All contracts awarded for ITER Divertor Cassette bodies

Metrology preliminary check performed on parts of ITER Divertor Cassettes bodies, Walter Tosto, Italy, September 2021. F4E has signed two contracts with Walter Tosto for the delivery of cassette bodies. © Walter Tosto
One of the ITER components to feel the blistering heat of the super-hot plasma is the divertor. Located in the lower part of the machine, it consists of 54 units known as cassettes, which will form a massive tray of roughly 142m2, where all impurities resulting from the fusion reaction will end up falling. Each cassette is made of a body, which will host a layer of components to protect its surface from the high plasma temperatures. In theory, manufacturing the pieces of this massive fusion “ash tray” may sound simple. In practice, however, the learning curve for Europe’s industry has been rather steep and that is because it is the first time such component is produced with these specifications. To make matters more complicated, there are three types of cassette bodies with subtle differences between them.
For this reason, Europe put together a procurement strategy with various stages to deliver 58 cassette bodies (54 + 4 spares). The first should be ready in 2025 and the last towards the end of 2027. The underlying rationale was to foster healthy completion between different suppliers by involving them in the process of manufacturing. How? By helping them to develop the necessary know-how, and subsequently test their skills in production. Each cassette bodies measures 0.8 x 2.3 x 3.5 m and weighs roughly 4.8 tonnes. Until recently, F4E had signed contracts for the production of 19 units. A new contract has been signed for the remaining 38 units, plus one optional, with Walter Tosto, marking the final procurement for this equipment. “We are pleased with this opportunity to increase our contribution to this fascinating project. We are proud of what we have achieved until now thanks to our involvement in fusion projects, and look forward to improving further over the next decade,” explained Luca Tosto, CEO of Walter Tosto Spa.
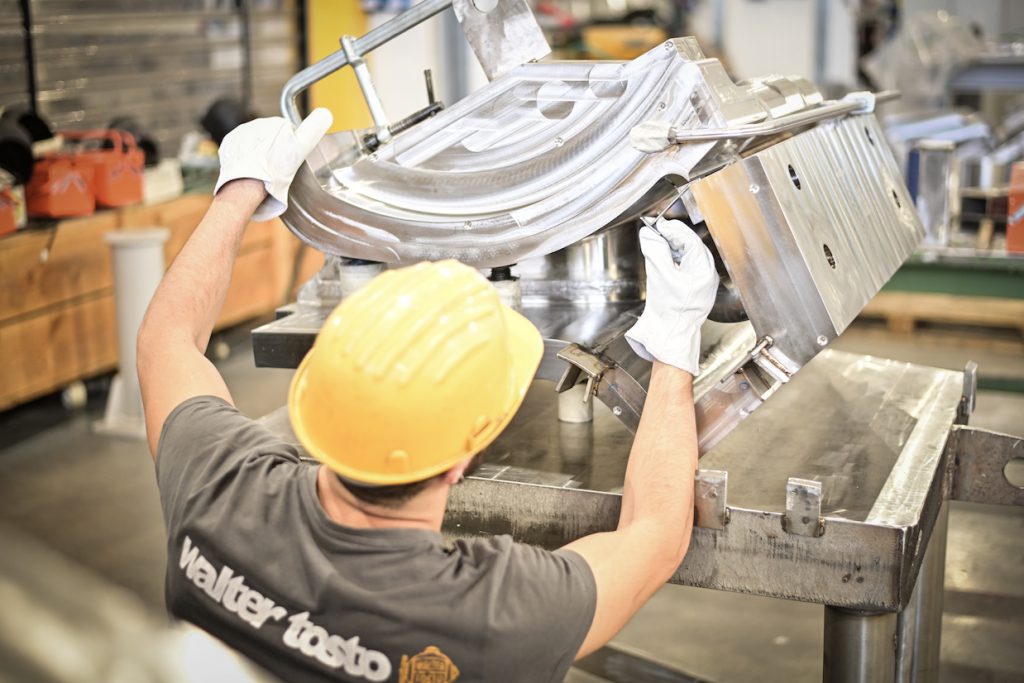
Laurent Guerrini, F4E Project Manager for the Cassettes Body, highlighted the significance of good teamwork inside and outside F4E. “In our collaboration with Walter Tosto, ITER Organization, and other F4E teams, we tried consistently to address any challenges and make sure that the final result corresponds to the demanding specifications we have. This requires team spirit, trust and open communication channels between all parties. The level of difficulty of this contract, compared to the previous ones, is twice as high in terms of documentation, materials needed and overall complexity.”
Vassilis Stamos, F4E In-Vessel Technical Officer, offers additional background. “The signature of the final contract puts project management, execution and delivery at the centre of our procurement strategy. Clearly, we are capitalising on know-how but we are also raising the benchmark in terms of volumes of production, purchase of material, supply chain and documentation. We are starting production in full speed.”
The final word rests with Patrick Lorenzetto, F4E Programme Manager for In-Vessel components. Counting years of experience in this field prior to joining F4E, now, together with his team, he has managed to sign off another big contract, which paves the way to manufacturing. “This contract is the outcome of a team endeavour and of a procurement strategy which was launched roughly eight years ago. It nurtured healthy competition during the early phases of the procurement to mitigate technical, schedule and commercial risks. The result of this process led to the best use of the European tax payers’ money.”