Massive ITER magnets in full production
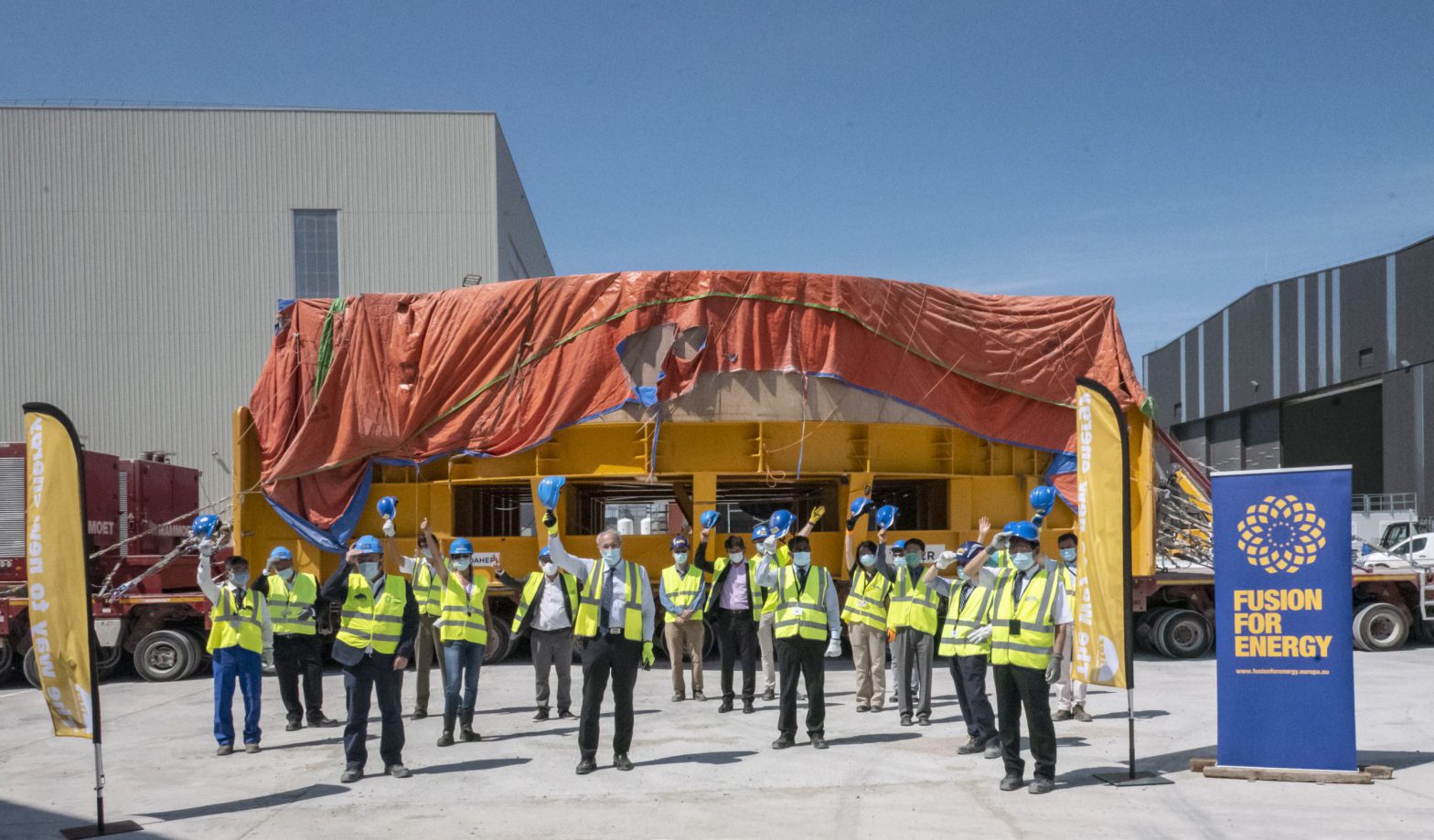
Representatives of F4E, ITER Organization welcoming the sixth Poloidal Field coil on-site, ITER site, Cadarache, June 2020.
Six powerful superconducting magnets will tame from top to bottom ITER’s powerful super-hot plasma ensuring its shape and stability. Their diameter varies between 8-24 m and their weight ranges from 200-400 t. Most of them are too big to be transported by a convoy. Due to their gigantic size, four of the six Poloidal Field (PF) coils are manufactured in a factory set up by Europe on the ITER site. F4E is not only procuring five of the six coils. It is also managing the factory and the contractors contributing to their fabrication. Sea Alp, Criotec, Elytt, Alsyom and SEIV have supplied the tooling; ASG Superconductors has been acting as engineering integrator and with CNIM, the two companies have been entrusted with manufacturing.
The sixth of the coils is PF6. It is the smallest of all and the first to be inserted in the ITER machine. It has been produced through an agreement between F4E and ASIPP, the Institute of Plasma Physics of the Chinese Academy of Sciences. Its delivery on-site marked an important milestone because it is the first PF coil to be completed and the first to undergo a cold test. The arrival of the coil was celebrated on 26 June with a small ceremony bringing together delegates from Europe, China and ITER Organization. Johannes Schwemmer, F4E Director, praised the truly collaborative spirit between Europe and China in delivering this one-of-a-kind component. The role of Jean Marc-Filhol, F4E Head of ITER Programme Department, was highlighted for having successfully sealed the agreement between Europe and China ensuring the timely delivery of PF6, and for overseeing F4E’s substantial financial contribution in the range of 500 000 EUR for the additional works of the ITER itinerary.
PF6 will now go through inspections, dimensional checks and cold tests which are expected to last approximately two months. Alessandro Bonito-Oliva, F4E Magnets Programme Manager, spent long time in China to oversee the final phase of manufacturing during which some unexpected quality issues had to be solved. “My collaboration with colleagues from ASIPP can be described as inspirational and motivational. It will always stay in my heart and mind. We had a little amount of time to fix technical issues which were hard to identify but we managed to do so successfully working as one team. We were strongly motivated, didn’t lose faith in our capability to resolve them even in the most difficult moments and managed to address them together in record time” he explains.
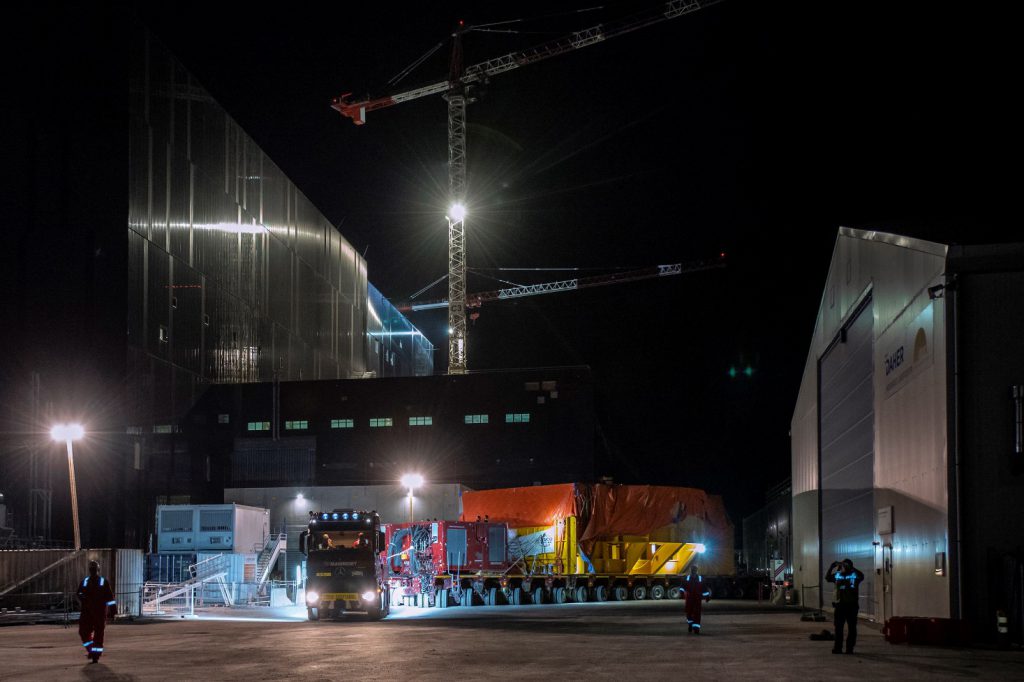
The arrival of PF6 generated a tremendous feeling of enthusiasm to those following closely the ITER project. In practical terms, however, it triggered off a series of changes in the layout of the F4E factory. Tooling stations had to be reconfigured, equipment had to be moved temporarily to make room for PF6, technicians prepared the cryostat to perform the first cold tests. The spotlight is now officially on the PF coils. What is the state of production with the rest of coils manufactured by Europe?
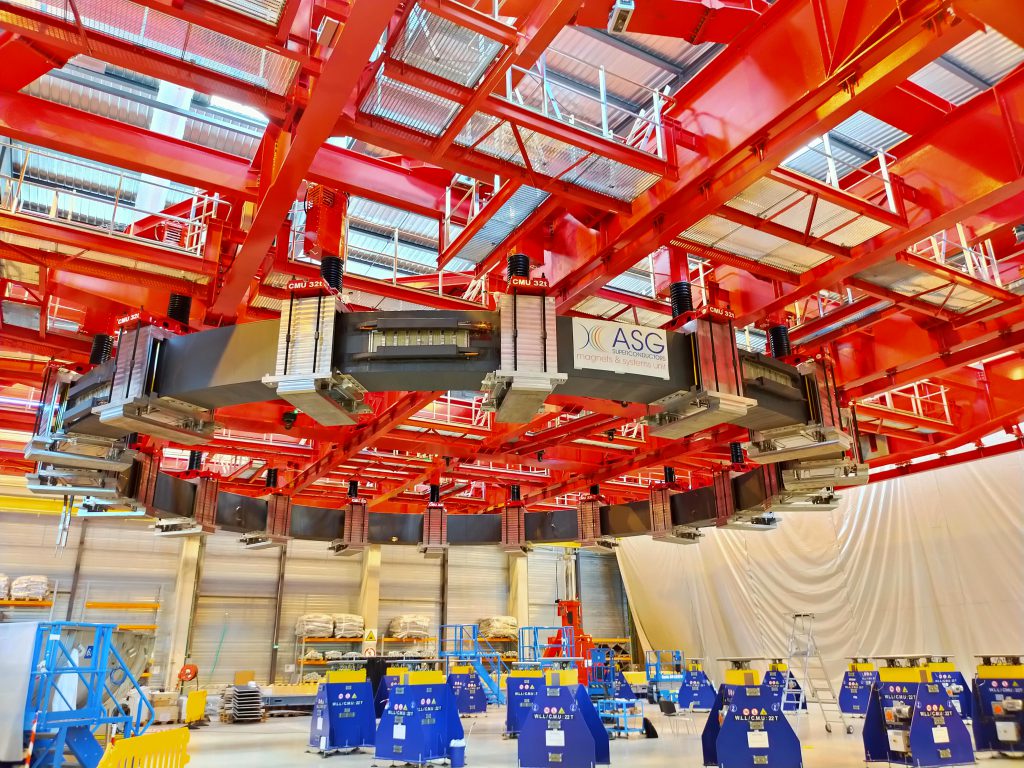
“We are now in the final assembly phase of the fifth Poloidal Field coil,” explains Thierry Boutboul, F4E Magnets Project Manager. “We have completed its impregnation, painting, performed dimensional checks, assembled protective plates and have positioned 18 clamps around it. The coils have been moved to the stacking station and we will proceed with instrumentation checks,” he explains. “What is remarkably different in the production of these magnets is our responsibility as factory owners. We have the supervision of Health & Safety and that of contractual co-ordination between all companies involved.”
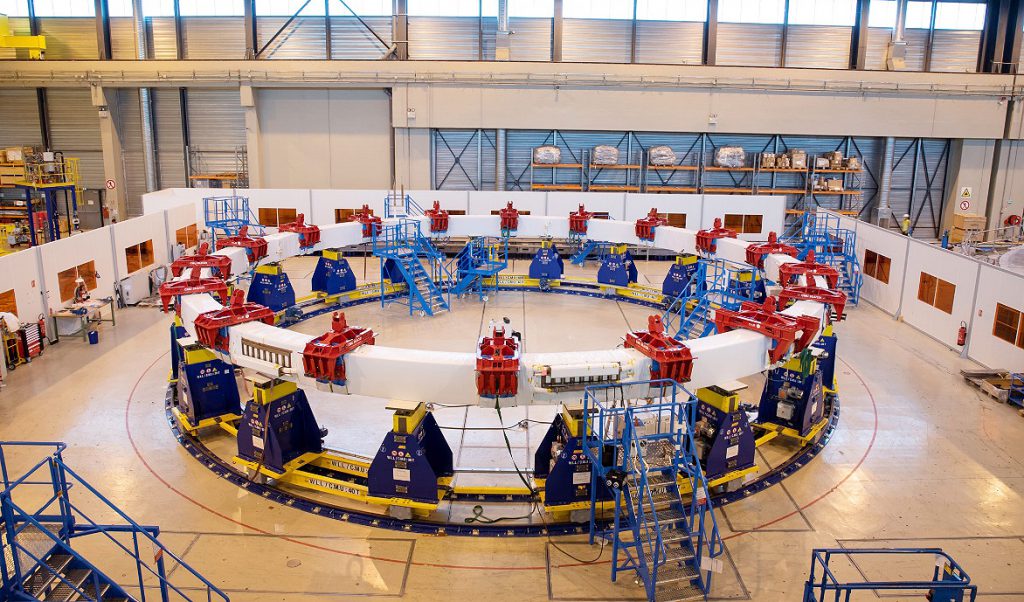
Meanwhile, PF2 has gone through ground insulation and will go through impregnation which is expected to last approximately three months. Last but not least, the teams are getting ready for the production of the biggest of all coils—PF4 which will have a diameter of 24 m. The winding station, where the conductor will be wound, has been reconfigured and the tests with a dummy conductor have already begun.
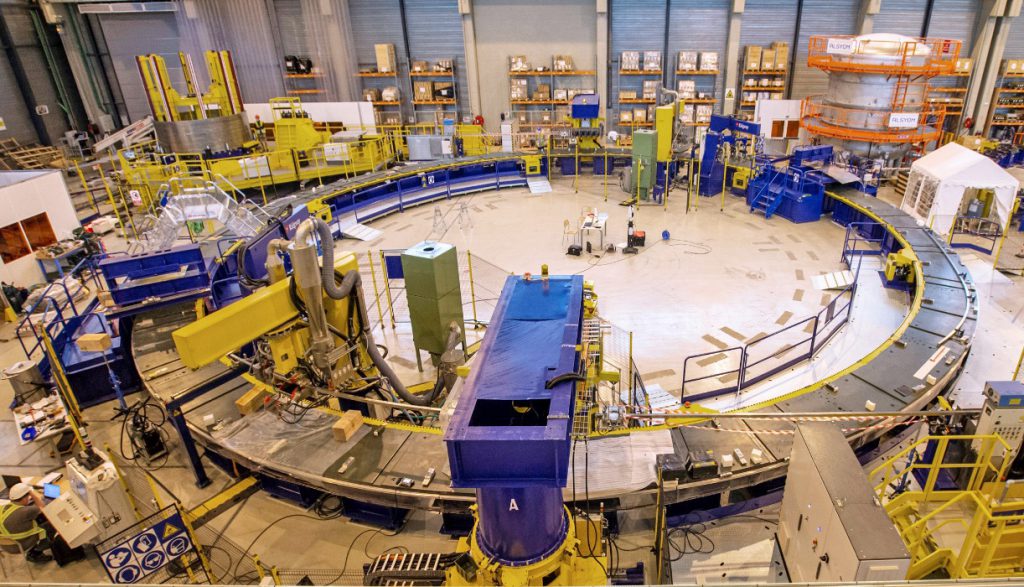
A further extension of the PF coils factory, measuring more than 1300 m2, is currently under construction in order to allow the installation of the de-moulding station for the 24 m-diameter double pancakes- the inner layers of the coil.
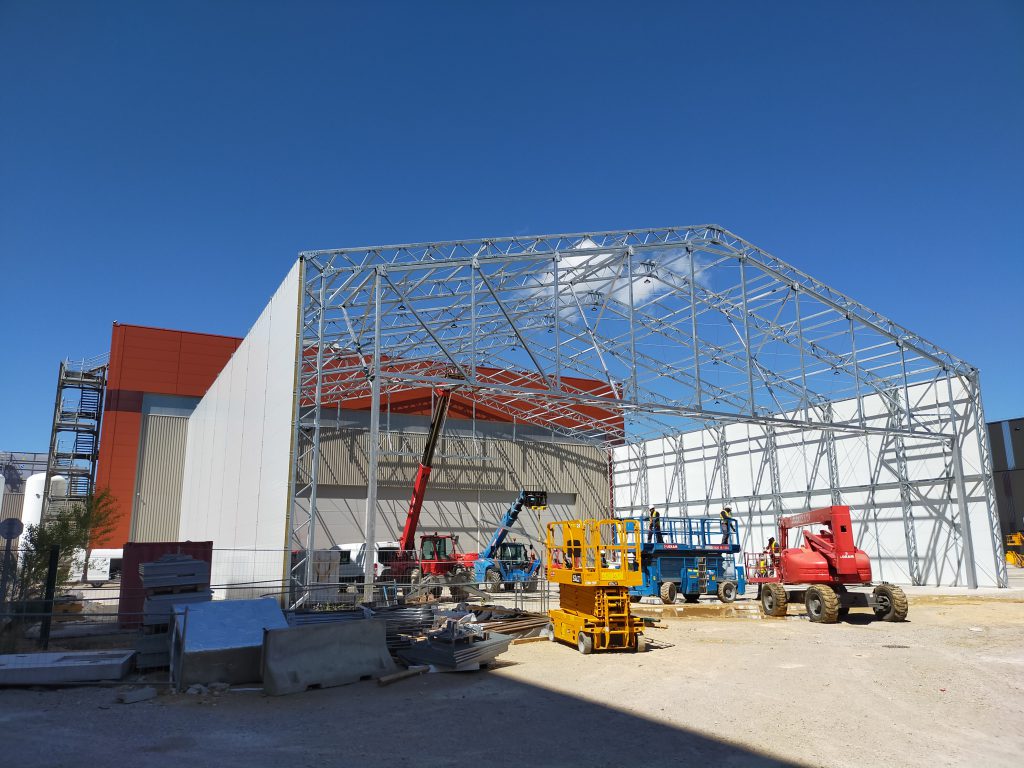
In spite of the COVID-19 outbreak, F4E took specific measures to maintain the pace of production by putting in place new health and safety regulations. Pierre Gavouyere-Lasserre, F4E Magnets Project Manager, has been heavily involved in the implementation of these measures. “First, we had to assess which tasks could still be performed during this exceptional period and how. Second, we reconfigured the activities making sure that no time was wasted. For example, we used this window of opportunity to test equipment, while performing heavy lifting activities with the cranes. More recently, we have developed and implemented a comprehensive post-confinement Health and Safety framework to ensure the safe acceleration of all activities. A complete set of measures has been specifically designed, such as a system of rotation, one-way circulation in the building, contactless temperature measurement at the entrance, and the reinforcement of the cleaning activities” he explains.
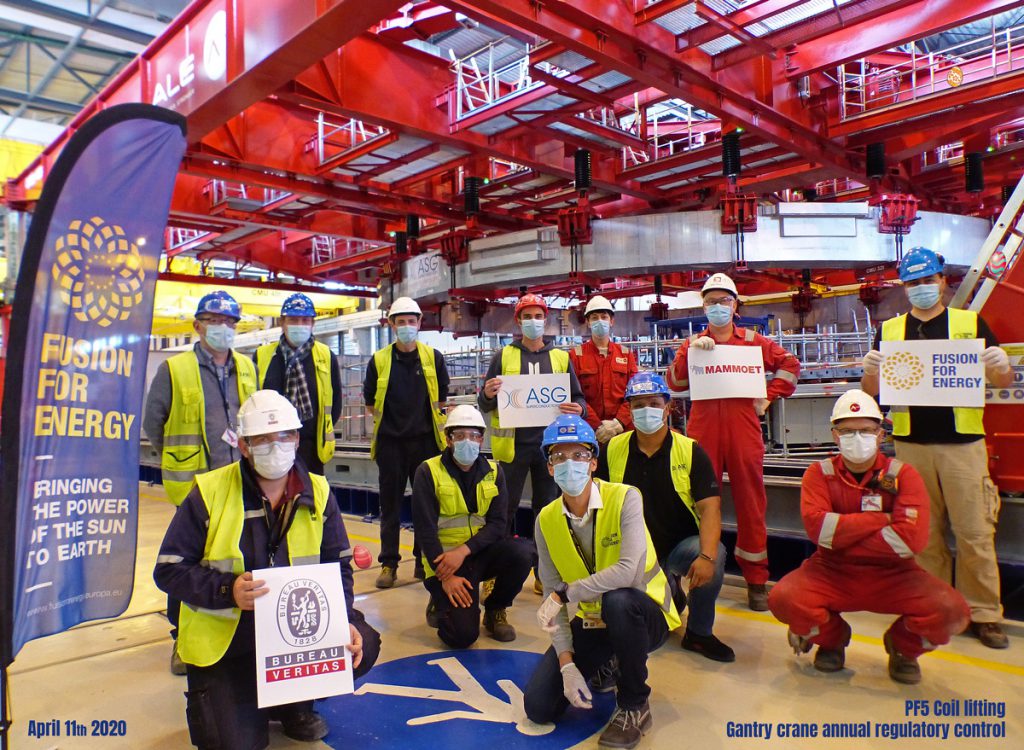
The arrival of PF6 and the progress of the remaining coils on-site have managed to pull the various teams of contractors closer together, reinforced a common vision for the project and gave them a sense of pride by being partners in the fabrication of some of the largest magnets ever made.