How to measure how much radiation is emitted by the ITER plasma?
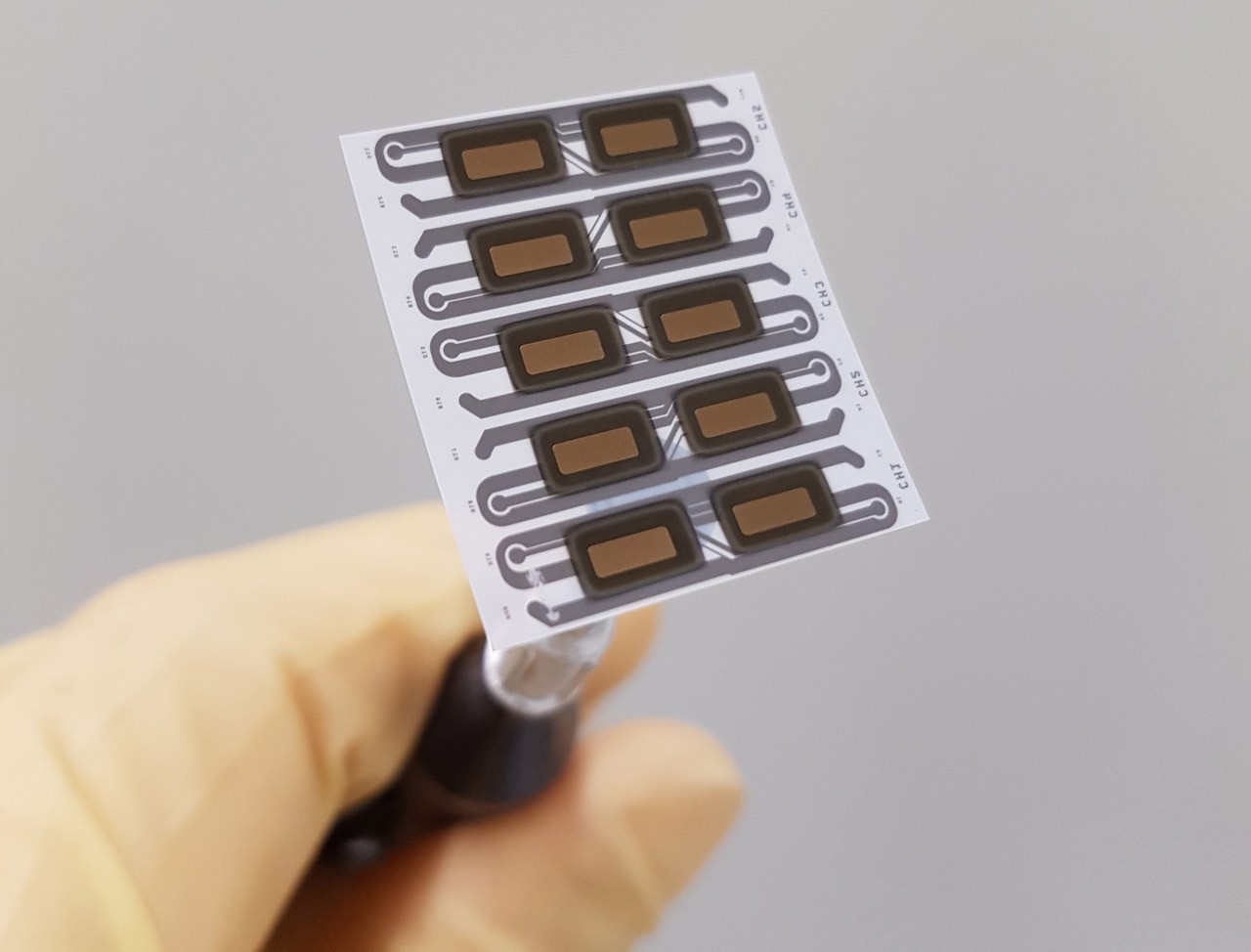
5-channel self-supporting substrate prototype sensor produced by CSEM, held up by means of a vacuum pen. It has ten blackened gold absorbers, and platinum tracks are visible through the zirconia substrate.
The ITER plasma will emit radiation. This is an important parameter for monitoring and optimising the plasma conditions. The sensors that experts use to measure the amount of radiated power are called bolometers.
ITER requires about 500 bolometer channels that will be installed inside the vacuum vessel, and will need to resist its harsh environment and remain operational for 20 years. They consist of a substrate or membrane with a thin layer of gold absorber on one side and with resistor tracks of platinum on the other. Bolometer sensors are commonly used in fusion experiments. However, for ITER, bolometers have to meet more demanding requirements than in any other fusion facility to date.
In order to maximise the likelihood of success, in 2017 F4E started a programme for prototyping and testing of two types of bolometers with several manufacturers. This strategy has resulted in the production of the first set of successful prototype sensors for ITER by two different research organisations. CSEM (Switzerland) and Fraunhofer-IMM (Germany) have produced the so-called self-supporting substrate bolometers, whereas Fraunhofer-IMM has also produced supported-membrane bolometers. F4E experts have received 18 prototypes of each type and now it is their turn to test them.
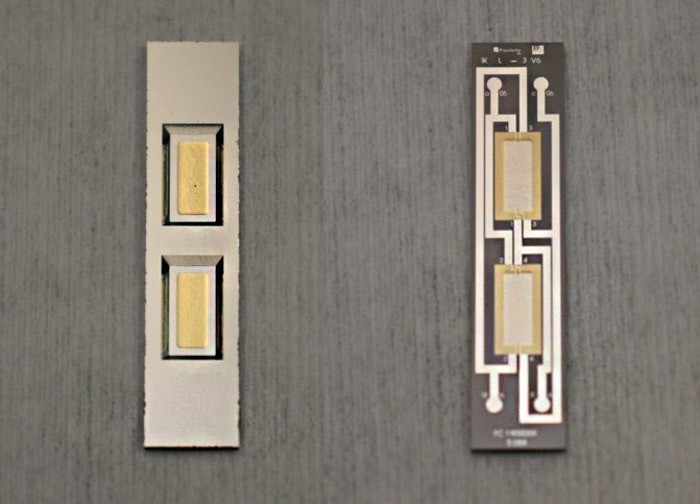
“The various technical challenges that arose during the programme show that we are pushing the limits of the technology. Both manufacturers, who are experts in the thin-film sensor technology field, overcame those challenges professionally and managed to manufacture the prototype sensors according to specifications,” states Christian Ingesson, F4E Manager of the Bolometer Project.
As part of the manufacturing, all delivered prototypes were demonstrated to withstand several temperature cycles up to 400°C, a key aspect in which previous attempts with other designs had failed. Still, the team at F4E will perform other tests (including radiation and steam exposure) on the prototypes to make sure they are suitable for ITER. At least one type of sensor is expected to fulfil the requirements and will thus be incorporated in the bolometer diagnostic that F4E will supply to ITER.