ITER Test Blanket System passes Conceptual Design Review
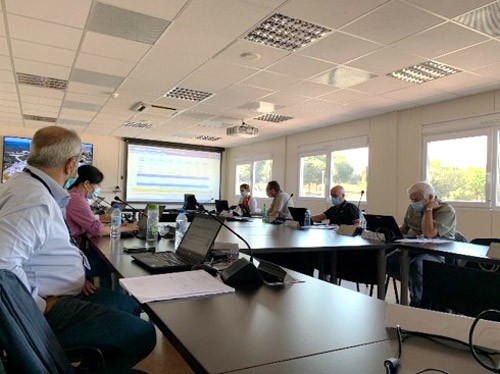
Experts during the Conceptual Design Review meeting assessing the quality of the design of the Water-Cooled Lithium-Lead Test Blanket System to be used in the ITER device. Cadarache, September 2020.
ITER will use two different types of “fuel” to release energy: deuterium and tritium. In addition, helium and neutrons will result from the reaction. While deuterium is abundant in seawater, tritium is much scarcer. Breeding blankets will play an important role in future to generate the supply of tritium in fusion machines. How? The component contains lithium, which after its interaction with the neutrons produced in the reaction, it will breed tritium. Moreover, the breeding blanket will turn the fusion power into thermal power, which afterwards may be used to generate electricity.
F4E is working closely with ITER Organization (IO), seven European fusion labs belonging to EUROfusion and nine engineering companies and universities to produce a Water-Cooled Lithium-Lead Test Blanket System (WCLL-TBS). Although ITER will not be connected to the grid, it will demonstrate that fusion is feasible at a bigger scale compared to smaller fusion experiments, and it will serve as a test environment for the breeding blankets in order to draw lessons for DEMO, the fusion machine to follow ITER. The Test Blanket System consists of different sub-systems deployed in the Tokamak building. One of these sub-systems is the Test Blanket Module, which will be placed in a vacuum vessel port. Its structure will be made of EUROFER97, a new martensitic steel, more suitable for neutrons than austenitic steels, making it less radioactive and shortening the lifespan of nuclear waste. Other sub-systems are the Water-Coolant System or the Tritium Removal System. The technical complexity of the whole Test Blanket System is such that it took nearly two years to develop its Conceptual Design Review (CDR).
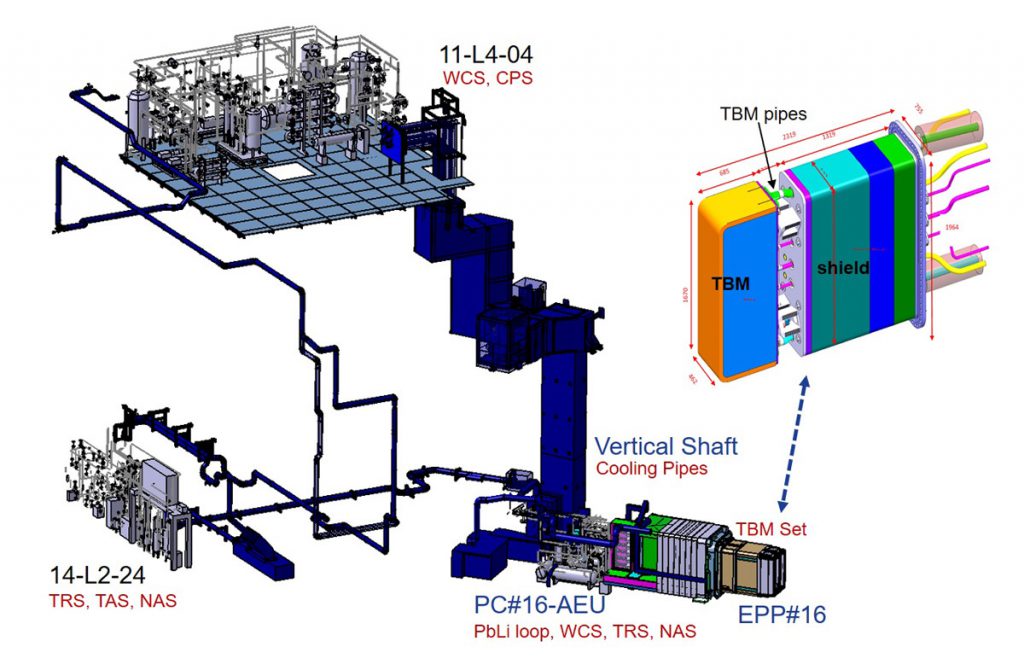
The CDR meeting took place 16-18 September 2020 in the premises of IO, Cadarache, with 11 people on-site and up to 92 remote attendees. A panel of 19 experts from IO and other entities acknowledged that the level of detail of the technical documentation presented exceeded by far what is expected of a CDR. No wonder, as more than 3 000 pages of documentation were submitted. The conclusion was therefore clear: the design is mature enough to go forward to the next stage.
“The acknowledgement we have received gives even more motivation to the team to continue with a high level of commitment. It enhances our credibility to our stakeholders and paves the way for the next step,” states Italo Ricapito, F4E Project Manager and Chief Engineer of the European TBM Programme.
As for Marco Ferrari, European TBM Deputy Programme Manager, he underlines the complex but successful collaboration with all involved parties: “It has been the first time that this type of European TBM Programme organisation, resulting from an F4E-EUROfusion collaboration, has been put in place and it has been successfully implemented and executed. It has marked the way forward for the finalisation of the WCLL-TBS design cycle.”
After this achievement, the team will have to focus on different areas such as design and analyses, safety studies, fabrication, etc. The Preliminary Design Review is scheduled for November 2022. We will have to wait until the end of 2025 for a Final Design Review, which will enable us to start manufacturing the WCLL-TBS.