Designing the ITER Divertor Remote Handling system
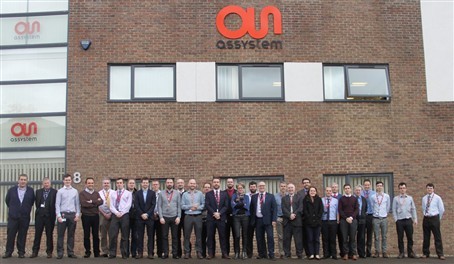

F4E and Assystem UK have started working on a long list of activities leading to the preliminary design of the ITER Divertor Remote Handling system. The kick-off meeting took place in Sunderland, at the offices of Assystem UK, gathering 30 experts who will have the opportunity to shape some of the most high-tech technologies combining man in the loop robotics and virtual reality platforms.
Generally speaking, the design phase just launched is one of the most important stages in the lifecycle of components. Technical experts tussle with issues like: how to integrate components in the machine, conduct risk analyses and finally come up with a preliminary design of the handling systems. It is a process underpinned by a lot of reviews and a continuous exchange of expertise. When this stage is completed, two more years will be required to reach the maturity of the final design prior to manufacturing.
The work stems from the contract signed between the two parties setting as an objective the manufacturing of two multifunctional movers and two toroidal movers for the ITER divertor. Other pioneers in the field of remote handling, such as the UK’s Remote Applications in Challenging Environments (RACE) facility linked to Culham Centre of Fusion Energy (CCFE) and Soil Machine Dynamics Ltd (SMD) together with Finland’s Technical Research Centre (VTT) and the Tampere University of Technology (TUT), will also contribute with their know-how.
Due to the nature of maintenance activities that will need to be carried out remotely and with extreme precision, a number of potential risks on tooling for cutting and welding, affecting remotely handled operations, will be addressed. The use of water hydraulics at a 50 ˚C radiation environment will be explored as well as the identification or the development of a suitable manipulator to perform complex maintenance tasks inside the ITER machine.
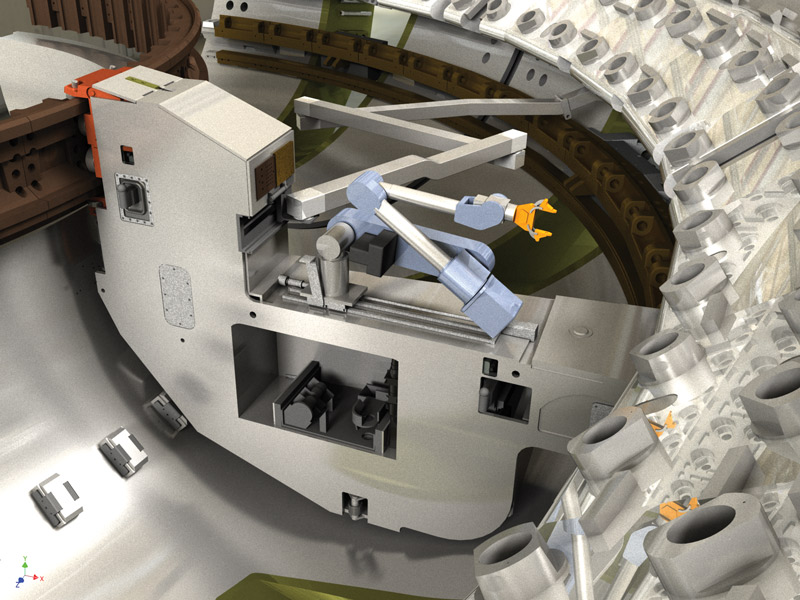