Mastering the manufacturing of ITER Poloidal Field coils
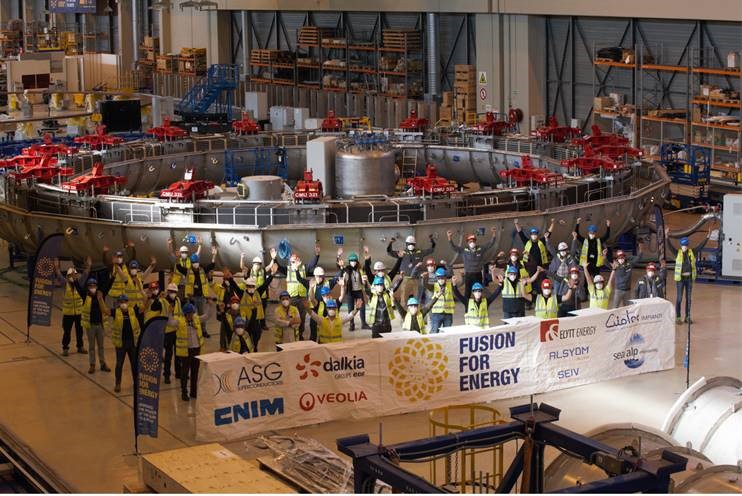
The successful conclusion of the ITER Poloidal Field coil 2 cryotests. Members of staff from F4E, ASG Superconductors, Dalkia, CNIM celebrating the technical achievement, Poloidal Field coils factory, Cadarache, France.
With two Poloidal Field coils (PF5 and PF6) already delivered, F4E and its industrial partners are working full speed to manufacture the remaining three coils under Europe’s responsibility. These magnets are much bigger in size, ranging from 17 to 24 m in diameter, occupying all stations in the factory set up by Europe on the ITER site. There is an upbeat tempo in the atmosphere as teams perform their tasks round the clock with incredible precision. From the mezzanine of the factory, you can feel the speed, the adrenaline and the stress to meet the tight schedule. But, you can also sense a professional and well-composed manner in executing those delicate technical operations stemming from the experience gained.
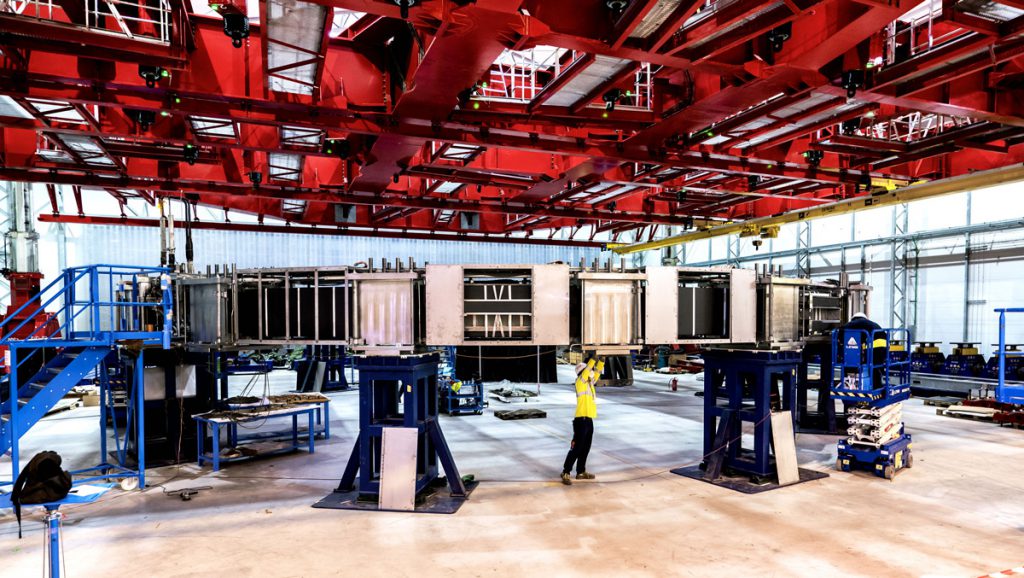
The ITER device will operate with six PF coils, having as their main objective to ensure the shape and stability of the super-hot plasma. PF 2, measuring roughly 17 m, is the next magnet in line to exit the factory in order to join the queue for assembly when its time comes. Weeks ago, the thermal cycle tests to 80 K were completed, as well as all Paschen and High Voltage tests. Now the coil is ready to be handed over to ITER Organization towards the end of December. “The completion of our third coil is an important milestone for all members of the team and the companies we work with. We have approximately 100 people in two shifts ensuring a smooth flow of operations. They have gained a lot of experience with the tooling, the processes in place, and have demonstrated a lot of resilience during those difficult times we had to cope with the pandemic,” explains Pedro Carvas, F4E Technical Officer.
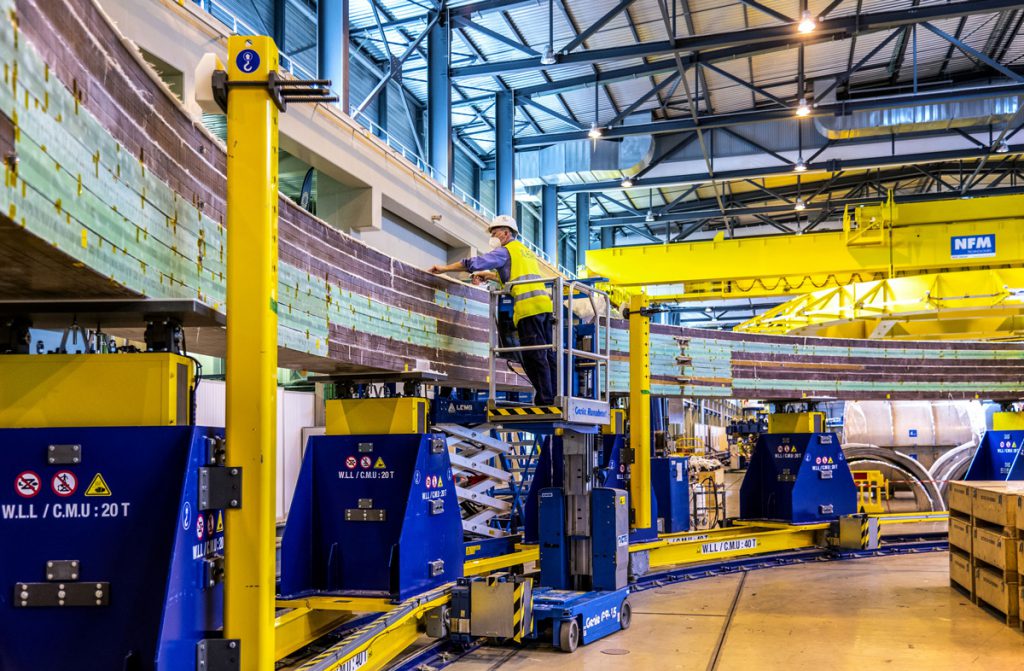
In parallel, the fabrication of PF4 is also progressing in various stages. All eight double pancakes, the layers of conductor inside the magnet, have been stacked and jointed in order to go through assembly. In essence, the technicians will have to insulate and impregnate eight double pancakes to form a winding pack—the core structure of the coil. The diameter of this coil is in the range of 24 m, much bigger than the previous ones. Consequently, an impregnation station is under preparation to correspond to its size. Daniel Rossi, F4E Production Manager, welcomes us at the mezzanine to explain some of the main challenges. “There is never a quiet moment in this facility. One coil may be on its way out but two more are shaping up. We will need to reconfigure the impregnation station and cryostat to perform the works for PF4 and PF3 without affecting the flow of all other operations. We need to use space wisely and in line with the production process. Our main challenge is to re-arrange our tooling and allocate our resources in an efficient manner in order to deliver this coil towards the end of the year.”
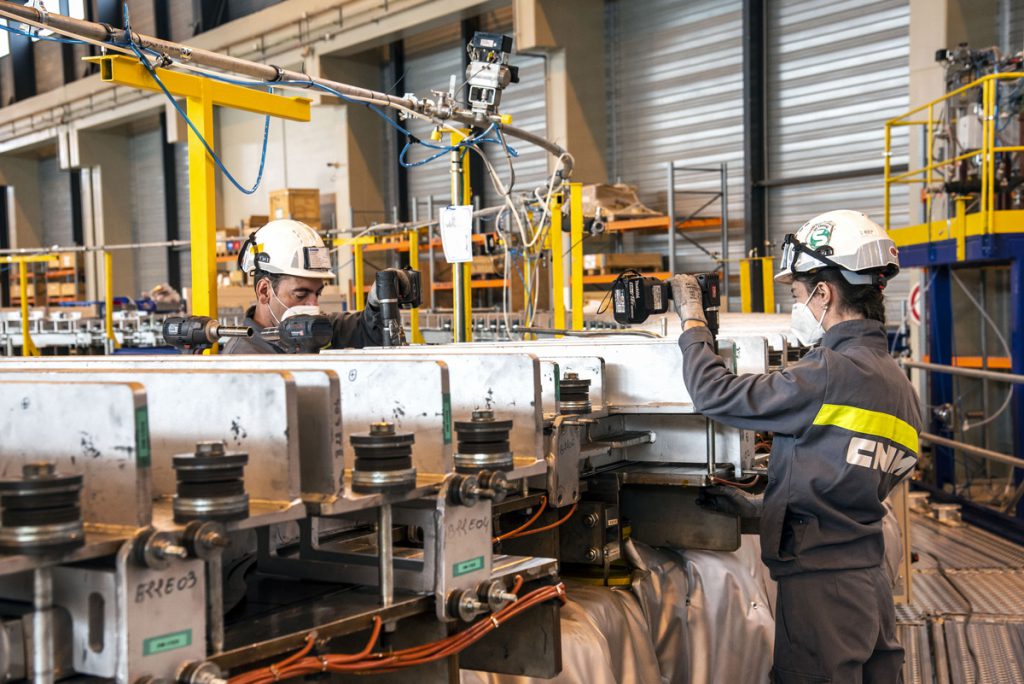
What is the magic formula, beyond technical expertise, that helped Europe’s PF coils team to master the process of manufacturing? Romano Gennaro, Technical Officer dealing with contractual aspects, elaborates on the human capital behind this success. “We have gone through an extremely useful learning curve. It helped us to build team dynamics, understand our strengths, weaknesses and build on a common project. When the final design of the components was agreed, the pieces started coming together. We could decide much better on the tooling, its maintenance, and in parallel, cut down any unnecessary activities, which proved, lengthy and costly. The activity you see in the factory results from an incredible team effort made by F4E and its suppliers. The people next to the machines and those who negotiate and mediate.”
Alessandro Bonito-Oliva, F4E Magnets Programme Manager, sees the race to complete the three magnets as the final sprint before reaching the finish line. “The trajectory of this project, from an initially difficult start to our present optimised organisation, has been incredible. We now run a factory with several suppliers working together where there is great team spirit and excellent coordination provided by the F4E. I am proud of our technical achievement, manufacturing among the largest-ever superconducting magnets, and also of our collaborative spirit which has been the secret of our success.”