European prototypes for ITER Divertor Cassette completed
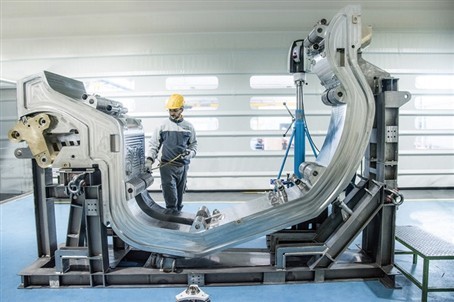

During the fusion reaction the lower part of the ITER machine will receive a significant amount of the heat coming from the 150 million °C burning plasma. The impurities will be directed to fall, just like ashes do, in a massive “ashtray” called the divertor, which covers an area of 142m2. The ITER Divertor is made of 54 pieces of stainless steel which can be removed, known as “divertor cassettes”, which measure 0.8 x 2.3 x 3.5 m and weigh roughly 8 t. The insertion of these components and their maintenance will be carried out remotely.
Before embarking on the manufacturing of the 54 ITER Divertor Cassettes , F4E in collaboration with industry had to develop real-size cassette prototypes to demonstrate the feasibility of their fabrication. For this reason, Europe developed a procurement strategy which encouraged several suppliers to get involved in order to check whether they had the skills to manufacture this component with the required quality and at minimum cost.
It all started in 2012 with the signature of a procurement arrangement with ITER International Organization. Then, F4E conducted a market survey, identified the technologies required for the fabrication of this component, and one year later launched a call for the production of the first real-size prototypes. The race started with three candidates which presented the best set of skills matched with value for money. Two of them decided to carry until the finish line: Walter Tosto, and a consortium consisting of CNIM-SIMIC. A few weeks ago the final dimensional checks were completed, offering proof that the companies were able to manufacture the prototypes. This has been the fruit of the hard work, undertaken by F4E and its industrial partners, which started approximately four years ago. Bruno Riccardi, F4E Divertor Technical Co-ordinator, and Laurent Guerini, F4E Technical Project Officer responsible for these contracts with the support of Montse Felip, José Andrade and Quality Officers, explain that “…due to the demanding requirements of this component we had to work closely with other teams inside F4E and with our external suppliers. To give you an idea of the rigour with which our work has been carried out…more than 700 documents per prototype have been processed and each prototype had to undergo extremely demanding tests. We have come a long way”.
The ITER Divertor Cassette is one of these components which may deceive the eye. It may give the impression that it is fairly straightforward to machine, but the moment fabrication kicks in then all sorts of manufacturing details come to play making it a far more complicated job. It is a piece of equipment that requires extreme precision and expertise in welding. In the case of the CNIM-SIMIC consortium and Walter Tosto there are at least 100 welds on the real-size prototypes produced. Furthermore, the components have to go through nondestructive testing (NDT), and a series of inspections regarding their volume and fabrication using radiographic and ultrasonic techniques.

F4E’s suppliers have successfully performed the tolerance assessments and the cold/hot helium leak tests. With these results in hand, F4E is now getting ready to launch the call for the production of the first series of ITER Divertor Cassettes, which will not exceed at this stage the total number of 20. To find more about the forthcoming tender check F4E’s industry and fusion laboratories portal. Patrick Lorenzetto, FE4 Head of In-Vessel Project Team, confirms that “this is an important milestone because it demonstrates Europe’s industrial capacity to manufacture this component and paves the way to new business opportunities”.