European success for another Inner Vertical Target prototype
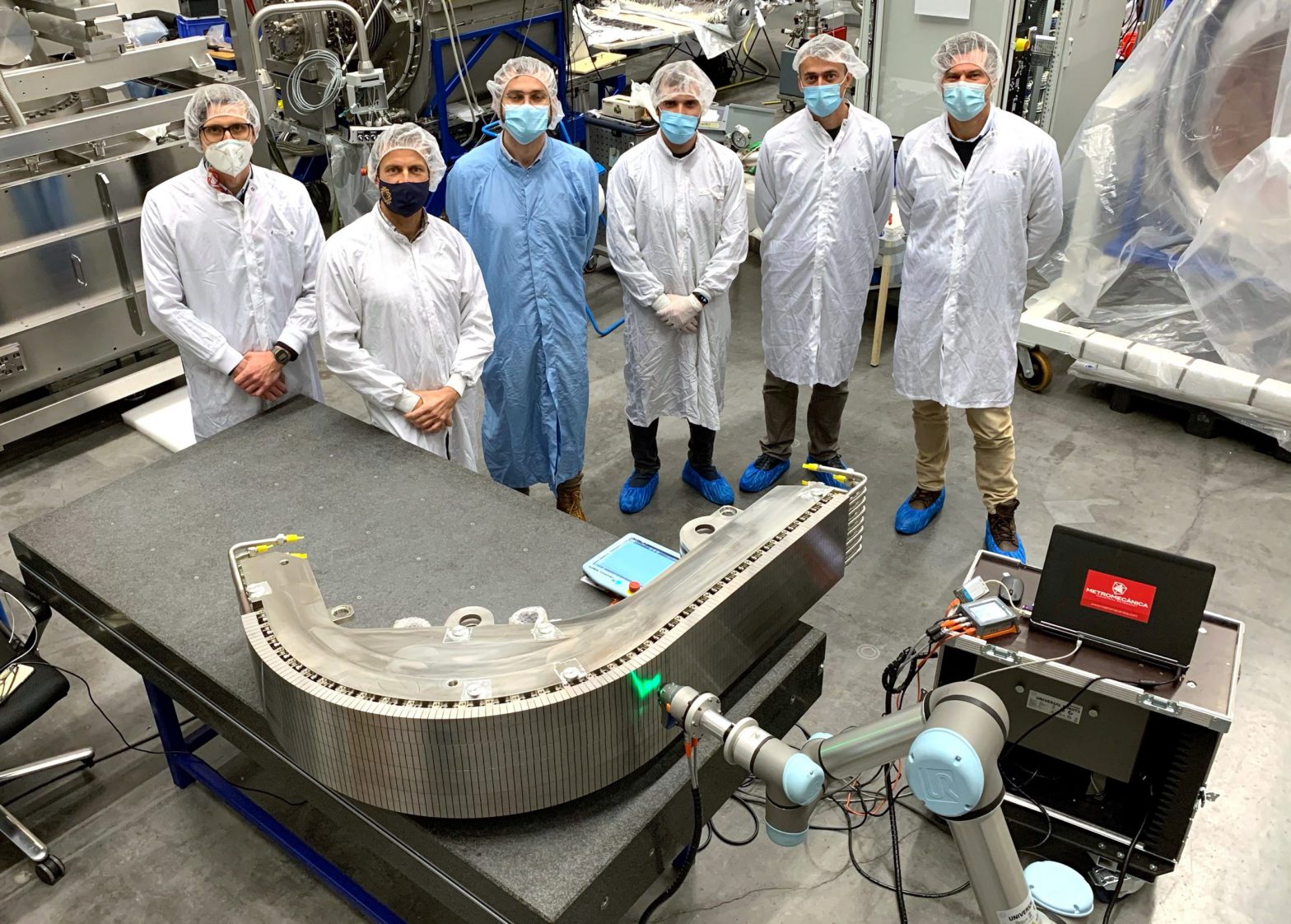
Representatives of Fusion for Energy, Research Instruments (RI), Metromecanica during the Inner-Vertical Target dimensional checks performed at the workshop of RI, Germany, December 2020
Ending the year on a high note by meeting a significant milestone puts all the hard work into perspective, especially after facing a global pandemic with severe implications on our daily life. For the team of engineers in Research Instruments (RI), Germany, the completion of the ITER Inner Vertical Target (IVT) prototype’s engineering phase was their trophy. In record time and with tonnes of iron will, the team of experts successfully produced the second European prototype of a component considered as extremely complex even for those counting decades in the fusion community.
Years ago, F4E took the decision to engage in parallel with different suppliers in the development of In-Vessel components in order to spread expertise from an early stage. Consequently, more players have started entering the fusion energy market each having different strengths. For components like these, manufactured for the first time ever, keeping the learning curve as inclusive as possible pays dividends.
The Divertor IVT prototype weighs 0.5 t and measures approximately 1.5 m. Its surface is covered by 1 104 tungsten blocks, which resemble to shiny thick tiles. In total 54 divertor cassettes will form the ITER Divertor, and when the machine is operational, the maximum expected temperature on the tungsten surface of a cassette will be in the range of 2000 °C. The blocks will face the hot plasma and right beneath them a circuit of copper alloy pipes with pressurised water will flow to cool down the heat.
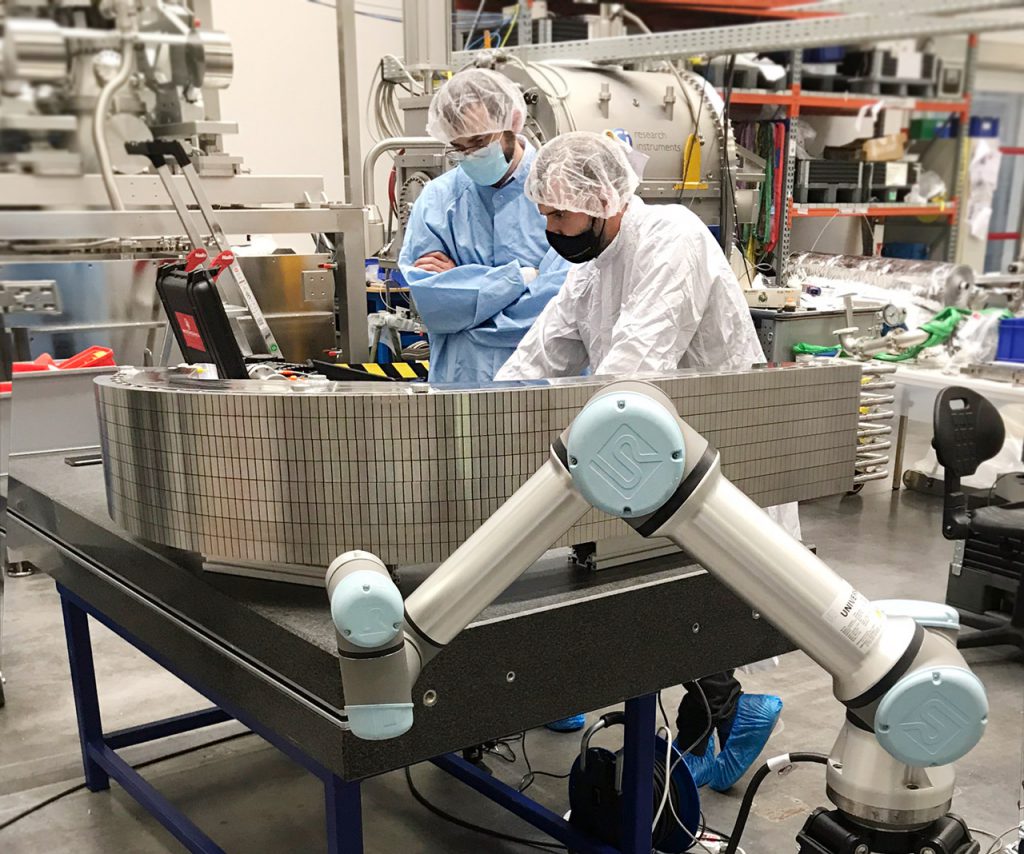
Understanding the nature of the beast helps taming it. This is exactly what F4E did together with RI in developing this prototype. The company with a proven track record in brazing and working with copper alloys, studied the functions of the IVT for roughly two years and took the first R&D steps producing small mock-ups. In 2017 they started working on a bigger prototype, which required procuring larger amounts of materials and scaling up their tools. As soon as the prototype pre-assembly was completed, F4E’s Technical Support Services, and their supplier Metromecanica (Spain), provided an automated system to measure quickly and with extreme precision any of the 1200 gaps between the blocks of the component. As the new year kicked-off, the prototype was getting ready to leave from RI to the Efremov Institute, Russia, in order to go through high heat flux tests.
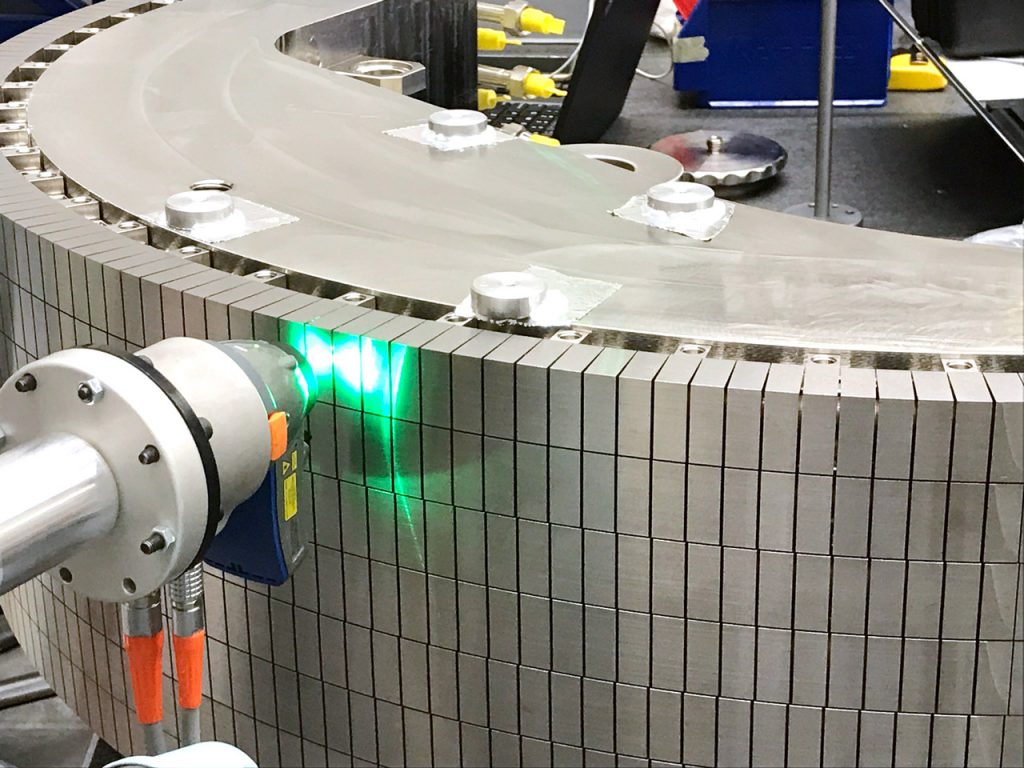
Michael Pekeler, Director of Superconducting RF, Fusion and Special Manufacturing, Research Instruments (RI), elaborates on the importance of this achievement. “We are very happy to have reached this milestone. This would not have been possible without the excellent cooperation with the F4E team, the passion and dedication of our project team. It is a clear demonstration of the high quality products we design and manufacture at RI. It is also a success bringing us closer to the qualification for the tender phase of the IVT series production. We are delighted to do our part bringing ITER to life by contributing to the development of high tech components as challenging as this one.”
Pierre Gavila, following this contract on behalf of F4E’s In-Vessel team explains, “We are pleased to see the second IVT prototype reaching this important project milestone. It is important to keep in mind that this component has not been produced before and it required from our European suppliers extra effort to meet the strict requirements. We are eager to see how the prototype will perform during the high heat flux tests performed in Russia.”