Operation Insertion accomplished
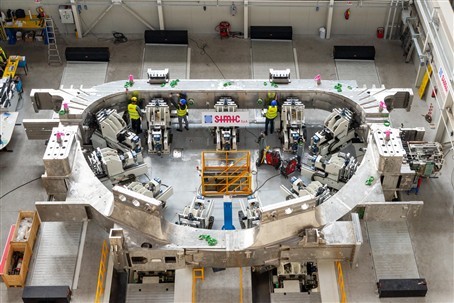

The clock is ticking for one of the most delicate steps in the fabrication process of the ITER Toroidal Field (TF) coils. “Operation Insertion” may sound like a classified mission to be carried out by experts in a remote location. The stakes are high and there is no room for improvisation. If you didn’t know any better you would think this is the teaser for an action blockbuster. Reality, however, often surpasses fiction and can be even more fascinating. A few kilometres from Venice (Italy), at the port of Marghera, where SIMIC has one of its facilities, Europe’s first Toroidal Field coil has been inserted in its case. The massive winding pack, the inner-core of the magnet with all its equipment, measuring 14 x 9 m, weighing 110 t, is now wearing its heavy stainless steel panoply of approximately 150 t. The TF coil cases, under the responsibility of ITER Japan, have been produced by Mitsubishi Heavy Industries (Japan), and Hyundai Heavy Industries (Korea). They measure no less than 17 x 10 m and almost like an “overcoat” they will protect the magnets whose mission is to confine the super-hot plasma when ITER is up and running.
How did we reach this important technical milestone? Once a winding pack has gone the cryogenic tests it gets wrapped with Tedlar® tape. In parallel, the coil cases go through a series of checks together with the tooling that will be used in insertion.


When technicians give the green light, the winding pack is lifted and positioned on the assembly rig. Pads are placed on the ground reflecting the D-shape geometry of the winding pack to rely upon them. With the help of the insertion tooling, the cases embrace the massive coil from left and right, and from top to bottom. Operation insertion lasts roughly one month.

From the moment the component is tucked in its coil case it will be officially considered a TF coil. “What makes insertion such a delicate process is the size and weight of the component –roughly 300 t with its cases— plus the extreme precision required. We are working with accuracies of 0.2 mm” says Boris Bellesia, following closely this contract on behalf of F4E’s Magnets team.

After the massive magnet is inserted into its coil case it’s time to start welding. Normally, it will take between four to six months to complete the welding procedure which initially will be conducted manually and afterwards automatically with two synchronised robots (narrow gap TIG welding). Then, for nearly two weeks, resin will be injected to fill the gap and to create a mechanical continuity between the cases and the winding pack. After this step is concluded, it’s time to procced with the machining of the magnet which is expected to last approximately four months. The magnet will then have to go through another round of final tests and get wrapped to be transported to ITER.
“We have entered the final production stage of the TF coils and it is the first time that we are performing these manufacturing steps. We have reached this point thanks to the excellent technical work and perseverance demonstrated by the different industrial partners who have contributed to the previous manufacturing phases, and thanks to the good collaboration with ITER Organization and ITER Japan. We look forward to this new exciting manufacturing stage during which we will use, just like in the past, our problem-solving skills and our technical expertise,” explains Alessandro Bonito-Oliva, F4E Project Team Manager for Magnets.
Paolo Barbero, SIMIC Project Manager, following this operation in collaboration with F4E, confirms that the insertion of the first winding pack into the TF coil cases has been completed. “Here at SIMIC, it gives us great satisfaction to have reached one of the most important milestones in the TF coil manufacturing process. This operation is technically very challenging, mainly due to the huge size of the parts and the very tight tolerances which need to be achieved. The assembly rig, a special machine designed and manufactured specifically for this purpose, is an extremely complicated automatic gigantic tool, considered as one-of-a-kind. We are impressed by the fact that it has worked remarkably well since the very beginning. We are very satisfied with the high level of precision obtained and this will pave the way for the next manufacturing steps such as the robotized narrow gap TIG welding, where we aim to get top quality results. We would like to thank all teams which spent the last years trying to make this achievement possible.”