How will engineers monitor the plasma performance of ITER?
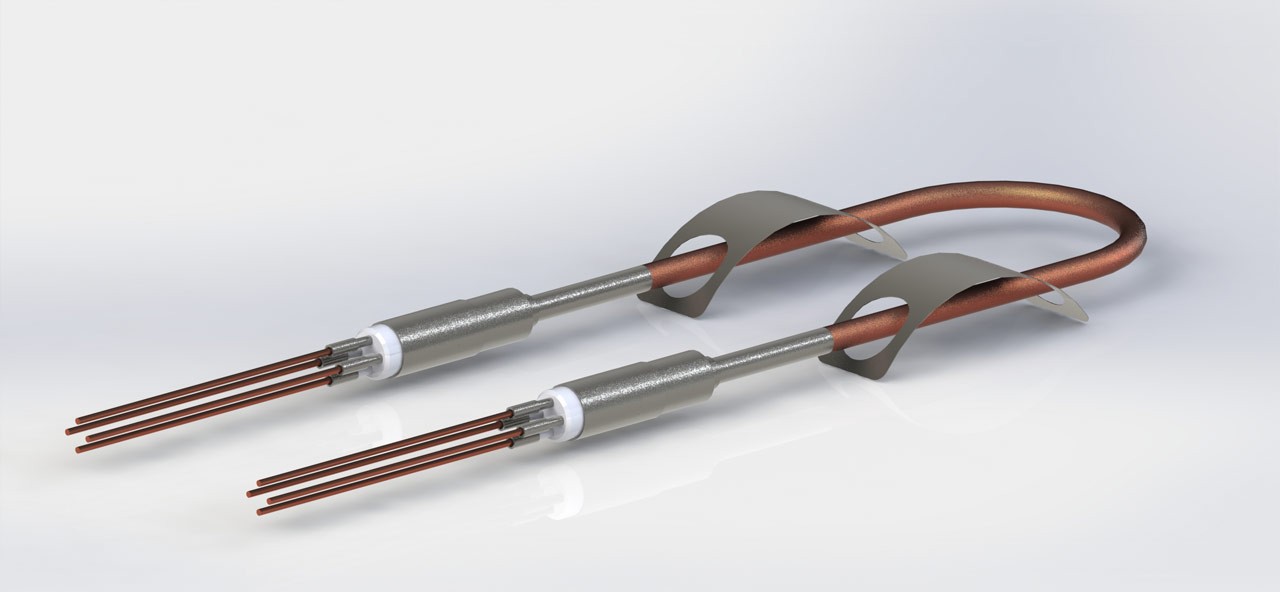
Sample of a four pin cable to be manufactured by Thermocoax in order to connect 1200 sensors inside the ITER Vacuum Vessel. The procurement is managed by Fusion for Energy. ©Thermocoax
When ITER is up and running, engineers will not be able to enter inside the vessel which will house the biggest fusion reaction. Those, however, following the project would need to install “eyes” and “ears” to closely monitor the performance of the different components in the hermetically-sealed chamber. This is exactly the mission of the F4E Diagnostics Programme developing the necessary equipment to keep track of the machine from a distance.
Special cables will be need to be manufactured to connect 1200 sensors, junction boxes, connectors for the transmission of electrical signals coming from the inner skin of the vacuum vessel. Almost like branches of a tree they will run under the blanket and go through the upper ports of the vacuum vessel reaching in total 60 km of cable length. F4E, being responsible for 25% of the Diagnostics equipment of the ITER device, has signed a contract with Thermocoax for the production of 1200 cables for the amount of 1.6 million EUR. The production of cables will be carried out during the next two years with a final delivery scheduled for mid of 2022.
Various parameters had to be taken into consideration prior to moving ahead with production. The transducers and the different in-vessel “obstacles” did not allow for a single design. Instead, custom solutions were required for every sector of the vacuum vessel and diagnostic port. There are at least 103 identifiable cable looms, broken down to several similar subtypes. The limited space in the machine and the requirements of tooling space for fixing and maintaining other in-vessel components played a role in their design. Most of all, the major thermal loads and plasma radiation to which they will be exposed had to be taken into account.
Miguel Perez Lasala, F4E Diagnostics Project Officer, following the fabrication of the mineral insulated cables gave us the background. “We started the pre-qualification programme in 2016 and for two years we considered various options drawn mostly from the fission industry. It took roughly two years to review our findings and to agree on the specifications of these cables for ITER. We signed the contract for manufacturing towards the end of last year and we will soon be launching a new tender for the 12 000 clamps which will need to be welded so as to mount the cables on the vacuum vessel,” he explains.