Two SOFT Innovation prizes go to technologies supported by F4E
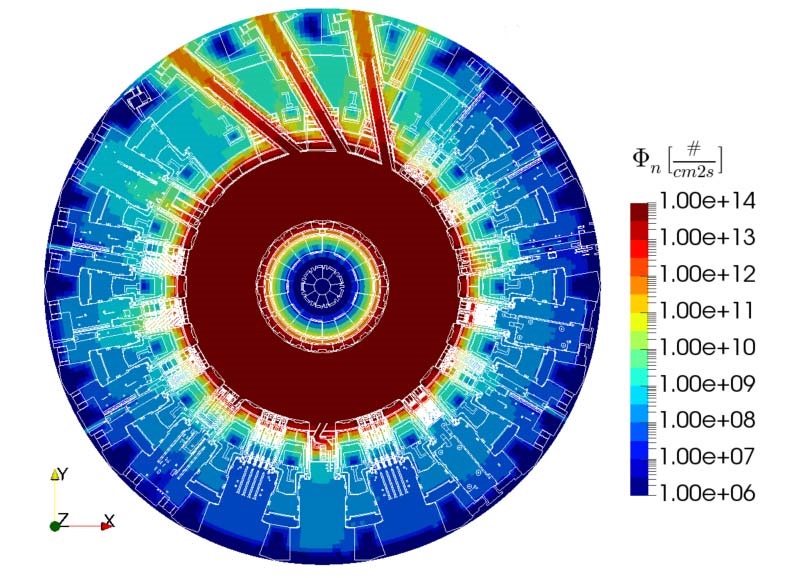
Neutron flux across the ITER Tokamak. This kind of maps are obtained thanks to radiation transport codes such as D1SUNED. © F4E
F4E has participated in the Symposium on Fusion Technologies (SOFT) held in September in Dubrovnik, Croatia. It has been an occasion to share knowledge and interact with the main stakeholders in fusion: ITER Organization, EUROfusion, UKAEA and many other universities, laboratories and industry partners that were there to get the latest news and hear about new opportunities in the field.
One of the most expected parts of the event was the ceremony of the SOFT Innovation Prize. Organised by the European Commission, the prize aims at promoting an entrepreneurial culture in fusion research by recognising outstanding researchers or industries that find innovative solutions to fusion challenges. An independent jury composed of experts in technology transfer selected the three winners. The second and third prizes have been awarded to technologies developed – at least partially – in the framework of a collaboration with F4E.
The second prize was for UNED, for the development of an improved radiation transport code for dose rate evaluation in fusion applications. Neutrons coming from fusion reactions activate materials, resulting in what experts call a “residual radiation” which requires laborious calculations to be correctly determined. The D1SUNED code allows to perform these calculations and obtain relevant data for safety and radioprotection studies.
Patrick Sauvan, UNED, gives us more details. “The development of the D1SUNED code started in 2014. The idea was to provide a code as easy to use as the standard transport code used in fusion neutronics (MCNP).” The F4E Analysis and Codes Group usually relies on UNED to perform this kind of tasks, and D1SUNED is used in several contracts, such as the neutronic support to the design of the European Test Blanket Modules. “Currently, D1SUNED is the reference code for residual radiation calculations in ITER, and it has been used to produce the radiation maps in the machine,” adds Patrick Sauvan.
The third prize was for KIT and Diamond Materials, for the development of diamond window technology used as vacuum and confinement barrier. The ITER Electron Cyclotron system will launch powerful microwaves that will travel through similar windows to heat the plasma. Diamond discs used in these windows must be “optical grade”: able to transmit the microwave beam with minimal heating of the material. The windows will also prevent the escape of any gas coming from the vacuum vessel.
“Analyses and codes, prototyping and testing, and microwave absorption measurements to ensure the correct beam transmission have led to an innovative window design concept. It has also attracted the interest of industry, leading to large area diamond discs on the base of a successful diamond deposition process,” explains Gaetano Aiello, KIT Research scientist on fusion technologies.
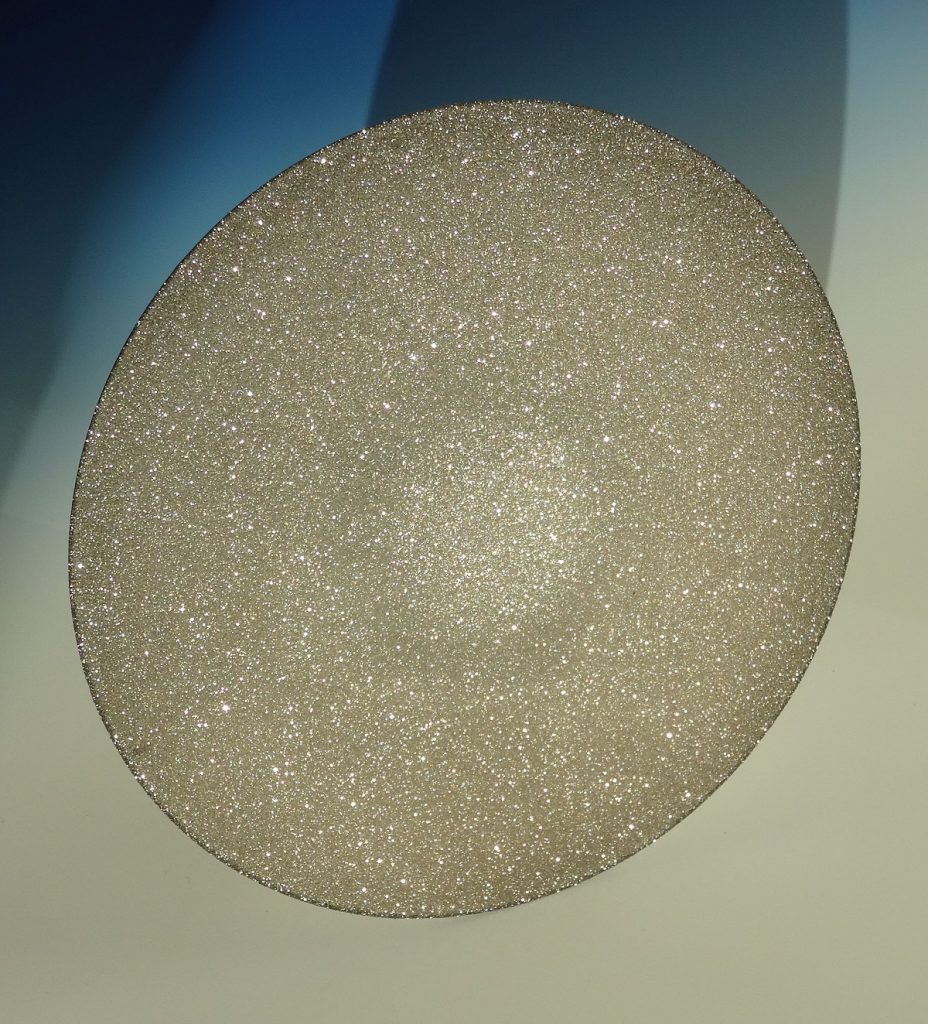
The diamond disc is manufactured by Diamond Materials. They have built on their previous work with F4E to propose a suitable component for DEMO, the fusion reactor after ITER. “The idea of a Brewster window is that you do not need to optimise the thickness of the window for a certain wavelength but you simply get your beam through it without reflection losses if you tilt the disc at a certain angle – instead of putting it perpendicular to the beam, as usual. Therefore, you can use the window for many different wavelengths,” explains Eckhard Wörner, Diamond Materials. However, there are also drawbacks: bigger discs are needed to use this configuration. They had to adapt their machinery and find process conditions to reduce stress in the discs in order to avoid crack formation during their fabrication. Many discs were tried until they had the first prototype which was then sent to KIT for microwave absorption measurements. “We had to grow and process a 180 mm optical grade diamond disc, something we and – to the best of our knowledge – no one else ever did. All in all, it was a great collaboration with KIT and a successful project,” he concludes.
KIT, together with Forschungszentrum Jülich, was also the winner of the first prize, the only one not directly linked to F4E, as it was awarded to a plasma sprayed coating that may be used as protective for the first wall of future power plants. These prizes show how, on the one hand, F4E keeps pushing industry’s limits of creativity and ingenuity to address the challenge of harnessing fusion energy and, on the other hand, F4E contractors have the knowledge and the technical and human capital to succeed. Let’s keep working together to deliver fusion!