Europe’s first cryopump delivered to ITER
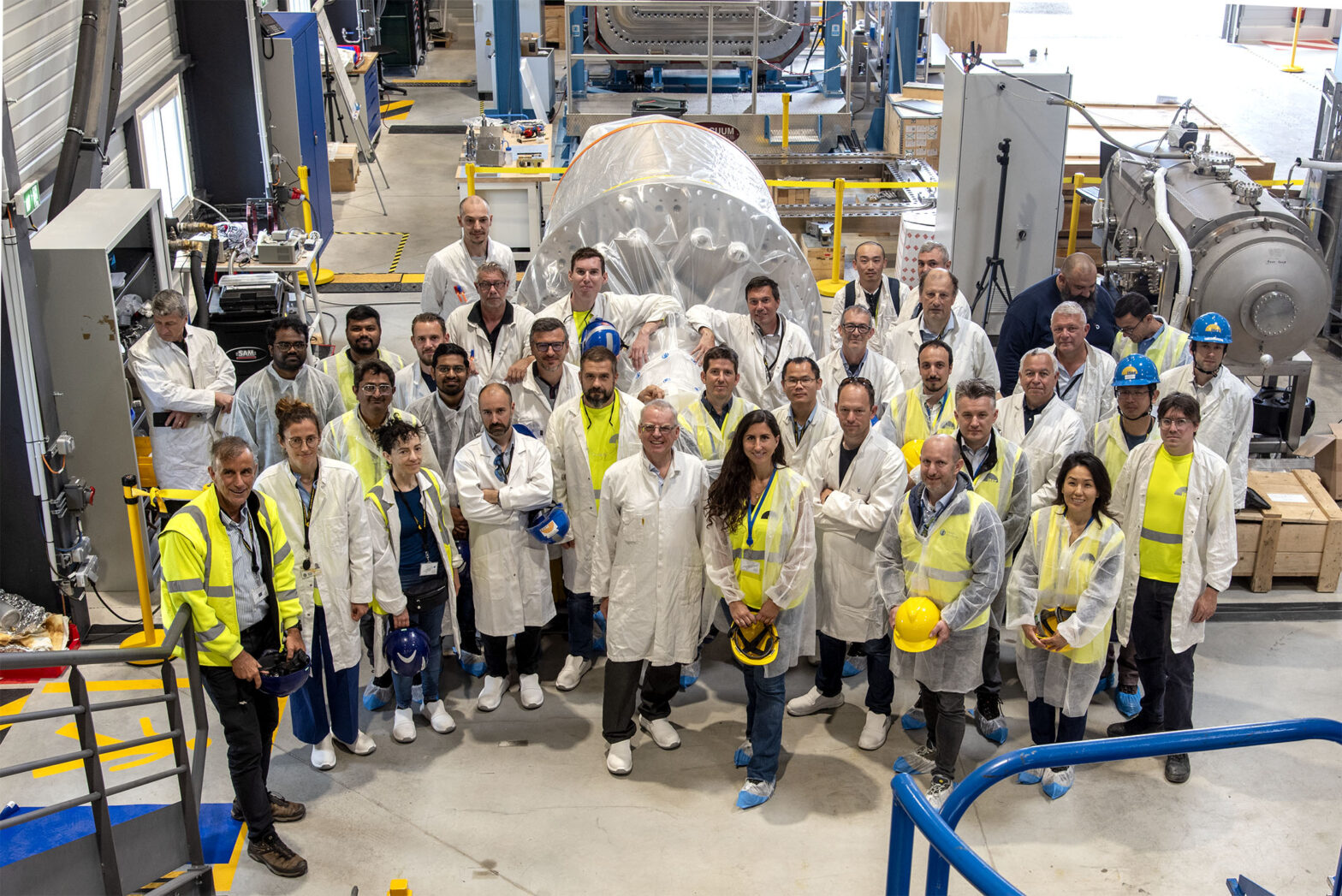
Colleagues from several partner organisations travelled to ITER to celebrate the delivery. May 2024. ©ITER Organization
ITER cryopumps can be likened to eight powerful cold traps that will suck gas out of the device. They will create and sustain the vacuum conditions inside the vacuum vessel and the cryostat by absorbing residual particles in panels at an ultralow temperature of around 4K (-269°C). Europe is responsible for providing these high-technology components, which will work hand in hand with ITER’s cryogenic network and fuel cycle.
Fusion for Energy (F4E) has been working for almost a decade for the cryopump fabrication, following the custom-made design for ITER. In 2017, a pre-production unit was handed to ITER before fabrication of the rest of the units started. Three years later, and with some slight design improvements, the European factories got back in motion, following the signature of the contract for series manufacturing with the RI – Alsymex consortium. The complexity and number of sub-components of the cryopumps called for a clockwork collaboration across European suppliers.
The chain proved to work: the first cryopump arrived this week in ITER, after completing final assembly and factory acceptance tests at Research Instruments (RI), in Germany. The teams present in Cadarache rejoiced at a milestone that paves the way for the seven remaining, all expected onsite by the first months of 2025. “We are very pleased with how our collective effort has gained traction. Behind each cryopump there are more than 20 companies, many of which specialised in advanced technological processes, such as hydroforming or electrodeposition”, claims Francina Canadell, F4E Project Manager and Technical Responsible Officer.
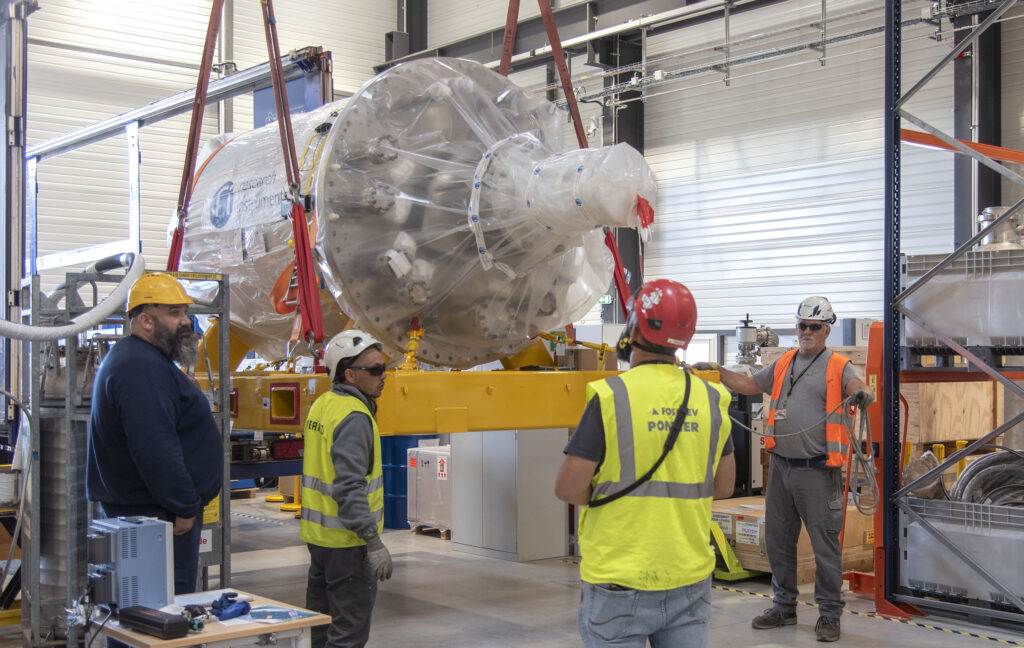
The design of ITER cryopumps took conventional ones to a new technical level – one that matched the requirements of the largest fusion device. Being connected to the interior of the reactor through a large valve system produced by Alsymex in France, the 8-tonne components are classified as nuclear safety class one. “Alsymex and its supply chain had to comply with very tight machining tolerances and extremely low leak rates, which raised the benchmark for manufacturing. We also used low-impurity stainless steels to cope with radiation”, asserts Manuel Durand, Project Manager at Alsymex.
The exceptional power of the ITER pumps lies in 28 cryopanels that act like ‘gas sponges’. They are coated with charcoal granules, a very porous material that multiplies by a thousand the actual surface on which particles can be trapped. The panels are cooled with liquid helium, fed through the Cold Valve Boxes and distributed along an intricate circuit of small pipes, fit tightly inside the pumps. It took meticulous teamwork to assemble them simultaneously, under the coordination of RI. “The skilled team with technological experts and manufacturing specialists, combined with a trustful and open collaboration with our consortium partners, F4E and ITER Organization guaranteed the successful fabrication of the first cryopump”, celebrates Dr Michael Pekeler, Director of RI.
The eight cryopumps will be the main ‘engines’ of two high vacuum systems of extraordinary size. Six pumps will work in turns to achieve the extremely low density needed in the toroidal chamber and evacuate waste gases from it, whilst two others will serve the cryostat.
F4E’s investment in the production of the cryopumps amounts to 21M. Once the eight are in ITER, they will undergo more tests and await their turn to vacuum ITER clean.