Start of final assembly for Europe’s vacuum vessel sector
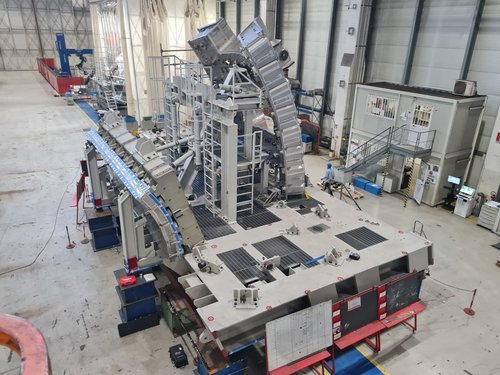
The first segments of sector 5 of the ITER Vacuum Vessel, manufactured in Europe, placed on the jig in the factory of Westinghouse/Mangiarotti, Italy, June 2021. (L-R) Poloidal segment 1 manufactured by Westinghouse/Mangiarotti and Poloidal segment 3 manufactured by Walter Tosto.
Another piece of the ITER Vacuum Vessel procured by F4E has arrived in the factory of Westinghouse/Mangiarotti, Italy. The operator of the crane is carefully lifting the stainless steel component, measuring 7 x 2.5 m, weighing 40 tonnes, to be positioned on the jig. A round of applause is heard in the workshop as it lands gently on a massive “bed” made of steel where it will remain to undergo dimensional checks. So far, two of the four segments that make a sector of the vacuum vessel have been delivered. The first, produced by Westinghouse/Mangiarotti has already gone through a series of tests. The second, manufactured by Walter Tosto, left Chieti a few weeks ago to reach Monfalcone. The remaining two segments are expected in the coming weeks to kick off the welding operations, which will involve roughly 40 technicians.
There is a sense of anticipation and excitement because the final of phase of assembly is about to start. The four parts produced in different factories, will finally come together under the same roof to become one—Europe’s first sector. More than seven companies, involving at least 200 people, have worked over the last years to roll out the production of the five sectors that F4E needs to deliver to ITER. Poloidal Sector 5 will be the first, produced by the consortium of Ansaldo Nucleare , Westinghouse/Mangiarotti, Walter Tosto (AMW) together with an extensive network of sub-contractors. Once the design was finalised, and the purchase of material completed, Europe set in motion the fabrication of this one-of-a-kind double-walled vessel that will house the biggest fusion reaction. If we had to simplify the fabrication process in a few steps, we would focus on the following: i) cutting and machining of raw forgings, ii) welding of sub-assemblies, iii) final machining. Each of them counts hundreds of sub-tasks. To give you an example, it took roughly four weeks to complete the welding of the forgings and plates of one segment using electro-beam welding, and at least 90 days to complete their inspection. Each sector counts 1 km of welds, and to comply with the stringent nuclear safety standards a lot of thorough work is required. Broadly speaking, we are now ready to take the final step, which will close the manufacturing cycle of the first sector.
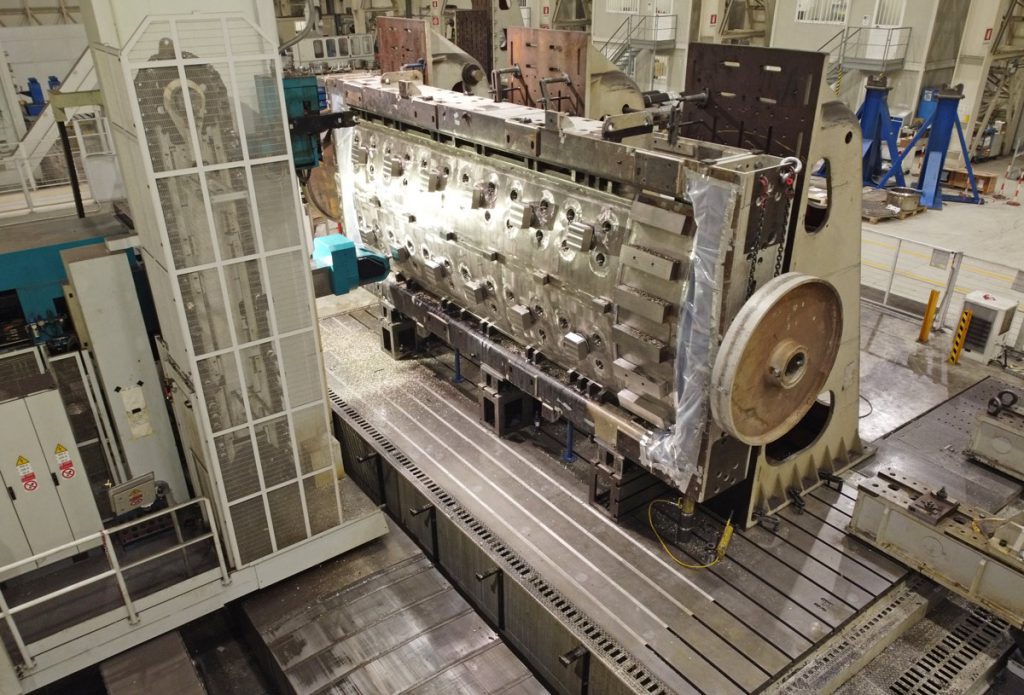
One of the initiatives introduced by F4E, to help with the fabrication of the vacuum vessel, has been the secondment of staff as “residents” located on different sites. Andres Dans Alvarez De Sotomayor is F4E’s Technical Officer in Mangiarotti, where roughly 150 technicians are involved in this task, looks back on the main challenges and the lessons learned. “What looked on paper as a rather straightforward fabrication process, proved to be far more complicated because of the size of the component, the sub-assemblies, tolerances and level of precision. Remember this is the first-of-a-kind vessel and we had to triple check everything. It was a case of learning by doing. The machining and welding were extremely complicated. First, they required good planning to co-ordinate the work carried out in different factories so that they are completed at the same; second, expertise in welding was essential to comply with the specifications; third, picking up good practice along the way was fundamentally important so that we learn from errors and apply those lessons in the sectors to come. We capitalised on this learning curve and managed to accelerate the production of the remaining sectors,” he explains. “On a personal note, it gives me immense satisfaction to see the completion of the first sector achieved in the factory, which has become my office during the last 10 years. We have worked so closely together with all the staff of the AMW consortium and bonded even more during the pandemic. I think it’s a great reward for all our efforts.”
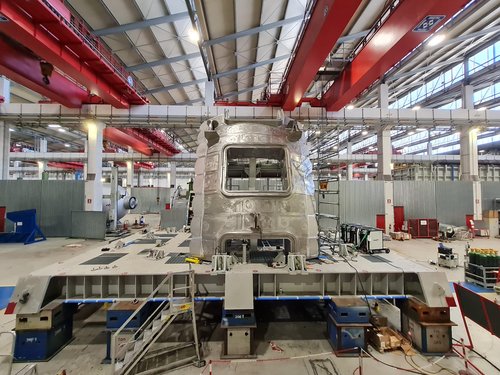
Gian-Battista Fachin, F4E’s Vacuum Vessel Deputy Programme Manager, uses this opportunity to highlight the strong partnership between the F4E, the contractors and ITER Organization. “The ITER project is based on the spirit of teamwork which cross-cuts the design and production of all its components. Europe’s contribution to the vacuum vessel is no exception to this. We managed to overcome technical difficulties, revise our working methods and implement new solutions by trusting one another and by respecting the contribution of each party. We build a supply chain made of different companies, operating in different countries, as part of the same project. We set common objectives and milestones so that they understand that they are inter-connected because their contribution has an impact on the entire project. I would like to thank them all for remaining focussed and resilient, in spite of the difficult circumstances we had to experience from the outbreak of COVID-19.”
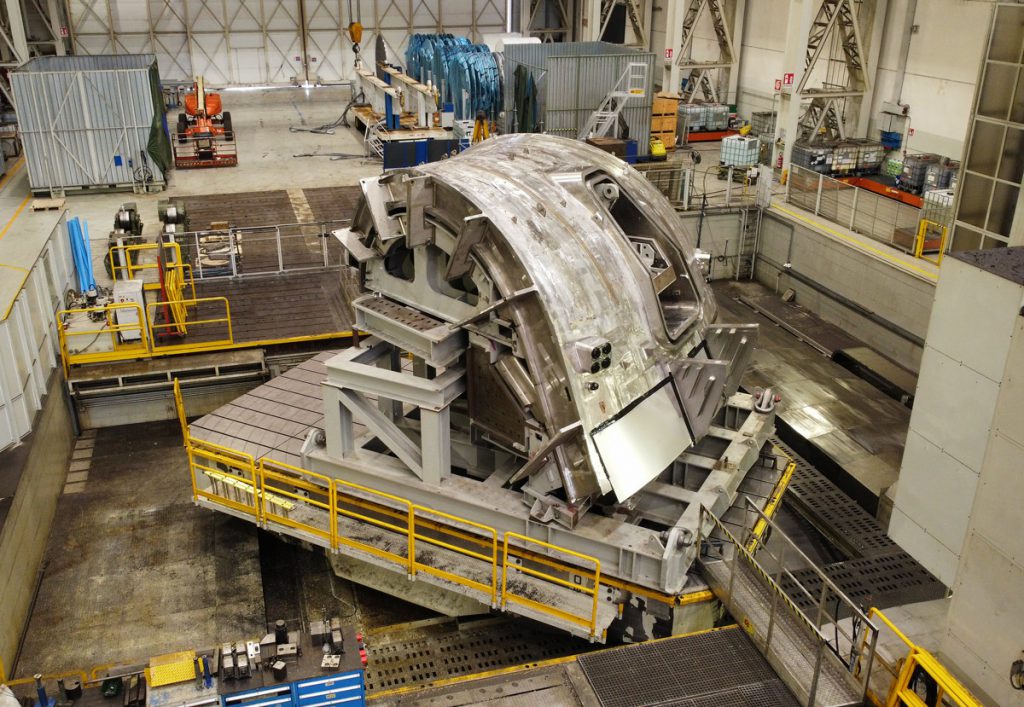
“The machining cycle of the first European segment of the ITER Vacuum Vessel, manufactured by the AMW consortium, has been completed. The process of assembly will soon begin with the other three segments on the big jig in the facility of Westinghouse/Mangiarotti (Monfalcone). We are concentrating all our efforts on first sector that will be delivered by F4E,” explains Fabio Presot, Westinghouse/Mangiarotti Customer Account Manager.
Cristian Casanova, F4E Programme Manager for the Vacuum Vessel, looks ahead at the next big milestones. “As we are entering the final phase of assembly the welding operations that will connect the four pieces are nearing. Apart from the hugely symbolic significance in the lifecycle of this project, this is an extremely important moment to draw lessons about transport, logistics, welding, final checks and delivery. In parallel, we need to keep the momentum for the remaining sectors, which are in different manufacturing stages. F4E, the AMW consortium, its network of suppliers, and ITER Organization are taking a big first step towards the completion of the first European sector.”