HELCZA—the new facility where F4E will test In-Vessel components
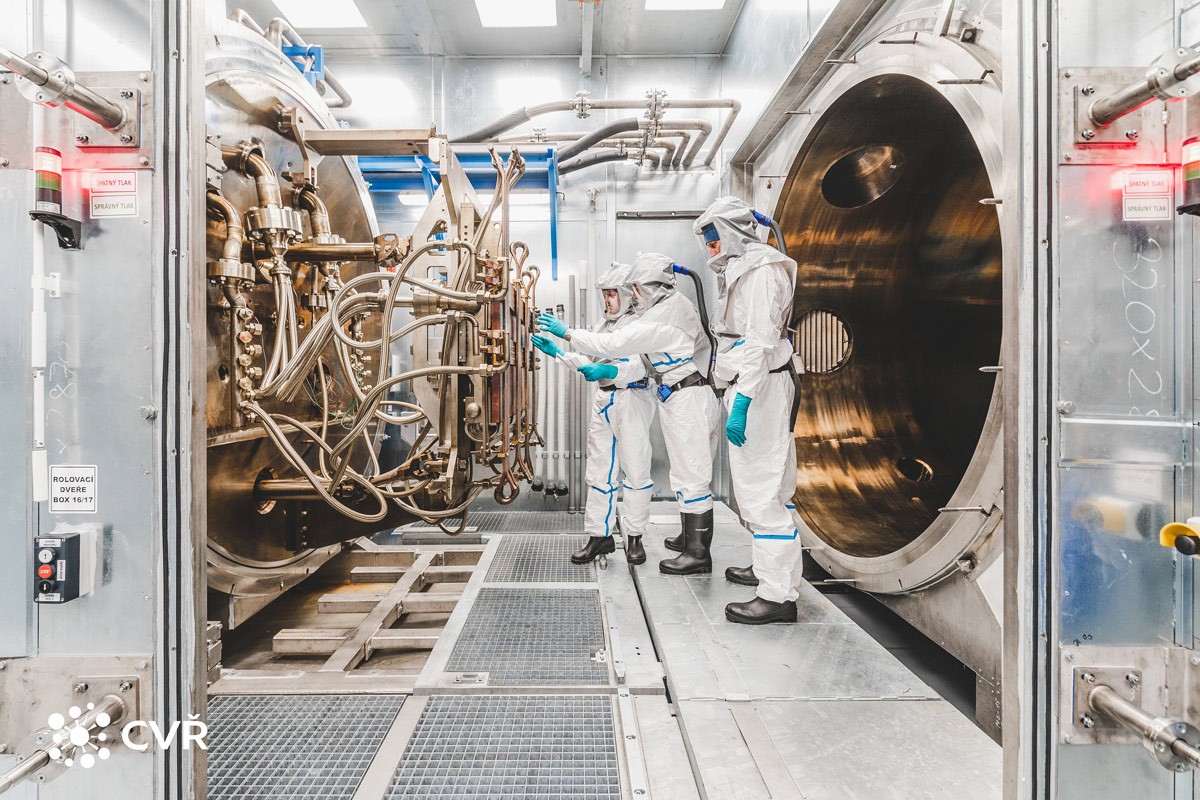
Positioning shielding frames on test sample, HELZCA Facility © CVŘ
Apart from inspiring Europe’s workforces to improve their technical skills, part of ITER’s legacy will be the creation of facilities to perform tests on various pieces of equipment. Knowledge, state-of-the-art infrastructure, skilled staff and the capacity to perform difficult technical tasks in various areas are some of the features that these centres have. HELCZA, located in Plzeň, Czech Republic, fits this description and it is where F4E will be testing the prototypes of the first wall panels.
Europe is responsible for the production of 215 first wall panels—roughly half of the total that will be used in the ITER device. They will form a first wall to protect the vacuum vessel housing the fusion reaction. These beryllium tiles will be joined onto a stainless steel-copper alloy bi-metallic structure to cover an area of 600 m2. Each panel measures approximately 1 x 1.5 m and weighs up to 1.5 t. Prior to manufacturing the “real” components, the prototypes would need to go through several tests to validate their fabrication process. The high heat flux testing is probably the most challenging.
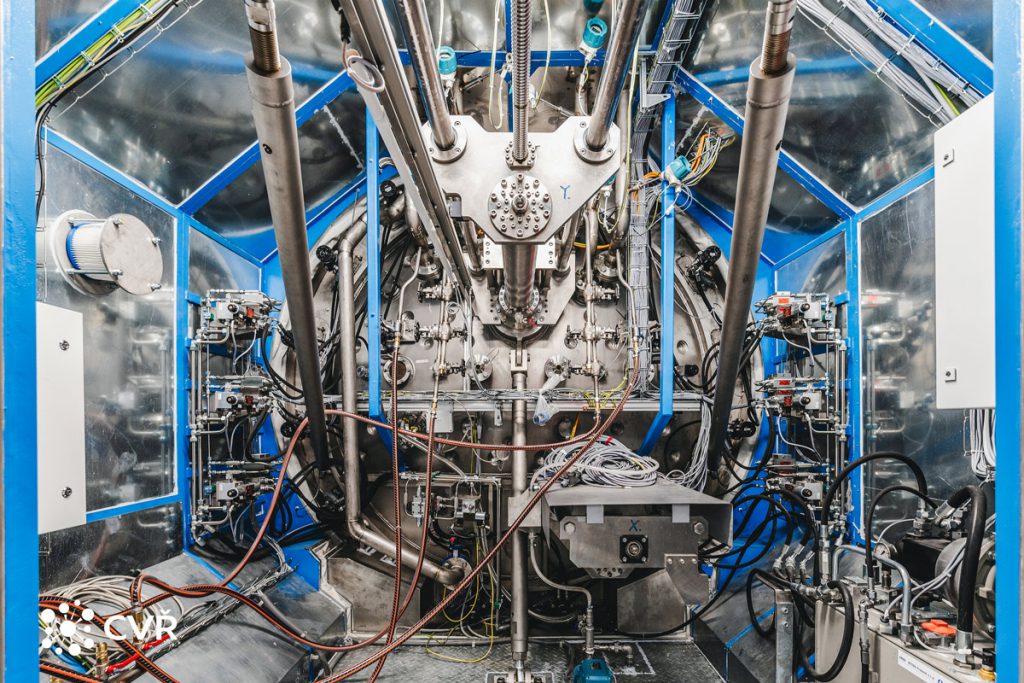
F4E’s decision to invest in the development of a high-heat flux test facility, able to handle components containing beryllium, was one of strategic importance. Essentially, it was about putting in place human capital, expertise and equipment for the future. Almost nine years ago, F4E launched a call to co-finance such testbed. With the support of EU funds, and the Ministry of Education, Youth and Sports of the Czech Republic, HELCZA became a reality. Its main subsystems are the vacuum chamber, the electron beam gun used to heat the surface of the tested items, the vacuum and cooling systems. The facility is also equipped with a set of advanced diagnostics to monitor the panels’ behaviour during testing. Finally, the beryllium management system will ensure the safety of the operators before, during and after the testing. The performance tests on the ITER first wall full-scale prototypes will start in the next weeks.
“It will take roughly two years to conclude the tests of the three prototypes produced by F4E,” explains Pierre Gavila, who has been following the design, construction and commissioning of the facility. “The facility may also be used, in the near future, by companies or associations involved in fusion R&D activities, in particular under the umbrella of EUROfusion for the activities related to the DEMO reactor. The presence of such testbed in Europe is an important asset for our engineers and scientific community.” “We are very eager to see the results of the testing of the first wall full scale prototypes, also to get feedback in view of the start of the series production,” says Stefano Banetta, F4E In-Vessel Project Manager, responsible for the contract of the first wall panels.
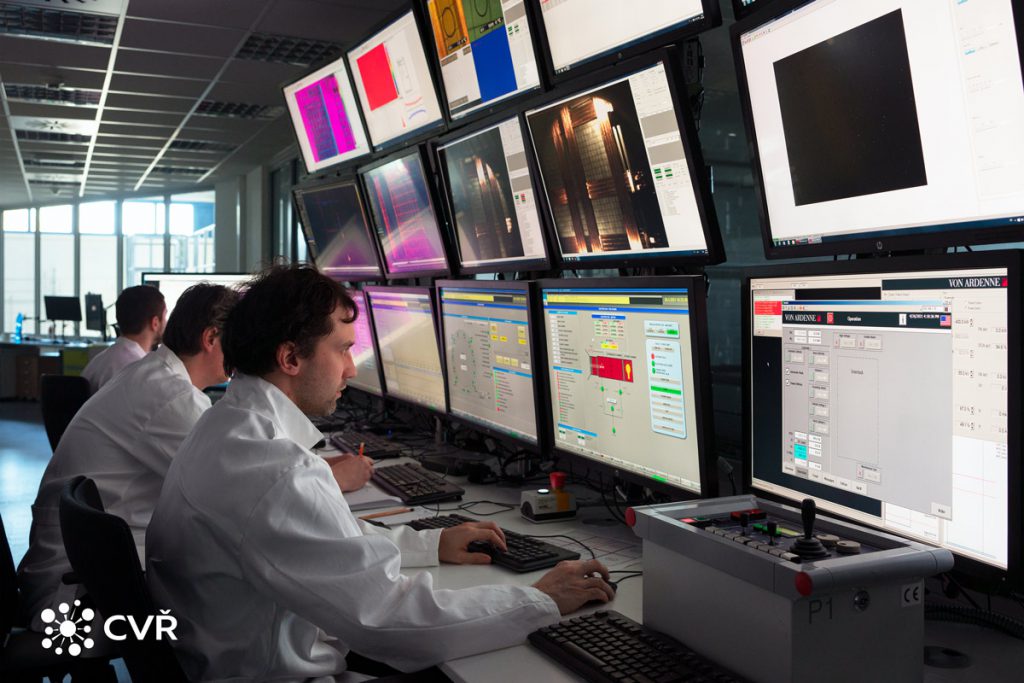
Centrum výzkumu Řež (Research Centre Řež in English) is the entity running the facility. We spoke to Daneš Burket, R&D Section Director, to understand how they see their contribution to ITER and which technology areas could benefit from their services. “This project allows us to take part in one of the most challenging scientific and research adventures of today — ITER. It is exciting to design and put into operation a unique test facility, where cutting-edge technologies and technical solutions are used.”
What kind of test can be performed? “We can carry out thermal resistance tests and check the cooling capabilities of various components; do material research and conduct studies of phenomena under high heat flux conditions. This said, the HELCZA facility is not limited to fusion applications. It can also be of service to the aerospace industry. In addition, HELCZA is interconnected to laboratories working with hazardous materials, which might generate carcinogenic dust particles during handling and testing. Therefore, there is the potential to check applications in the areas of safety, health and environment.”