Cryopanels completed for the MITICA cryopump
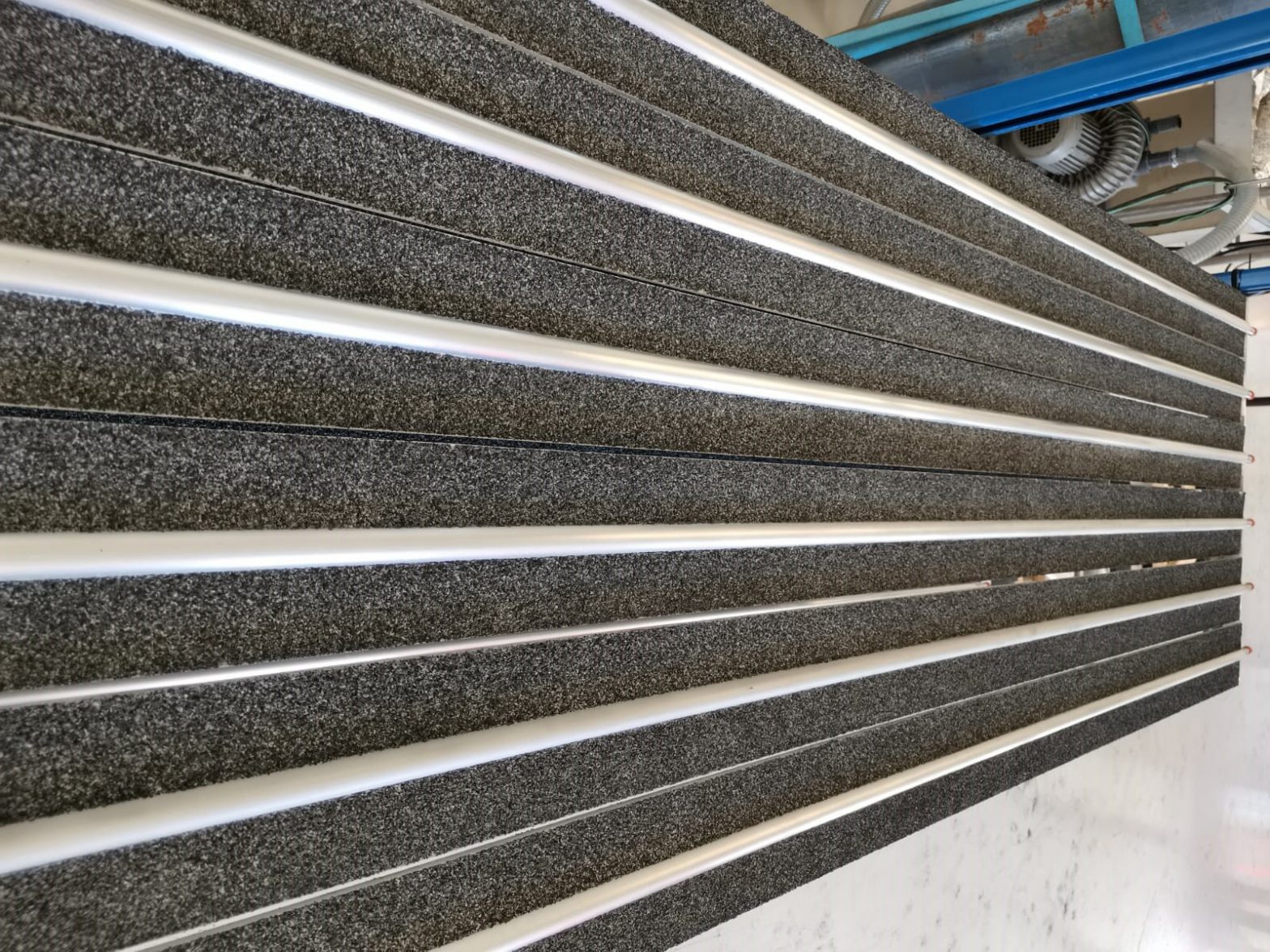
Completed cryopanels with their charcoal coating in SDMS, Saint-Romans, France, April 2021.
MITICA is the test facility located in Padua (Italy) devoted to the validation of the technology required by the ITER neutral beam system. This part of the machine will help to heat the plasma contained in the vacuum vessel. A key component of MITICA is its cryopump, which will ensure the vacuum conditions needed to perform the experiment.
The cryopump consists of 64 pumping sections assembled in a frame. Each pumping section is made of three cryopanels (the components that perform the vacuum pumping function) and four thermal radiation shields (which keep cryopanels at the right temperature). A total of 231 cryopanels have been successfully coated with charcoal and are now ready to be assembled in the MITICA cryopump.
The manufacturing results from a contract signed between F4E and SDMS, which started in May 2018. The cryopanels, made of aluminium, went through different phases until they reached their final stage. After being free issued by F4E, they were first submitted to grit blasting, a process in which microparticles are shot against the surface of the material to give it a particular roughness. Then, experts applied a ceramic glue to the panels prior to spraying the charcoal granules. Finally, experts baked the panels in an oven and performed adherence tests. The entire process was implemented under strict cleanliness conditions to ensure that the panels are adequate to work in vacuum.
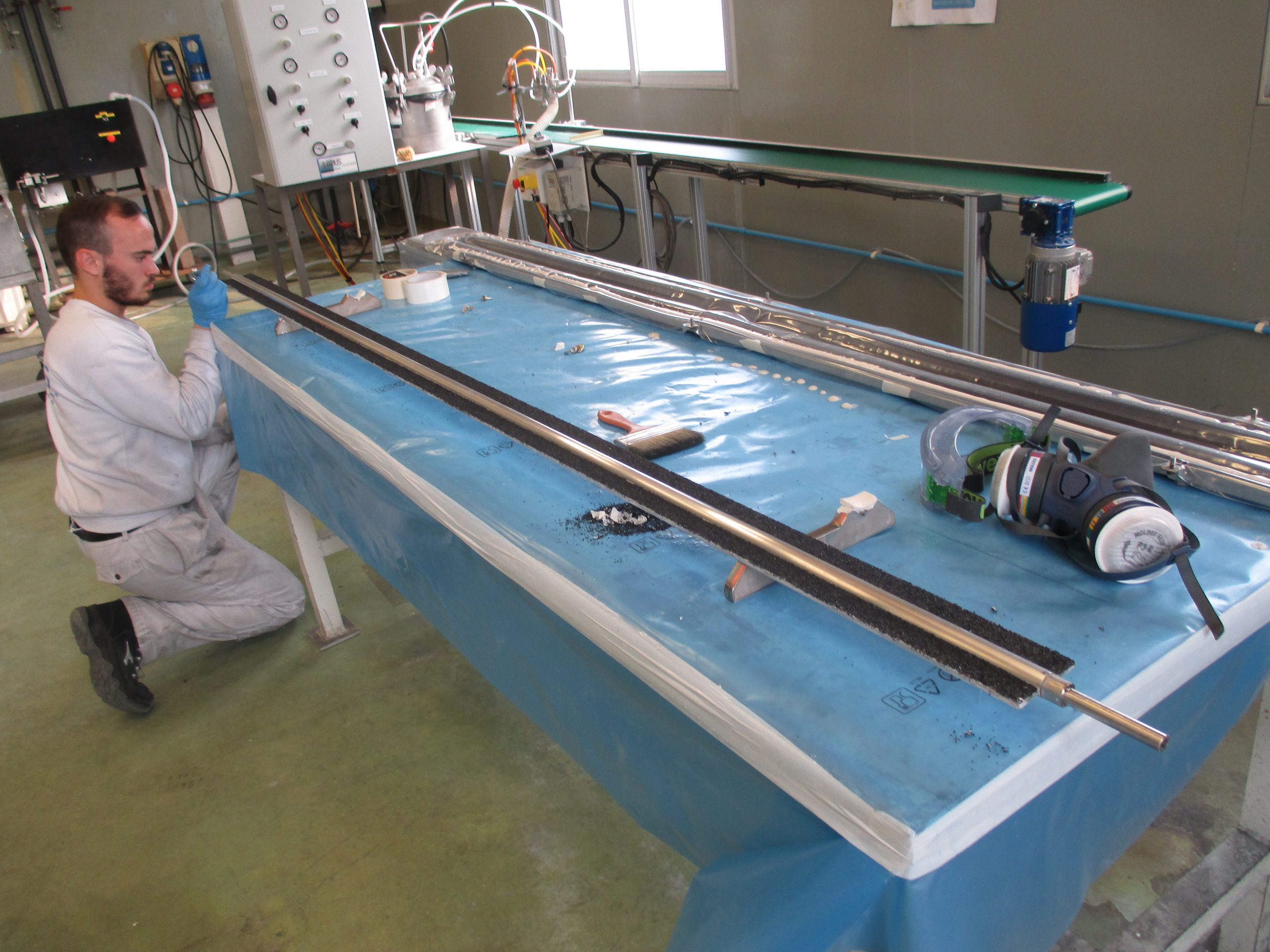
But why do cryopanels need charcoal coating? Cryopanels pump out thanks to their very low temperature (4 K). In these conditions, particles stick to their cold surface, providing extreme vacuum as a result. The charcoal applied is a very porous material, thereby multiplying the effective surface area on which gas particles can be trapped. One could say that charcoal coated cryopanels act as “air sponges”.
Obtaining a suitable coating process, however, has not been straightforward. “SDMS has already performed charcoal coatings on cryopanels manually in the past. The challenge in this project was to semi-automate the coating process in order to obtain a homogeneous result on all the profiles. SDMS set up a workshop entirely for this purpose and, after several months of tests, settings, adaptations, and thanks to the rigour and expertise of Clément Astruc, Manufacturing Quality Manager, SDMS has developed a reliable and repetitive process,” explains Amanda Rome, SDMS Project Manager.
“After months of trials by SDMS, and close supervision by the F4E team, we finally developed a charcoal coating process that met ITER Organization’s demanding requirements. This result was achieved thanks to the perseverance of the people involved. The supervision efforts of all parties were enforced during series manufacturing in order to avoid deviations,” explains Aurélien Rousseau, F4E Cryoplant & Fuel Cycle Project Manager who followed this contract.
“The outstanding outcome of this project is the result of the close collaboration between SDMS, F4E, ITER Organization and RFX. Together we have been able to make the most of the knowledge acquired so far in charcoal coating to successfully qualify the process and coat more than 230 panels. It’s worth to point out that this is the first time that such a large number of panels are coated with charcoal,” concludes Luis Mora, F4E Cryoplant & Fuel Cycle Technical Project Officer.