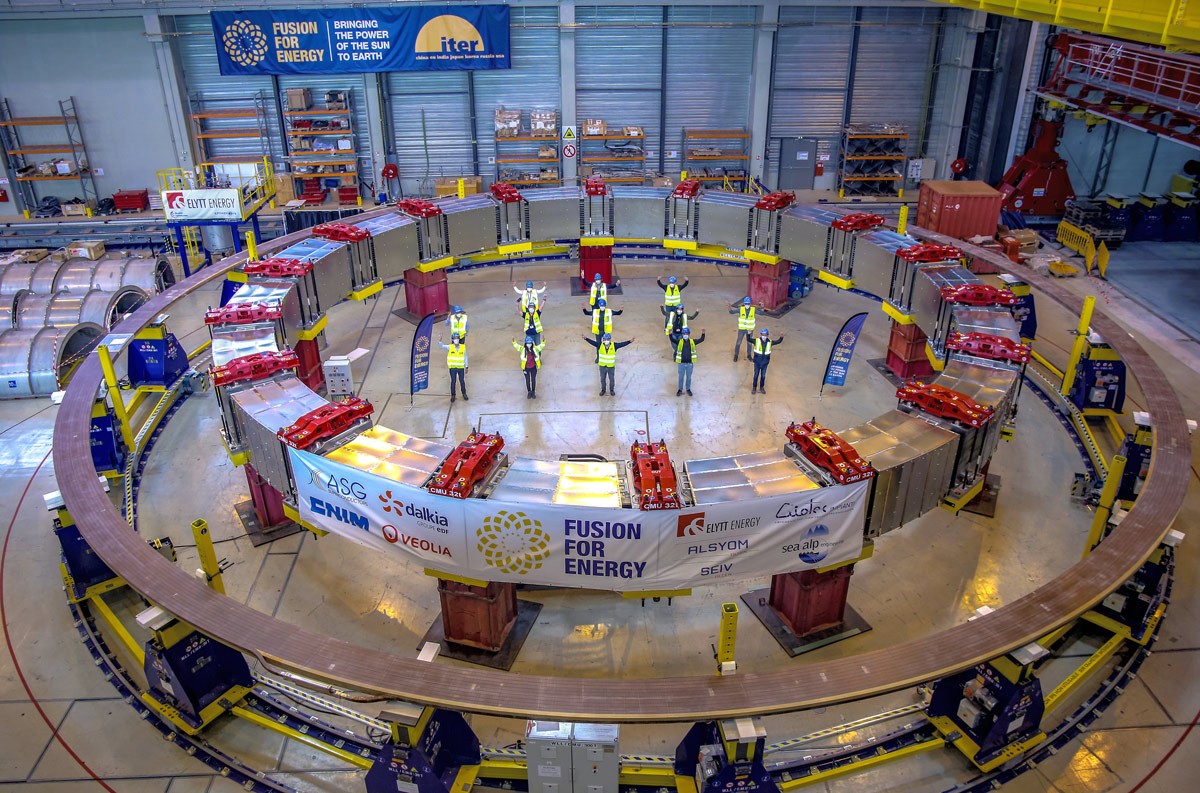
ITER’s fifth Poloidal Field is ready-measuring 17 m in diameter and weighing approximately 330 tonnes. Members of the F4E team standing in the middle of the magnet, PF coils factory, Cadarache, France, April 2021
The bigger ITER Poloidal Field (PF) coils, ranging between 17-24 m in diameter, left F4E with no choice other than to build a factory in order to manufacture the massive superconductive magnets. It is located on the ITER site in order to allow the transport of the largest coil from the production plant to the Tokamak pit, where they will be installed. ITER will rely on six PF coils for the shape and stability of its plasma. Europe is producing five of them, and Russia one.

A 250 m-long facility was erected to become Europe’s production plant in order to house the tooling and the workforces from various companies destined to deliver these massive magnets. The first-ever PF coil entirely made in Europe has been completed and has been handed over to ITER Organization, responsible for the assembly of the components. It’s an important milestone for those involved in its production during the last years because it results from the expertise of at least 12 companies and more than 150 people.
“ITER has always set the benchmark high in terms of engineering, and today’s result demonstrates that Europe can make it. We have the technical skills, the know-how and the capacity to produce such magnets. The first fully EU-manufactured poloidal field coil (PF5)—being the fifth of the six—may not be the biggest given the fact two will follow with a diameter of 24 m. But this one has been our learning curve for the ones to come. We learned a lot, improved and developed techniques to overcome any technical difficulties along the way. F4E supervised the entire production from the start, and with the valuable contribution of our contractors we delivered our first made in Europe,” explains Alessandro Bonito-Oliva, F4E Magnets Programme Manager. A few months ago, PF6, a coil manufactured jointly by Europe and China left from the PF coils factory having gone through successfully its cold tests. Incidentally, as PF5 gets delivered, PF6 will be moved in the Tokamak pit. It’s a double milestone for the ITER project.

The main production steps of PF5 can be simplified in the following order: winding and wrapping of the electric insulation of the conductor to produce flat spiral coils (known as double pancakes); stacking and electrical connection of the eight double pancakes to form one winding pack; impregnation with epoxy resin; electrical checks, cold tests, final checks.
Those who want to know more about some of the details we have some key figures. The total diameter of the coil is 17 m and weighs 330 tonnes. The length of conductor is roughly 11.5 km and the amount of resin contained is approximately 2400 litres. The cold tests that the PF coil needs to go through are extremely delicate and take place towards the end of the manufacturing process. What do they entail? The component goes into a cryostat at room temperature, where it is cooled down to -188 °C (85 K) during 15 days so that engineers perform the necessary tests. Once these are over, the component goes back to room temperature to carry out the final acceptance tests. This process is performed twice to make sure the component withstands the low temperature with no technical issues.

Setting of the facility with the help of Dalkia–Veolia has been fundamental in providing the infrastructure of the PF coils factory. The production of tooling and manufacturing has been possible thanks to the involvement of various European companies such as Sea Alp, ASG Superconductors, CNIM, Elytt, Alsyom/Seiv, Criotec Impianti. Mammoet and Bureau Veritas have been involved in the production of cranes and their annual regulatory controls.
The operation of the factory on-site has given an industrial edge to the ITER project, complementing the already well-known construction works of the experiment. But, it has also given a human angle to the components we produce. Because under the roof of this production plant, where Europe is manufacturing its PF coils, people have demonstrated that they can convert designs into tools, apply fabrication techniques to production; solve complex technical issues as they arise; respond to health and safety challenges posed by a pandemic which was unforeseen; honouring the spirit of international collaboration to deliver. And in spite of all these challenges, they succeeded working as one team! Meet some of the F4E staff involved in the production of the PF coils and read about their contribution by clicking here.