One of the largest superconducting magnets completed and delivered.
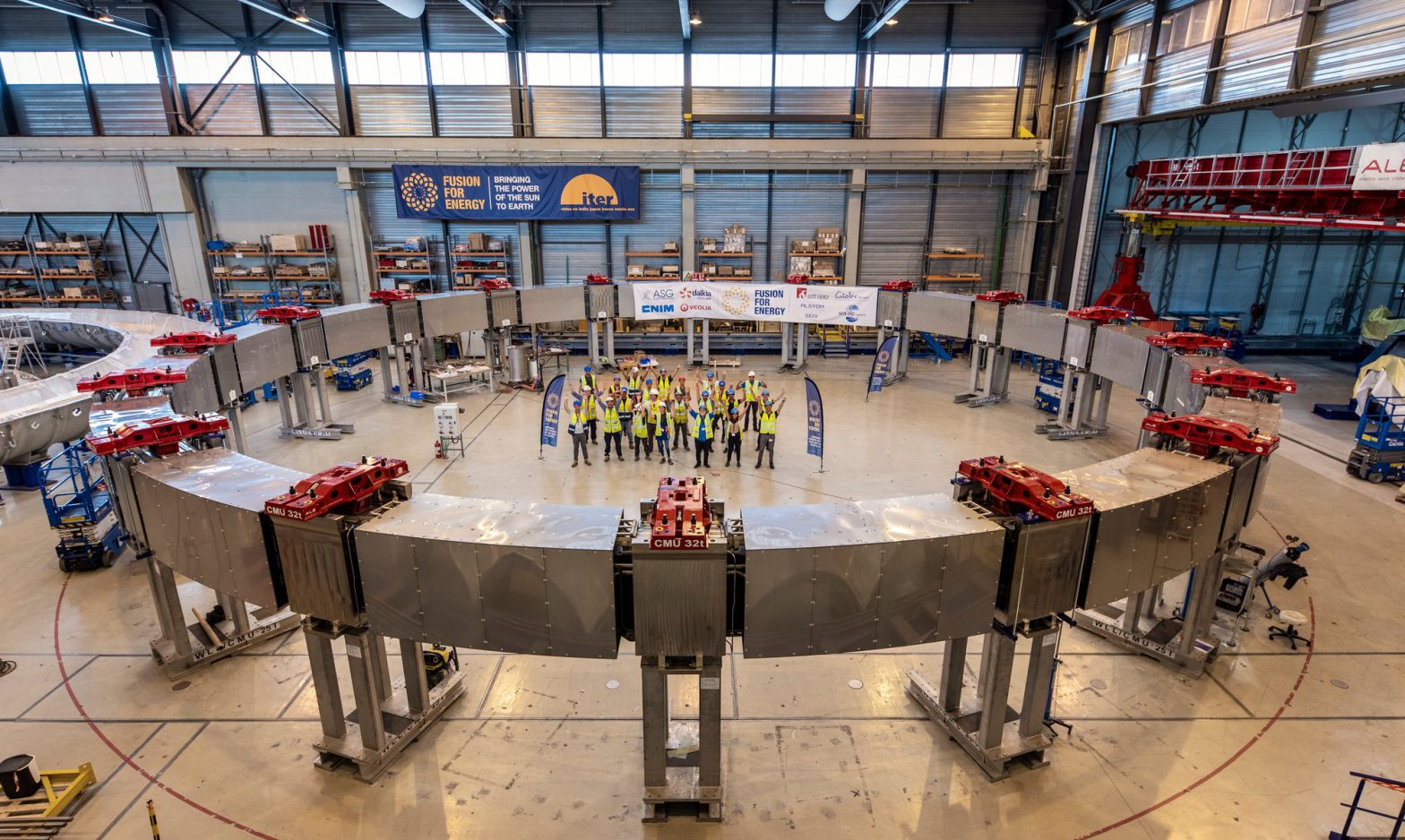
Representatives of F4E, ASG, ISQ, Dalkia, Veolia, Onet standing in the middle of Poloidal Field coil 4, manufactured by Europe in the PF coils factory, Cadarache, July 2023. ©F4E
Various fusion projects are competing to deliver the energy of the Sun to Earth. ITER, the largest international collaboration in this field, aims doing that with the help of powerful superconductive magnets and a vast range of new technologies. Six of these magnets, known as Poloidal Field (PF) coils, will control the shape and stability of the burning plasma. These massive rings will embrace the machine from top to bottom to create a powerful magnetic field. They vary in size and that proved decisive for their production. Two of the smaller coils were fabricated off-site, because it was possible to transport them by sea, and subsequently, on the highway from the industrial port of Marseille to Cadarache. In fact, one of the smaller coils (PF6) resulted from the collaboration between Europe and China, produced in Hefei (China), while the other one was fabricated in Russia. But just to give you an impression of what we mean by smaller coils, the one manufactured in China in collaboration with Europe, weighs 400 tonnes and is 10.3 m in diameter.
Due to the massive dimensions of the remaining four coils, Europe had to build a factory on the ITER site to manufacture them and perform all relevant tests. The facility, opposite the Assembly Hall of the Tokamak Complex, which is 300 m long, houses all the tooling and infrastructure to produce magnets that range from 17-24 m in diameter. We are talking about are massive, heavy, and complex components that over the years have involved on-site up to 100 people and at least 10 companies from Europe. To name few: Sea Alp, , Elytt Energy, Alsymex and Criotec and have supplied the tooling and the cold test facility respectively; ASG Superconductors has been acting as the engineering integrator and together with CNIM, the two companies have been entrusted with manufacturing.
Every time a magnet is produced, and tested at roughly -200 °C, it is handed over to ITER Organization, which has the responsibility to receive all components and assemble them. So far, F4E has delivered three PF coils (PF6, PF2 and PF5). By no means an easy feat but nevertheless, nothing compared to the two 24 m in diameter magnet beasts, left to be produced. The expertise accumulated proved valuable for the fabrication of the last two, which qualify as some of the biggest superconductive coils ever produced. According to Enrico Vizio, F4E Project Manager, who has been monitoring closely the pace of production, it took Europe approximately 25% less time to produce PF4, compared to PF5, in spite of its larger size.
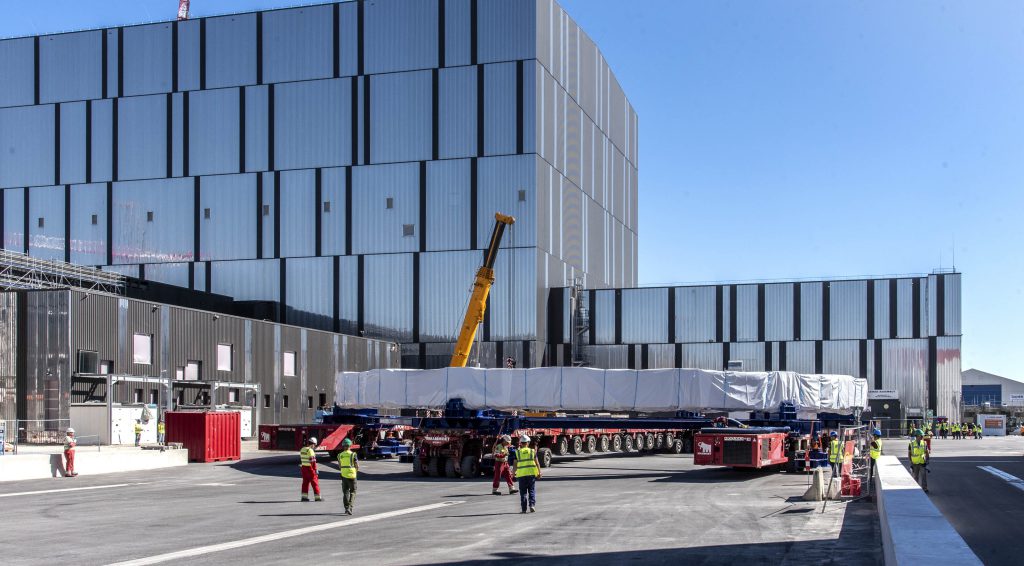
Early in August, PF 4 left the F4E PF coils factory to join the rest of the coils that have been delivered. The magnet, whose 250 m2 surface was tightly wrapped, was driven to a storage facility. It took roughly three years to complete its production, with engineers working on two magnets in parallel. During the pandemic, engineers had to comply with tight restrictions on social distancing, and enhanced health and safety guidelines which complicated their original routine.
Alessandro Bonito Oliva, F4E Magnets Programme Manager, highlights several important facets which added more complexity to the manufacturing of these components. “Managing the production of the PF coils, through six industrial contracts, and more than 10 suppliers gives you a good impression of the structured work we did and the multiple interfaces we had to deal with. Working simultaneously on different aspects and phases of the production has been a challenging task. We had to foster a collaborative culture with other partners, making the best use of their skills to produce these one-of-a-kind magnets.”
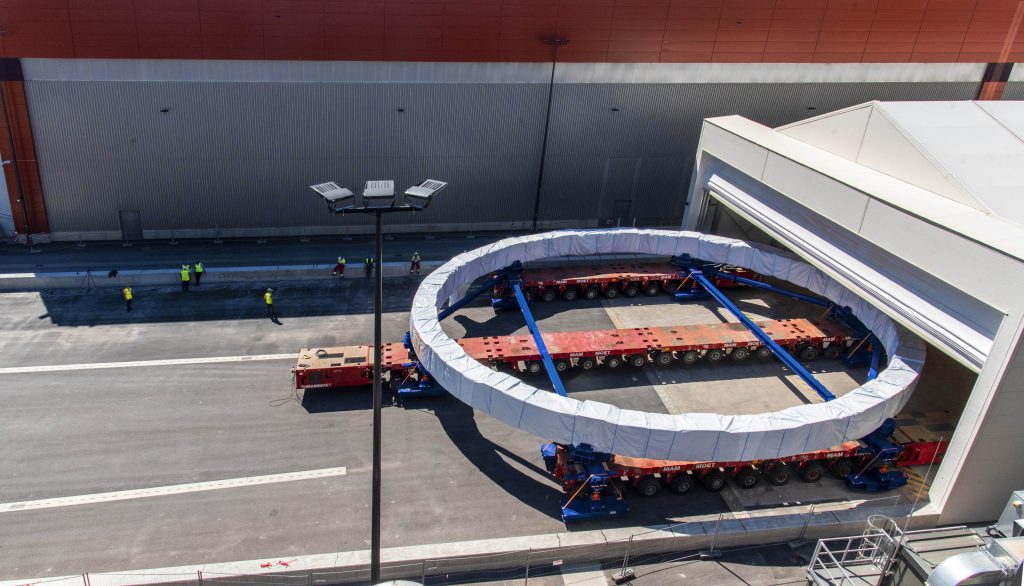
“Many factors have contributed to the successful production of this magnet. If I had to single out one, it would be teamwork. We need to understand the particularity of this context. F4E was not only procuring the magnets, but it was also deeply involved in managing their production in a factory that we built. F4E colleagues have worked as one team with our suppliers to deliver the PF coils. We capitalised on the strengths of each party and created a team that worked round the clock even during unforeseen circumstances such as the pandemic. It took us time to reach this point of understanding and to develop a different mentality which went beyond the standard dynamic of customer and supplier. In terms of technical challenges, I would highlight the risk of non-conformities due to the big size of the coils, and the reconfiguration of all tooling to respond to their needs,” explains Enrico Vizio.
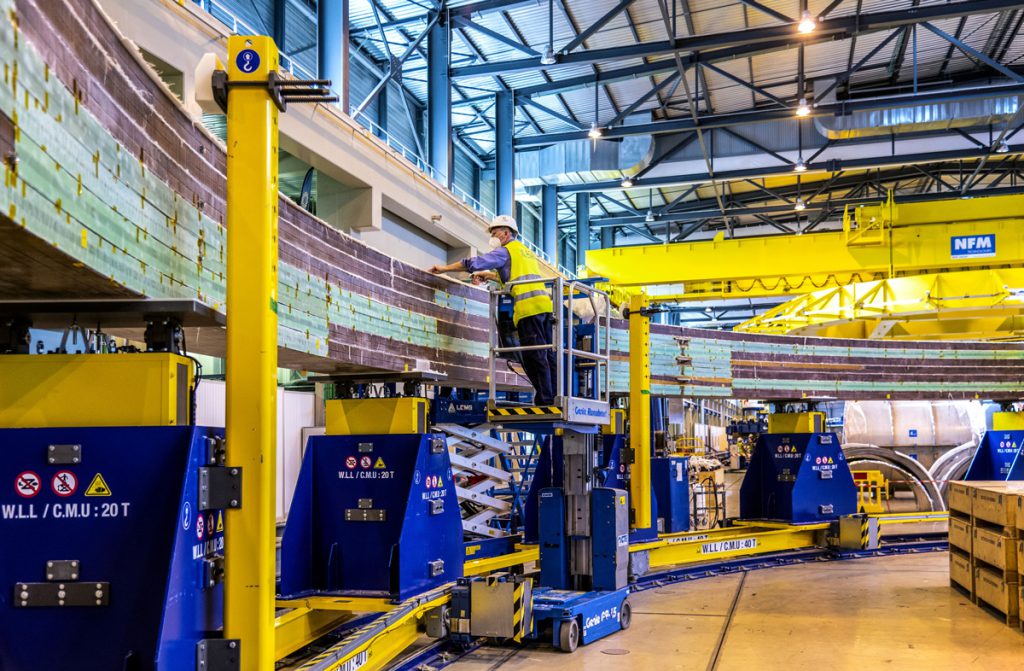
To understand better the manufacturing process, we spoke to some of our technical experts and asked them to break it down into main steps. First, we start by winding the lengths of conductor, made of around 1000 Niobium-Titanium (NbTi) and Copper (Cu) wires compacted inside a steel jacket, to arrive at massive rings that we will later insulate and impregnate with resin. PF 4 is made of 8 Double Pancakes (DPs), layers of spiralled conductor that will carry electrical current. Then, the DPs get stacked the one on top of the other, insulated, and impregnated again with more resin to become one piece, known as Winding Pack. The component also goes through electrical, thermal cycle and leak tests.
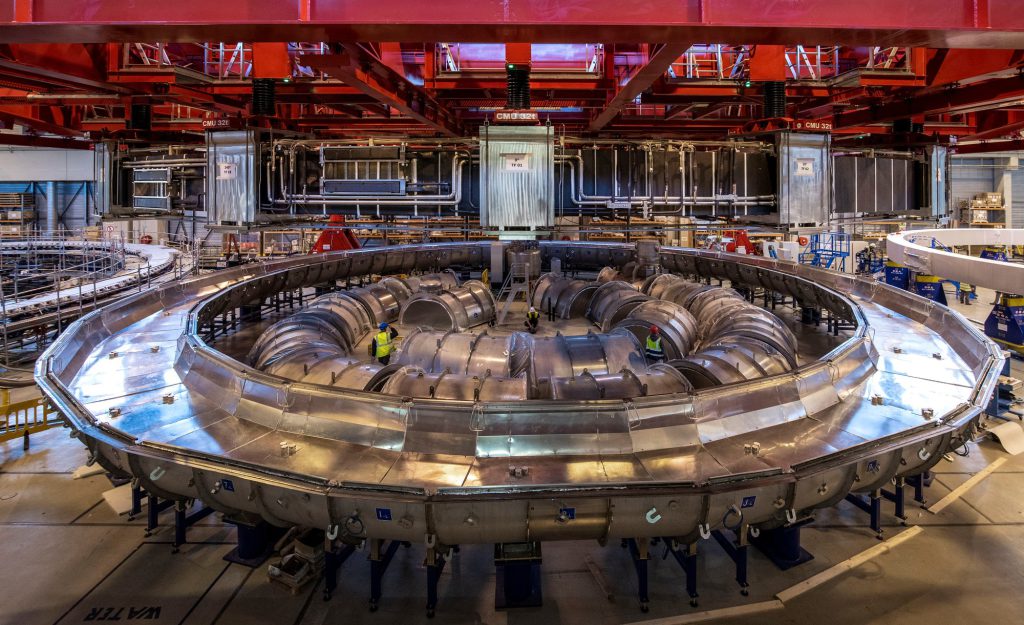
Pedro Carvas, F4E Technical Officer, elaborates on the effort behind the reconfiguration of all equipment. “We had to adjust all our equipment to the needs of PF4. Starting with the winding table, the stations for stacking and the cryostat. Much of this work needed to be carried out in a specific sequential manner in order to make the best use of space in the factory. We had to minimise any delays resulting from the pandemic and afterwards accelerate to make up for any lost time. Some of the lessons learnt from previous magnets in insulation, helped us improve and make gains.”
Mónica Martínez López, F4E PF Technical Responsible Officer, following closely the production and all tests, is quick to point out that all PF coils are not identical. “They do not only differ in size, but in fact each of them has specific adaptations. As for all ITER coils, robust electrical insulation to withstand the voltage developed during a faulty operation is an integral part of the manufacturing process. The insulation has undergone several strict tests. Only then the coils are ready to go through the final acceptance test inside the cryostats where the coils are cooled down at 80 K and brough back to room temperature so that we observe their response to mechanical stress conditions similar those of the ITER device. All these make-or-break steps along the way did not only raise the benchmark in manufacturing, but they also taught us a great deal. In fact, PF4 was the first coil not showing any defects during testing.”
PF3, the final poloidal field coil to be delivered by Europe, is expected to be handed over to ITER Organization next year in spring.