Last case for ITER Toroidal Field coils delivered to F4E
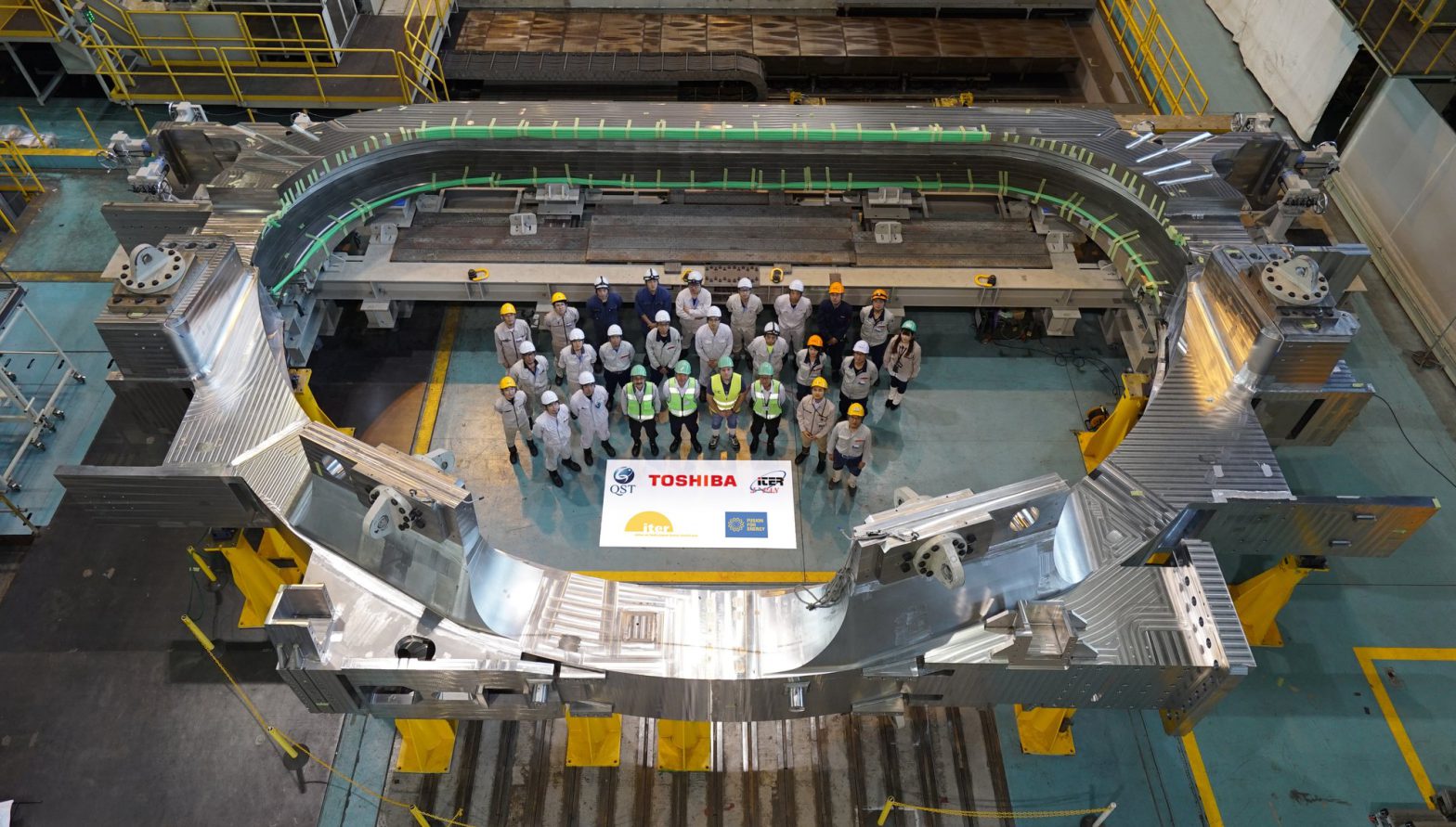
Completion of the fifth (middle) Toroidal Field coil case for Europe, manufactured by Toshiba in collaboration with QST, Japan. © QST
The super-hot plasma of the ITER device will be confined with the help of 18 superconducting magnets, known as Toroidal Field coils. They will create a “cage” to keep the hot gas floating without touching the walls of the vessel that will house the fusion reaction. Europe is responsible for the production of ten of them and Japan for the remaining eight, plus one spare. A stainless-steel case will enclose the inner core of the magnets to protect them, while they sustain extremely high electro-magnetic forces during operation.Each case consists of four parts: two U-shaped and two closing plates. The longest measures 17 m and the widest approximately 6 m. It’s a bulky panoply which will take welders roughly four months to dress with this layer, the 14 m magnet.

Japan’s ITER Domestic Agency, QST, has been responsible for their fabrication. The last of the ten coil cases was delivered in February 2022 to the factory of SIMIC, Italy, where the final production steps of Europe’s TF coil are unfolding.
The completion and delivery of the final coil case marks the end of a successful collaboration between F4E, QST, and ITER Organization, which started 14 years ago. To celebrate this technical milestone, a virtual event was organised bringing together representatives from the different parties involved to look back on this journey. Collaboration, determination, and the importance of human dynamics were highlighted in all interventions.
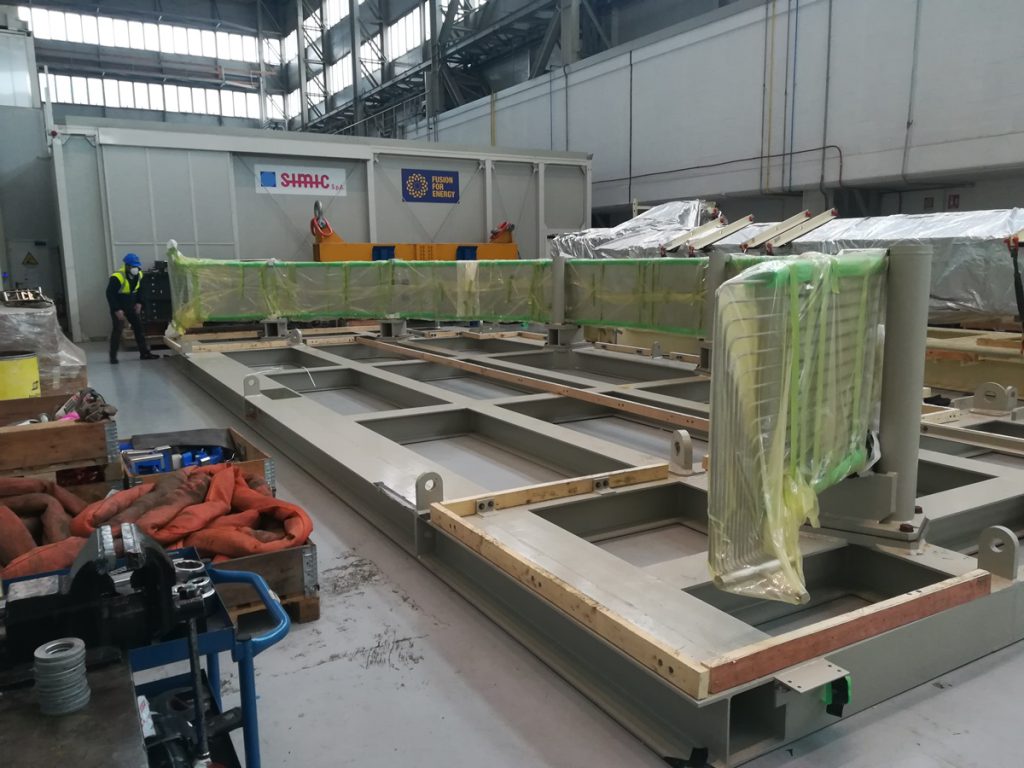
Alessandro Bonito-Oliva, F4E Magnets Programme Manager, recalls the early days when several factors had to be weighed. “We needed to get the technical specifications right regarding the tolerances of the coil cases; the logistics so that they arrive safe and according to schedule, and last but not least, evaluate the financial impact of these operations. The pressure to get things right from the start was enormous but afterwards, we were able to put in motion a process which worked till the end. Good communication together with a problem-solving approach from all parties, were essential in achieving this milestone.”
Masataka Nakahira, ITER Japan, Group Leader for TF coils, had to face first hand several of the technical challenges, given the fact that his organisation was responsible for the production of the coil cases. “First, we needed to explain to industry what we were after and convince them that it doable. Second, we dedicated time in getting the design right and validating all production steps to meet the high tolerances of these components. Once the first case successfully passed all acceptance tests, we knew we were on the right track for the ones to follow.”
When delivered in Europe, the technical team of F4E took the lead to check the equipment and apply with SIMIC the necessary welding techniques. Boris Bellesia, F4E Magnets Deputy Programme Manager, looks back on the arrival of the first coil case in 2018. “After concluding rounds of meetings discussing costs and fabrication, I remember how eager we were to receive the first coil case in 2018. All other parts of our TF coils were produced in Europe except this one and naturally, we were curious. Throughout this process we worked as one team reporting on checks, metrology assessments, and exchanging information with our counterparts in Japan who were also welding the cases to their coils.”
F4E is getting ready to send its seventh coil to ITER. And as for the welding operations of the last European coil, they are expected to be completed by the second half of 2022.