The progress of ITER’s first Toroidal Field coil is impressive!
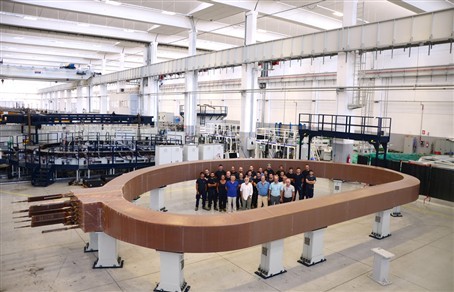

After having completed the insulation of ITER’s first-ever winding pack, the inner core of the massive Toroidal Field coils which will magnetically confine the hot plasma, the stage of resin impregnation followed. Technically speaking this has been one of the most delicate operations to be performed on the most complex magnet to date. For Alessandro Bonito-Oliva, F4E’s Project Manager for Magnets, his team and their suppliers, this is an important achievement underpinned by the collective commitment to deliver on time, plan carefully and be sufficiently flexible to adapt to the engineering challenges along the way.
A team of ten technicians worked relentlessly to get the magnet ready for this important manufacturing milestone. First, they had to apply the impregnation mould all over the surface of the 14 m high, 9 m wide and 1 m thick magnet. It has taken an entire week to cover its surface with pads in order to make sure that the resin injected during impregnation would flow in an even and controlled manner. Next, the magnet was enclosed in a layer of stainless steel sheets and clamped by heating plates to create a solid shell. Approximately 100 clamps, tightened one by one, sandwiched the magnet to compact the electrical insulation at the right level. Welding of the stainless steel sheets came next, and after having completed this step, the leak and electrical tests were carried out
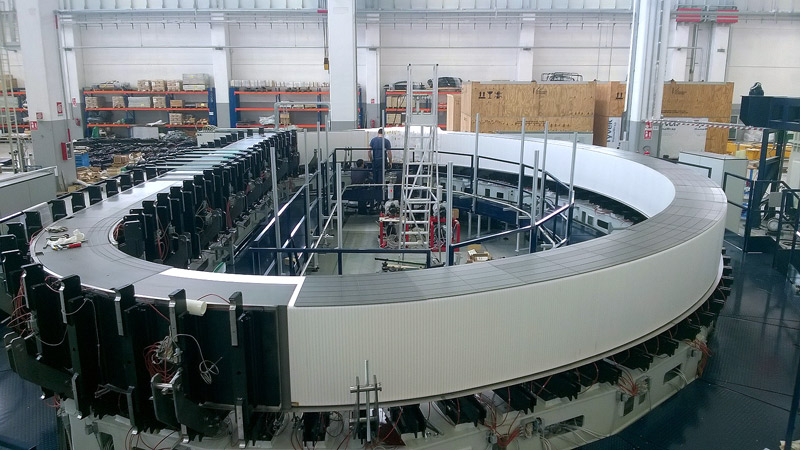
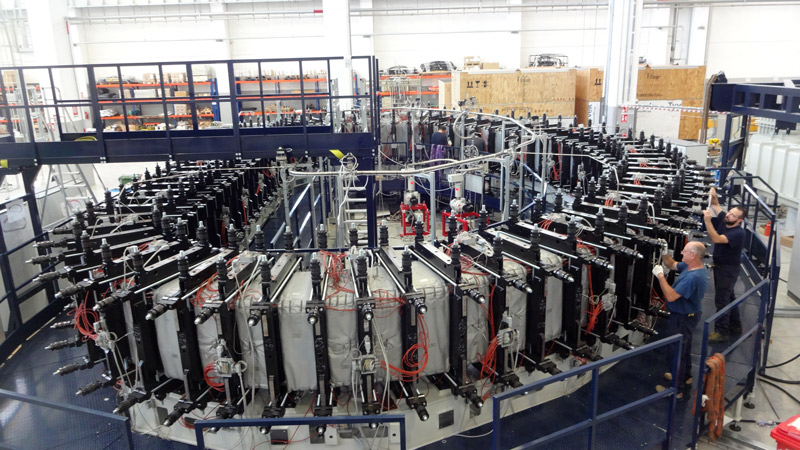
The successful completion of the works paved the way for the impregnation process. What were the main elements of this step? First, the component needed to be heat-dried in vacuum at 110 ˚C to eliminate any vapor or humidity trapped in the insulation. Second, with the mould under vacuum, resin was injected from the bottom of the magnet to fill in any gap, and pressure of approximately 3,5 atmospheres was applied to ensure complete filling of the mould. Finally, the winding pack went through a curing cycle, at temperatures reaching 155 ˚C during five days, before extracting the impregnated magnet from the mould.
After having completed this step, dimensional checks were carried out together with laser scans to examine the state of the component. In order to protect the component in operation a special conductive paint was applied all over its surface. So what works are currently ongoing? Magnetic measurements, checking the geometrical compliance of the magnet, are being performed. The mechanical works for the electrical joints are advancing together with the external helium piping, which is going to channel the cold helium in the coil, and the high voltage wire connection.
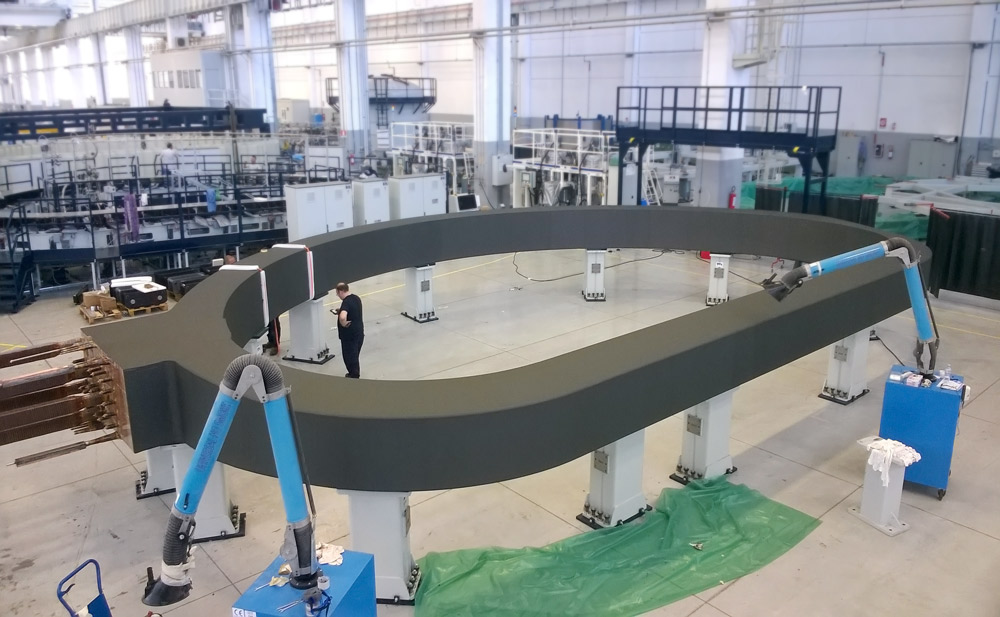
And what will come next? Paschen tests, considered as the most demanding electrical conditions because even a tiny insulation defect would cause failure, and last but not least, leak tests to assess the vacuum tightness. When this cycle of activities is completed then the winding pack will be transported to SIMIC to go through a series of cold tests and be inserted in its coil case.