Success for Europe’s ITER Toroidal Field coil cold tests
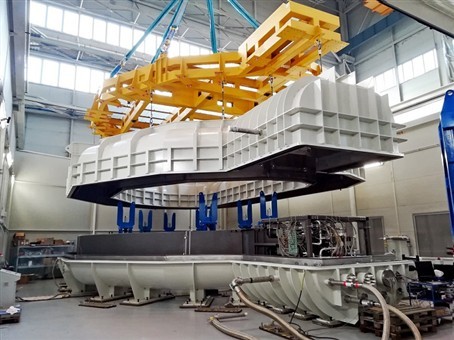

Close to Venice, the final act of Europe’s Toroidal Field (TF) coil magnets will be played. The breathtaking beauty of this city has inspired authors and directors to narrate some of the most powerful stories we have read or seen on screen. This time, however, engineers from all over Europe will join forces to link its legacy with the manufacturing of the most high-tech magnets in history. Europe’s ten ITER TF coils will undergo the final stage of manufacturing there.
At the workshop of SIMIC, an Italian company close to the port of Marghera (Venice), the container of the first TF winding pack – the core of the magnet – has arrived. It left from the port of La Spezia where at the factory of ASG Superconductors the 14 m coil had been produced. Now, it will have to go through a series of mechanical tests, and be inserted in a massive case weighing 180 t, so as to protect it almost like a knight’s panoply. Basically, the winding pack is going to turn into a magnet. Marianna Ginola, SIMIC Commercial Manager, is no stranger to the project. “It feels like coming full circle in a way…for years we worked hard to shape this component, and now we get to oversee its final production stage. To do so, we have invested in the infrastructure of our plant, collaborated extensively with our subcontractors, and trained our workforces for the delicate operations that we will have to carry out. The fact that this is the first of the ten winding packs that we will have to handle, makes this moment even more special” she says. The company has been previously involved in the fabrication of half of the radial plates which protect inside their grooves the superconductor.
After having unpacked the winding pack, the teams of SIMIC and its subcontractor, Babcock–Noell (BNG), had to perform a series of dimensional and electrical checks to inspect the coil. “The successful results have paved the way for the cold tests, which have been successfully concluded. In essence, the coil enters into the cryostat to be cooled down at 80 K (-200 °C) for nearly 20 days using a combined cycle of nitrogen and helium. Meanwhile, its electrical connections are placed at the exits of the cryostat so that they are tested with a current of 1000 A” explains Paolo Barbero, SIMIC Project Manager.

Piergiorgio April, who has been following closely the commissioning of the cryoplant and the cold tests on behalf of F4E, explains: “…it took us roughly one year to get the equipment ready. All the tolling had to be manufactured from scratch and will be used during the next years to test the inner-core of Europe’s TF coils. We will test them at extreme temperatures to check that the insulation is robust enough and that no cracks appear. Before they confine the superhot plasma they will have to experience freezing temepratures”. Boris Bellesia, also working in F4E’s Magnets team following the same contract, summarises the fabrication steps that will follow: “now that the cycle of cold tests has been successfully completed, dimensional and electrical checks will be performed again to inspect the state of the coil. Then, the coil will be moved to the assembly rig so as to be inserted into its case by using state-of-the art tooling and laser dimensional technology. The technical teams will have to move 110 t and fit them in the cases with millimetric precision. Subsequently, the cases will need to be welded in order to lock the metallic structure around the coil”.
Two important aspects will add to the challenge: first, the weld will be 120 mm thick, and second, the welding will be carried out only from one side within very complex geometries. For these reasons, ultrasonic technology will be pushed to the limits to inspect the component. Meanwhile, the gap between the TF coil case and the winding pack will have to be filled with reinforced resin to glue the two together. The high density of the resin makes this task particularly challenging. Try and imagine filling a tight gap of 4 mm thick and 35 m long with 1 m3 of resin that has the thickness of honey. It’s hard to imagine it but it will be performed.

Alessandro Bonito-Oliva, heading F4E’s Magnets team, highlights the success of the tests and the various interfaces of the ITER project. “The successful completion of the cold tests of Europe’s first winding pack pave the way to the final steps of its manufacturing until it gets inserted in its coil case. Try to think of it like a puzzle where the pieces need to come together. Most TF coil components like the winding packs and the radial plates are manufactured in Europe. The TF coil cases, however, are fabricated in Japan, and the thermal shields’ support of the Vacuum Vessel, are produced in Korea. All these pieces of equipment will need to be put together as part of ITER’s TF coils. It is an exercise of unprecedented complexity and planning. And we are working together with our industrial partners and the other ITER Parties to make this a reality” he explains.