Winding the final conductor for Europe’s ITER Toroidal coils
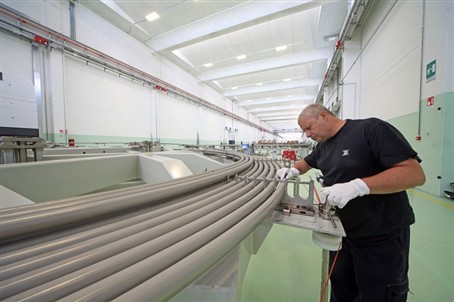

Under the massive cases of the ITER Toroidal Field coils (TF) and the multiple components which have been insulated, wrapped and impregnated to form the magnet, various lengths of superconductive conductor lie beneath. They nestle in the grooves of the finely machined pieces of equipment and when ITER is in operation they will carry current to the core of these massive magnets to generate the magnetic field required to confine the super-hot ITER plasma.
Europe’s final conductor has been wound in the ASG Superconductors facility, Italy, where F4E is manufacturing the 10 winding packs— the core of the TF coils. F4E’s industrial partners: Luvata, Oxford Instruments Superconducting Technology, Bruker European Advanced Superconductors, ENEA, Tratos and Criotec have all contributed to the fabrication of the conductor. China and Russia have also produced conductor lengths which have been used by Europe for its TF coils. After six years of meticulous work, the winding tooling has performed the final bending operation with a millimetric precision of 0.05mm/m.
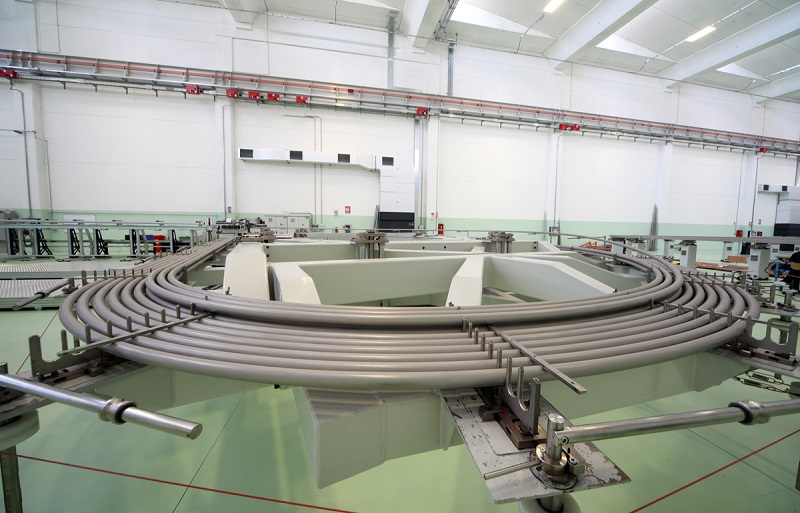
Each conductor is formed by a cable of roughly 1400 Niobium Tin and copper strands fitted inside a stainless steel conduit of about 45mm diameter. After arrival on-site, it is leak tested, before it is moved to the winding station where it is de-spooled, cleaned and sandblasted and finally, bent into a spiral D-shape trajectory, just like the shape of a TF coil. When two layers of conductor are wound they form a “Double Pancake” (DP). For Europe’s TF coils 70 DPs have been produced in total. Depending on the type of the DP, the conductor length may vary between 760 m for a regular DP or 450 m for a side DP.
Winding takes roughly one week and teams of technicians are constantly overviewing the process. On completion, the remainder of the DP manufacturing process will take approximately eight months. Afterwards, it should be ready to be assembled into the last TF coil winding pack due for delivery in 2019. Robert Harrison, F4E’s Technical Officer following the works closely explains that “the precision achieved has been the most remarkable aspect of this process and bears credit to the staff and engineering involved.”
Alessandro Bonito-Oliva, F4E’s Project Manager for Magnets, explains that “this is the most critical manufacturing phase. The success of all subsequent manufacturing operations depends on the accuracy of the winding. This is also the first manufacturing step of the winding packs that we will not be repeating. The excellent collaboration between our partners and the good co-ordination of all technical interfaces has brought this operation to a successful conclusion. For Europe’s TF coils, the winding of the conductor is over!”
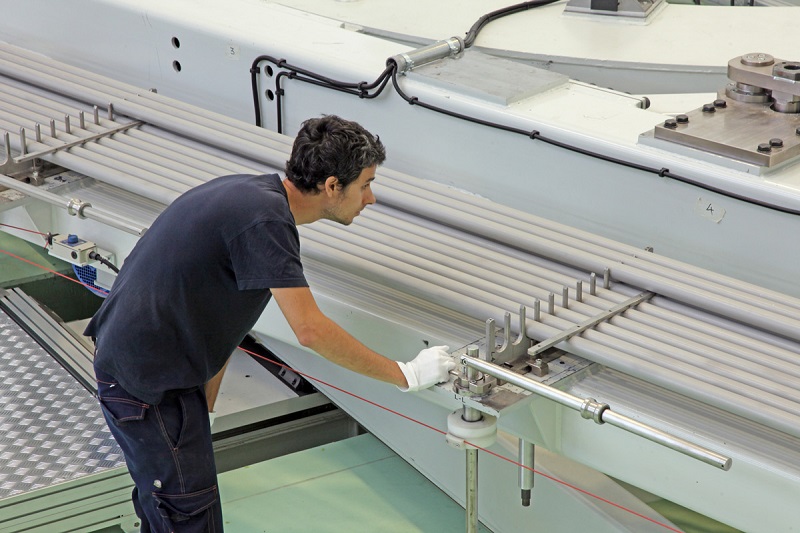